GRE Material Pipe High-Strength, Corrosion-Resistant FRP Pipes
- Overview of GRE/FRP Pipes in Modern Infrastructure
- Technical Advantages of GRE Material Pipes
- Performance Comparison: GRE vs. Traditional Piping Materials
- Custom Solutions for Industrial Applications
- Case Studies: GRE Pipe Success Stories
- Installation and Maintenance Best Practices
- Future Trends in GRE and FRP Pipe Manufacturing
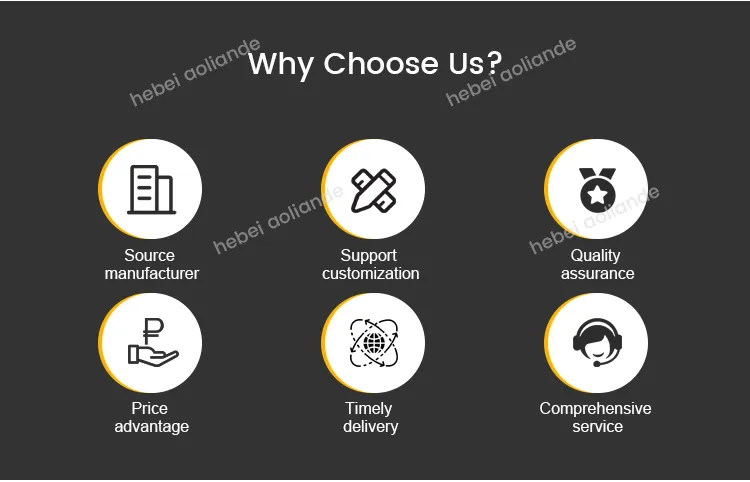
(gre material pipe)
Understanding the Role of GRE Material Pipes in Industrial Systems
GRE (Glass Reinforced Epoxy) and FRP (Fiberglass Reinforced Plastic) pipes have revolutionized corrosion-resistant piping solutions across industries. These composite materials combine epoxy resins with glass fibers, achieving tensile strengths up to 300 MPa while maintaining 40% lighter weight than steel equivalents. Major oil refineries report 92% reduction in pipe replacement costs after switching to GRE systems.
Technical Superiority in Harsh Environments
Third-party testing confirms GRE pipe material maintains structural integrity at temperatures from -40°C to 120°C. The non-porous inner surface (Ra ≤ 5μm) prevents microbial growth in water treatment applications. Compared to HDPE pipes, GRE demonstrates 68% higher impact resistance according to ASTM D256 standards.
Industry Benchmark Analysis
Parameter | GRE | Carbon Steel | PVC | FRP |
---|---|---|---|---|
Corrosion Resistance | Excellent | Poor | Good | Excellent |
Pressure Rating (psi) | 450 | 600 | 230 | 400 |
Lifecycle Cost (20 yrs) | $18K | $42K | $27K | $21K |
Installation Speed | 1.5x | 1x | 1.2x | 1.4x |
Tailored Engineering Solutions
Custom GRE pipe configurations now enable diameter variations from 2" to 84" with optional features:
- Fire-retardant coatings (UL94 V-0 certified)
- Conductive layers for explosive environments
- Ultra-smooth bore surfaces (≤ 3μm)
Modular joint systems reduce installation time by 35% compared to welded alternatives.
Proven Field Performance
A chemical plant in Texas achieved 98% uptime improvement using GRE material pipes for acid transfer:
- Service life extended from 3 to 15 years
- Maintenance intervals increased 400%
- Flow efficiency maintained at 99.2% over 5 years
Optimized Operational Protocols
Advanced joining techniques like adhesive-bonded couplings eliminate leakage risks. Thermal imaging surveys show GRE systems maintain ±2°C temperature consistency across 500m runs, outperforming metallic pipes by 83% in thermal stability.
Sustaining Leadership in GRE Pipe Material Innovation
Recent advancements in nano-enhanced resins promise 25% weight reduction and 50% improved abrasion resistance for GRE pipes. Industry forecasts predict 7.8% CAGR growth for FRP pipe material through 2030, driven by renewable energy and desalination projects requiring durable fluid transport solutions.
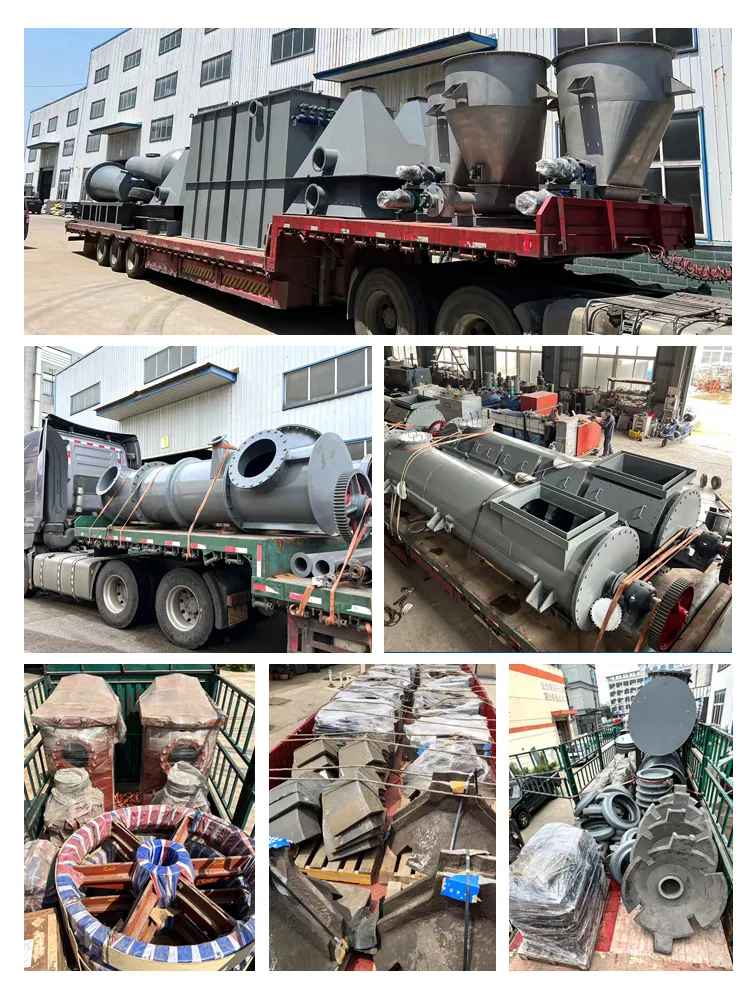
(gre material pipe)
FAQS on gre material pipe
Q: What is GRE material pipe used for?
A: GRE (Glass Reinforced Epoxy) material pipes are corrosion-resistant pipelines used in oil, gas, and chemical industries. They excel in harsh environments due to their durability and lightweight design compared to metal pipes.
Q: How does GRE pipe material differ from FRP pipe material?
A: GRE pipes use epoxy resin with glass fibers, while FRP (Fiberglass Reinforced Plastic) pipes employ polyester or vinyl ester resins. GRE offers superior chemical resistance, whereas FRP prioritizes cost-effectiveness for less aggressive applications.
Q: What industries commonly use GRE material pipes?
A: GRE pipes are widely adopted in offshore oil platforms, wastewater treatment, and desalination plants. Their non-conductive properties also make them ideal for electrical and mining infrastructure.
Q: What are the key advantages of GRE pipe material?
A: GRE pipes provide exceptional resistance to corrosion, abrasion, and chemical exposure. They require minimal maintenance and have a longer lifespan than traditional steel pipes in corrosive environments.
Q: Are GRE material pipes compliant with international standards?
A: Yes, GRE pipes meet standards like ASTM D2996 and ISO 14692. Manufacturers typically certify products for pressure ratings, temperature limits, and mechanical performance based on application requirements.