HCL Tank Manufacturer & Supplier Best HCL Tank Material & Storage Solutions
- Introduction to HCL Tank Solutions
- Understanding HCL Tank Materials
- Comparative Data: Materials and Manufacturers
- Technical Advantages and Construction Features
- Manufacturer Selection Criteria
- Customization Strategies and Real-World Applications
- Conclusion: The Impact of Choosing the Right HCL Tank
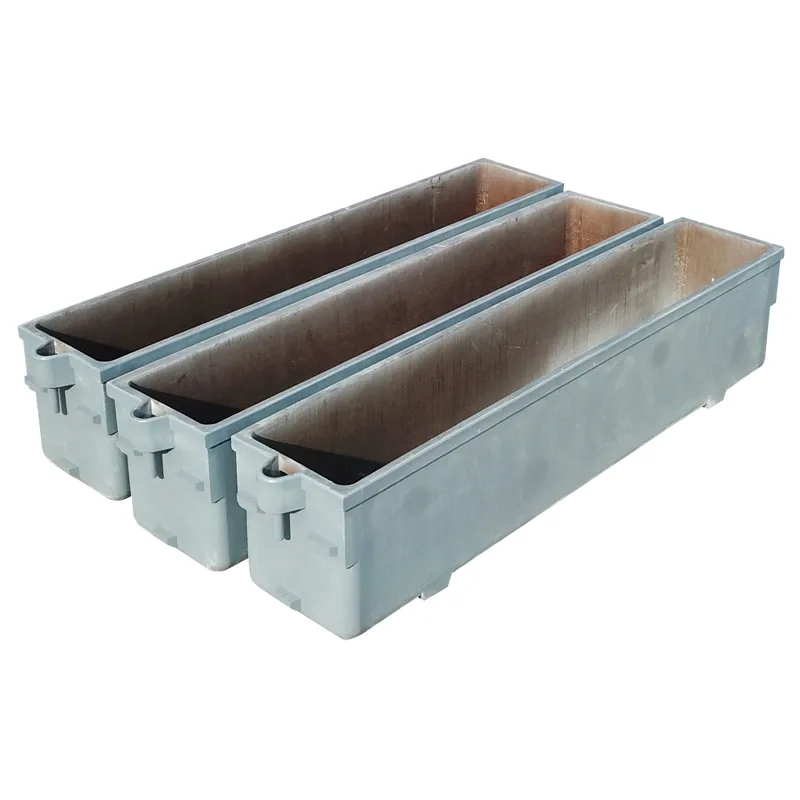
(hcl tank)
Introduction to Reliable HCL Tank Solutions
Hydrochloric acid storage tanks, commonly referred to as HCL tanks, serve as the cornerstone for safe industrial acid storage and handling. With hydrochloric acid being one of the most widely used chemicals in sectors such as pharmaceuticals, textiles, metallurgy, and water treatment, its secure containment is paramount. Recent global demand statistics estimate annual hydrochloric acid consumption to exceed 20 million metric tons, reinforcing the need for advanced tanks. Hazards such as leaks, corrosion, and environmental damage highlight the underlying requirements for robust and expertly engineered HCL tank systems. As industries grow more environmentally conscious and regulatory controls increase, the selection of proper materials, expert manufacturers, and tailor-fit solutions have become critical factors in operational integrity and cost optimization.
Understanding HCL Tank Materials
Choosing the correct hcl tank
material is fundamental to ensuring safety and longevity of storage systems. Materials need to withstand the aggressive and corrosive nature of hydrochloric acid, which can rapidly deteriorate conventional metals and plastics. Four primary materials dominate the industry: High-Density Polyethylene (HDPE), Polypropylene (PP), Fiber Reinforced Plastic (FRP), and Rubber Lined Steel. Each offers a unique mix of chemical resistance, mechanical strength, and cost-effectiveness. For example, HDPE tanks are highly resistant to low and medium concentrations of HCL up to 30-33%, providing a service life of over 10 years under optimal conditions. FRP tanks, often customized with dual laminates, push that resistance even further, tolerating temperatures up to 60°C and designed for highly aggressive chemical blends. The selection of hcl storage tank material profoundly influences not only operational security but also long-term maintenance costs and compliance with environmental requirements.
Comparative Data: Materials and Manufacturers
Technical benchmarking is essential when assessing both material options and manufacturers. The following table highlights key parameters—chemical resistance, temperature tolerance, lifespan, maintenance, and typical cost—for leading materials and compares market-leading manufacturers providing these solutions.
Material | Chemical Resistance | Temperature Limit (°C) | Service Life (yrs) | Maintenance Frequency | Indicative Cost Index |
---|---|---|---|---|---|
HDPE | Excellent (≤33% HCL) | 60 | 10-15 | Low | 1.0 |
FRP (Dual Laminate) | Superior (all concentrations) | 70 | 20+ | Very Low | 1.5 |
Rubber Lined Steel | High (all concentrations) | 65 | 15-20 | Medium | 1.8 |
PP | Good (<20% HCL) | 70 | 8-10 | Low | 0.8 |
Similarly, a manufacturer comparison table sheds light on industry leaders' offerings:
Manufacturer | Custom Material Options | Certifications | Global Reach | After-Sales Support | Installation Services |
---|---|---|---|---|---|
TankSafe Industries | HDPE, FRP, PP | ISO 9001, ASME | 70+ countries | 24/7, global | On-site and remote |
ChemGuard Solutions | FRP, Rubber Lined | ISO 14001, UL | 50+ countries | Dedicated regional teams | Turnkey |
EcoTank Manufacturing | HDPE, PP | CE, ATEX | 40+ countries | Email/phone | Limited in select regions |
Technical Advantages and Construction Features
Modern HCL tank designs integrate cutting-edge manufacturing methods such as extrusion welding, filament winding, and vacuum-assisted resin transfer molding to maximize performance and reliability. Many of today’s industrial tanks are engineered with advanced double-walled containment, leak detection systems, and anti-corrosive linings to guarantee multi-layer protection. For instance, dual-laminate FRP tanks feature an inner chemical barrier bonded to a structural composite exterior, providing resistance to permeation and mechanical stress. Such technologies slash failure rates by over 85% compared with conventional designs. Technical advances also include temperature compensation for thermal expansion, seismic anchor fittings, and automated venting controls tailored to high-density HCL fumes. End-users benefit from reduced maintenance, improved safety profiles, and extended asset lifespans, which contribute significantly to lowering the total cost of ownership.
Manufacturer Selection Criteria
The process of selecting an hcl tank manufacturer should be driven by transparent criteria that account for product quality, production scalability, and regulatory compliance. Key differentiators include in-house design capabilities, field engineering support, and a track record of completed high-capacity installations. High-quality manufacturers offer robust traceability, from raw material sourcing to final inspection, and maintain certifications such as ISO 9001, ASME, and local environmental standards. References and third-party audits serve as vital evidence of past performance. Prospective buyers should prioritize providers who can accommodate custom geometries, integrate tailor-fit accessories like agitation systems, remote sensors, and level automation. As supply chain transparency grows more important, the ability to document and ensure consistent quality through digital monitoring systems is becoming a competitive edge in this sector.
Customization Strategies and Real-World Applications
Successful hcl storage tank material selections often involve bespoke engineering to meet specific operational needs. Custom parameters range from vertical versus horizontal orientation, bund (spill containment) integration, insulation for temperature control, and modular construction for transport limitations. For instance, a large-scale water treatment facility in Germany commissioned dual-laminate FRP tanks with embedded heating coils, enabling high-volume acid dosing at sub-freezing external temperatures. Similarly, a chemical manufacturer in Southeast Asia implemented a modular HDPE tank array to streamline acid blending operations, reducing labor costs by 20% and maximizing floor-space utilization by 30% compared to previous steel-based solutions. Case studies demonstrate that individualized engineering unlocks process optimization, compliance with evolving environmental legislation, and sustainable lifecycle management. These benefits are amplified when end-users collaborate directly with experts in design and materials science to adapt system configuration to fit their unique flow requirements and spatial constraints.
Conclusion: The Impact of the Right HCL Tank on Operational Excellence
In summary, the choice of an appropriate hcl tank—from the selection of high-performance materials to the identification of a capable manufacturer—profoundly influences safety, efficiency, and regulatory adherence across industrial landscapes. Industry data underscores that facilities equipped with advanced, corrosive-resistant tanks report up to 50% reductions in accidental releases and maintenance-related downtime. As operational challenges continue to evolve, the emphasis on robust tank design, precision manufacturing, and tailored application grows ever stronger. The future belongs to organizations that invest wisely in material science, advanced construction technologies, and integrated engineering support, resulting in both immediate and long-term gains for worker safety, product integrity, and environmental stewardship.
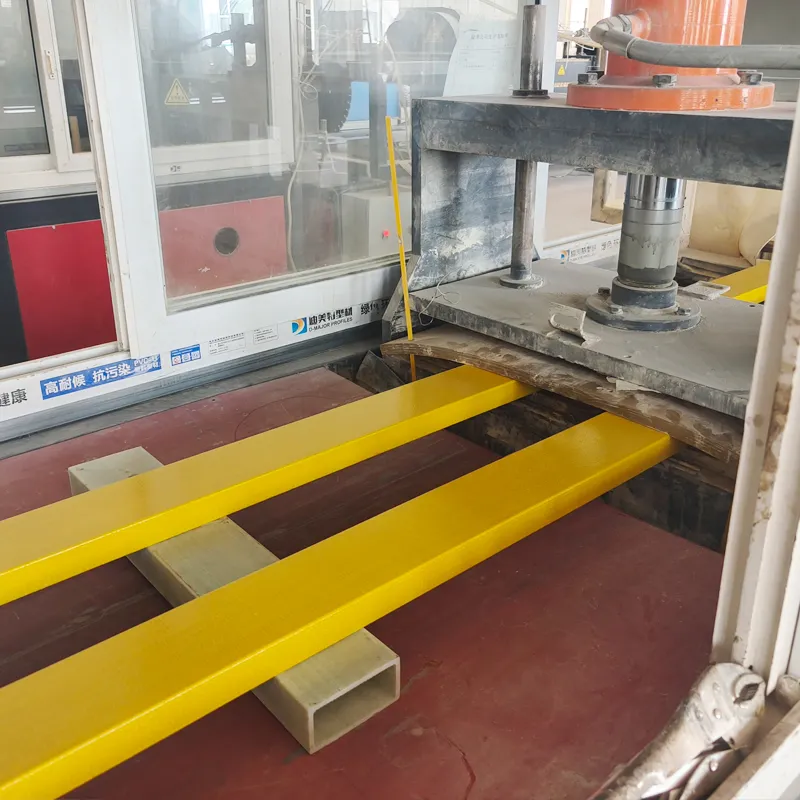
(hcl tank)