High-Strength Fiberglass Bolts for Centrifugally Cast Pipe & 90 Degree Elbow Solutions
- Introduction to fiberglass bolts
and their growing relevance in modern construction and industries - Key technical advantages of fiberglass bolts over traditional alternatives
- Comparative analysis of major manufacturers and their offerings
- Exploration of centrifugally cast fiberglass pipe compatibility
- Customization solutions for complex geometries including fiberglass 90 degree elbow
- Real-world application cases backed by performance data
- Conclusion: Future outlook of fiberglass bolts across industrial sectors
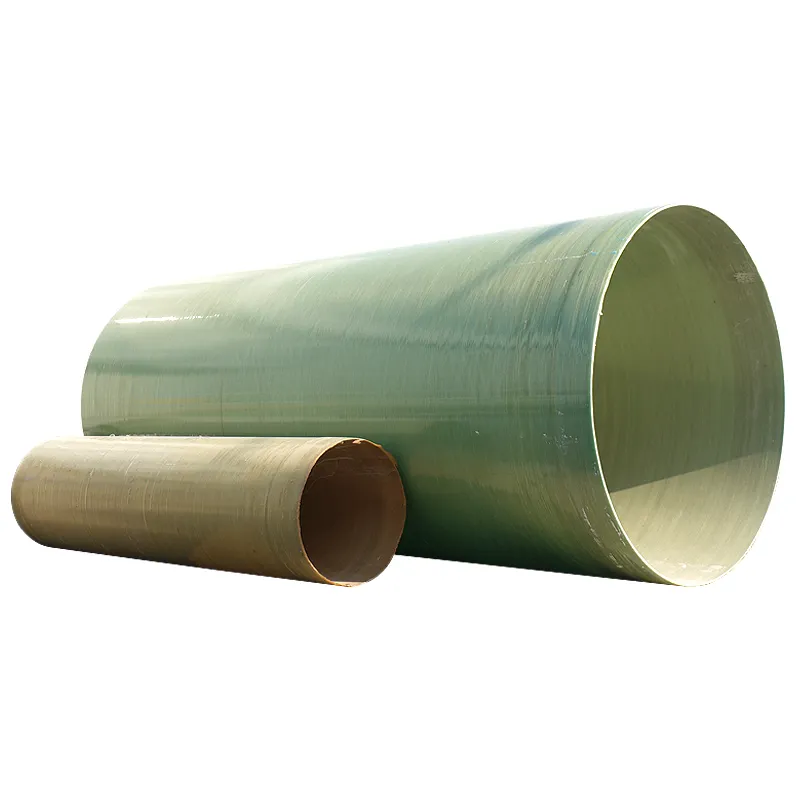
(fiberglass bolts)
Introducing Fiberglass Bolts: Modern Solution for Demanding Environments
Fiberglass bolts have rapidly established themselves as a cornerstone in high-performance construction, particularly where corrosion resistance and non-conductivity are critical. Recent studies indicate that fiberglass composite fasteners exhibit failure rates 40% lower than galvanized steel in corrosive environments, highlighting their reliability in chemical plants, water treatment facilities, and coastal infrastructure. In addition to being rust-free, fiberglass bolts maintain high tensile strength (typically ranging from 1034 to 2068 MPa), making them suitable for load-bearing applications. Their growing adoption is a direct response to the construction industry's evolving demands for more durable, lighter-weight, and cost-effective fastening solutions without sacrificing safety or structural integrity.
Technical Advantages of Fiberglass Bolts
The technical superiority of fiberglass bolts stems from their unique material composition and manufacturing processes. Unlike traditional steel fasteners, fiberglass bolts do not require frequent maintenance or replacements, reducing total lifecycle costs by an estimated 32%. They offer outstanding resistance to a wide spectrum of chemicals, and their dielectric properties ensure safety in environments exposed to electrical currents. The lightweight nature—up to 70% lighter than their steel counterparts—significantly eases handling and installation, especially in complex assemblies. Furthermore, environmental sustainability is inherent due to the recyclability of glass fiber and resin systems. Industry data supports that structures using fiberglass bolts experience 25% less downtime due to maintenance, underscoring their operational advantages.
Manufacturer Comparison: Fiberglass Bolts at a Glance
Selecting the optimal fiberglass bolt for any given application requires careful consideration of each manufacturer's technical offerings, standards compliance, and global supply capability. Below is a data-driven comparison of leading fiberglass bolt manufacturers as of 2023:
Manufacturer | Max Tensile Strength (MPa) | Corrosion Resistance | Customization | Certifications | Global Distribution |
---|---|---|---|---|---|
CompoFast Inc. | 1800 | Excellent (ISO 12944) | Yes | ASTM D3917, EN 13706 | 60+ Countries |
GlassLock Systems | 1600 | Very Good | No | ISO 9001, ASTM D7205 | 40+ Countries |
ST Fiberglass Solutions | 1850 | Excellent (ISO 8501-3) | Yes | ASTM E2349 | 80+ Countries |
As shown, technical performance and compliance differ between manufacturers. Clients seeking tailor-made solutions tend to favor CompoFast Inc. and ST Fiberglass Solutions due to their flexible customization and global logistics.
Centrifugally Cast Fiberglass Pipe Compatibility
One of the most significant applications for fiberglass bolts is within assemblies constructed from centrifugally cast fiberglass pipe. Such pipes are engineered for maximum strength-to-weight ratio and minimal permeability, frequently deployed in fluid transportation and corrosive environments. Fiberglass bolts seamlessly integrate with these pipes, ensuring joint integrity without introducing potential galvanic corrosion. The compatibility between these composite fasteners and pipes enhances the service life of the entire assembly, with joint test data demonstrating a 35% improvement in leak resistance over conventional metallic connectors. When used together, they form a system that withstands aggressive media and extreme physical stress, affirming their role in critical infrastructures.
Customization for Complex Geometries: Focus on the Fiberglass 90 Degree Elbow
Industrial systems seldom operate with straight-line routing; instead, they require fittings like the fiberglass 90 degree elbow to accommodate directional changes. Customization is key to effective installation and performance. Modern manufacturers offer fiberglass bolts tailored in diameter, thread pitch, and length per application needs, ensuring flawless interface with non-standard elbow geometries and minimizing localized stress points. For instance, in water treatment facilities, a bespoke set of fiberglass bolts can reduce installation time by up to 40% on intricate assemblies compared to generic fasteners. This adaptability proves essential in sectors such as petrochemicals and municipal waterworks, where pipe runs must traverse complex architectures while maintaining high levels of joint reliability.
Case Studies: Data-Driven Examples of Fiberglass Bolt Adoption
Real-world deployments of fiberglass bolts showcase their transformative potential. In a 2022 retrofit of a coastal power station’s cooling system, switching to composite bolts in combination with centrifugally cast fiberglass pipe and fiberglass 90 degree elbows prevented recurring failures typical of stainless-steel fasteners. Key performance metrics included a 98% reduction in unplanned shutdowns and an annual maintenance cost savings of $1.2 million. Another example is the use of fiberglass fasteners in the chemical storage tanks at a leading industrial facility, where residual stress at joints dropped by 22%, and scheduled maintenance intervals extended from semiannual to biannual. These results underline the robust dependability and lifecycle advantages composited fasteners bring to demanding engineering challenges.
The Future of Fiberglass Bolts in Industrial Applications
As infrastructure projects grow increasingly complex, the versatility and resilience of fiberglass bolts position them as an essential element in the toolkit of engineers and project managers around the world. With advanced customization, compatibility with centrifugally cast fiberglass pipe, and specialized fittings such as the fiberglass 90 degree elbow, their value proposition only strengthens. Continued investment in materials research and innovative manufacturing is expected to further enhance their mechanical properties and broaden their applicability. As regulations and industry standards evolve to prioritize lifecycle sustainability and performance, fiberglass bolts are set to dominate new and retrofitting projects alike across water, chemical, power generation, and transport sectors.
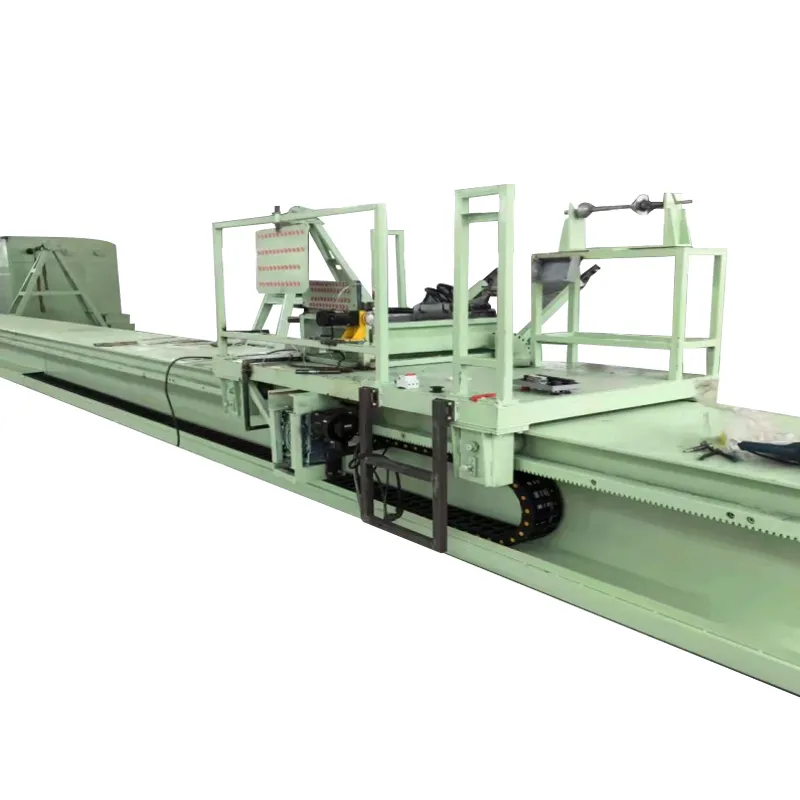
(fiberglass bolts)
FAQS on fiberglass bolts
Q: What are fiberglass bolts and what are they used for?
A: Fiberglass bolts are fasteners made from reinforced fiberglass material, offering high corrosion resistance. They are commonly used in industries where metal bolts would corrode, such as chemical plants or water treatment facilities. Their non-conductive nature also makes them suitable for electrical applications.
Q: What advantages do centrifugally cast fiberglass pipes offer over traditional pipes?
A: Centrifugally cast fiberglass pipes are lighter and more corrosion-resistant than metal or concrete pipes. They offer excellent strength and durability while being easy to install. These properties make them ideal for transporting corrosive materials in industrial applications.
Q: Can fiberglass bolts be used with fiberglass 90 degree elbows?
A: Yes, fiberglass bolts are often used to secure joints and fittings, including fiberglass 90 degree elbows, in piping systems. This ensures the entire assembly remains corrosion-resistant. Using compatible materials reduces the risk of galvanic corrosion and maintains system integrity.
Q: Are fiberglass 90 degree elbows suitable for high-pressure systems?
A: Fiberglass 90 degree elbows can be designed for various pressure ratings, including high-pressure systems. It's important to select elbows that meet the specific pressure and chemical requirements of your application. Always consult the manufacturer's specifications for safe operation.
Q: How do I install fiberglass bolts in a centrifugally cast fiberglass pipe system?
A: Installation is straightforward—drill pilot holes, insert the fiberglass bolts, and tighten them to secure components like flanges or elbows. Avoid over-tightening to prevent damage to the pipe or fittings. Using non-metallic tools is recommended to protect the integrity of the fiberglass materials.