High-Quality Fiberglass Reinforced Plastic Tanks Durable FRP Vessels for Industrial Use
- Introduction to fiberglass reinforced plastic tanks
- The technology behind fibre reinforced plastic tanks and vessels
- Comparative analysis of leading manufacturers
- Customization capabilities and options
- Applications and case studies across industries
- Environmental and operational benefits
- Conclusion: Why choose fiberglass reinforced plastic tanks
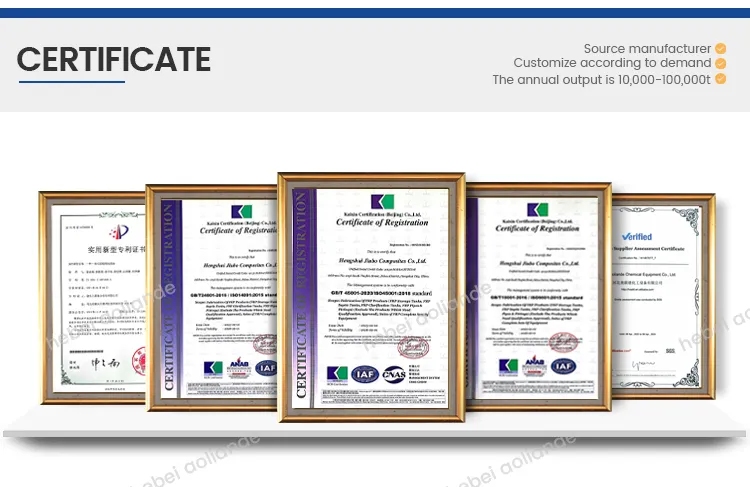
(fiberglass reinforced plastic tanks)
Introduction to Fiberglass Reinforced Plastic Tanks: Industry Evolution and Demand
Over recent decades, fiberglass reinforced plastic tanks (FRP tanks) have become the backbone of critical storage solutions in industries ranging from chemicals to food processing. The global market for fibre reinforced plastic tanks and vessels exceeded USD 2.5 billion in 2022 and is projected to reach USD 4.1 billion by 2028, growing at a CAGR of 7.6%.1 This robust growth is driven by stringent industry standards, corrosion resistance demands, and evolving regulations regarding material sustainability. Unlike traditional steel or concrete counterparts, FRP tanks offer a weight reduction of up to 70%, contributing to easier transportation and installation. Additionally, maintenance costs are reduced by 60% on average over a tank’s lifecycle due to exceptional chemical resistance and structural longevity.2
The Technology Behind Fibre Reinforced Plastic Tanks and Vessels
At the core of FRP tank technology is the potent synergy between glass fiber reinforcements and a polymer matrix, typically thermosetting resins such as epoxy, vinyl ester, or polyester. These materials are meticulously layered and cured, resulting in containers that boast tensile strengths exceeding 1,000 MPa and flexural strengths above 900 MPa.3 The design flexibility—cylindrical, rectangular, horizontal, or vertical—makes them ideal for safe storage of aggressive acids, alkalis, potable water, and even food-grade ingredients. Internal linings can be engineered for special requirements such as UV or thermal resistance, utilizing laminate thickness calculations and finite element analysis to ensure precise mechanical properties. Automated filament winding and hand lay-up techniques guarantee uniformity and repeatability, aligning with ASTM D3299 and BS4994 standards for pressure and atmospheric tanks.
Comparative Analysis of Leading Manufacturers
To aid in procurement decisions, the following table presents a comparative analysis of four globally established FRP tank manufacturers, focusing on production capacities, certifications, warranty offerings, and after-sales services:
Manufacturer | Annual Output (Units) | Key Certifications | Standard Warranty | After-sales Support | Custom Design Capabilities |
---|---|---|---|---|---|
ProTank Solutions | 10,000 | ISO 9001, NSF/ANSI 61, ASME RTP-1 | 10 Years | 24/7 Onsite, Online Monitoring | Yes - Up to 500,000 gal |
FiberServe Industries | 6,500 | ISO 14001, API 650 FRP, FDA | 5 Years | Phone, Annual Inspection | Yes - Modular Configurations |
EcoTank Manufacturing | 8,200 | WRAS, UL 1316, ATEX | 8 Years | Email, Video Support | Yes - Nonstandard Geometries |
PlastiGlass Engineering | 12,000 | EN 13121, PED, GOST | 12 Years | 24/7 Global Field Team | Yes - High-pressure Designs |
This comparison highlights how the choice of supplier impacts long-term operability and compliance outcomes. Products certified to standards such as NSF/ANSI 61 and API 650 offer proven assurances in potable water and petroleum industries, ensuring safe containment and operational integrity.
Customization Capabilities and Options
No two storage requirements are identical, and the adaptability of fiberglass reinforced plastic leads the industry in tailored solutions. Modern FRP suppliers empower clients with computer-aided design (CAD), allowing vessels to be engineered down to the flange, nozzle, and interior lining specifications. Common customization options include:
- Volume capacities ranging from 100 liters to over 1,000,000 liters
- Wall thicknesses from 4 mm up to 60+ mm for pressure or vacuum resistance
- Dual laminate designs (FRP with thermoplastic liners) for highly corrosive storage
- Specialized linings for thermal, UV, or abrasion protection
- Horizontal or vertical orientations, modular panelized tanks
- Embedded sensors for level and leak detection
- Integrated sumps, manways, and support legs or saddles
Customization is also available for extreme temperatures (from -60°C to +120°C operating ranges), seismic zones, and wind load compliance. In complex scenarios, finite element modeling is employed to validate custom tank integrity before manufacturing.
Applications and Case Studies Across Industries
The versatility of fibre reinforced plastic tanks and vessels is showcased in a vast array of industrial and municipal applications:
- Chemical Processing: FRP tanks endure aggressive solvents, acids, and corrosives. For example, a leading fertilizer plant in Texas deployed 16 x 50,000-gallon FRP acid storage tanks, which reduced maintenance downtime by over 65% versus previous steel tanks.
- Water and Wastewater Treatment: Municipalities widely use FRP vessels. A city in Northern Europe replaced failing concrete clarifiers with FRP clarifiers, reporting a 15-year lifespan extension and a 78% reduction in structural failures.
- Food & Beverage: Hygienic-grade, FDA-compliant FRP tanks safely store syrups and juices in large beverage operations across Southeast Asia, providing contamination-free payloads and easier sterilization.
- Pharmaceutical: Cleanroom-ready FRP vessels with smooth liners are widely used for active ingredient containment and process intermediates, helping a multination pharma group in India achieve a near-zero microbiological risk in storage.
- Energy & Power: Lightweight FRP solutions have replaced metal tanks on offshore platforms in the North Sea, slashing deck loads and decreasing corrosion-related leaks by 91% in harsh saltwater environments.
Case studies consistently demonstrate improved lifecycle costs, enhanced safety metrics, and compliance achievements, positioning FRP as the premier choice in mission-critical storage.
Environmental and Operational Benefits
FRP tank technology delivers both ecological and economic value. Unlike metals, the primary raw materials are non-toxic, and manufacturing processes continually strive for reduced VOC emissions and energy consumption per unit produced. FRP tanks are fully recyclable and their thermal insulation properties reduce condensation and minimize heat loss, especially when compared to single-walled steel or aluminum tanks. Operators benefit from:
- Service life exceeding 30 years, validated by field results
- Chemical resistance performance that virtually eliminates internal coating renewal
- Downtime reduction by an average of 55% due to lower failure rates
- Lower insurance premiums thanks to enhanced containment reliability
- Lightweight design contributing to decreased crane and foundation costs, typically 40% less than equivalent metals
- Compatibility with sustainability initiatives—many vendors offer tanks manufactured from up to 35% recycled content
The operational footprint also shrinks, with modular installations enabling rapid commissioning even in confined sites, and remote monitoring options reducing manual inspection intervals.
Conclusion: Why Choose Fiberglass Reinforced Plastic Tanks
In summary, fiberglass reinforced plastic tanks offer unmatched versatility and durability, evolving year-on-year in response to complex industrial storage demands. The latest advancements in materials science and automation have resulted in vessel designs that outperform legacy solutions in safety, environmental impact, and maintenance savings. With proven records across sectors such as chemical processing, water treatment, food & beverage, and energy production, these storage solutions deliver long-term value supported by leading global manufacturers. Decision-makers benefit not only from robust compliance credentials and adaptive customization but also from quantifiable lifecycle savings, making FRP tanks the strategic choice for the future of reliable and sustainable storage infrastructure.
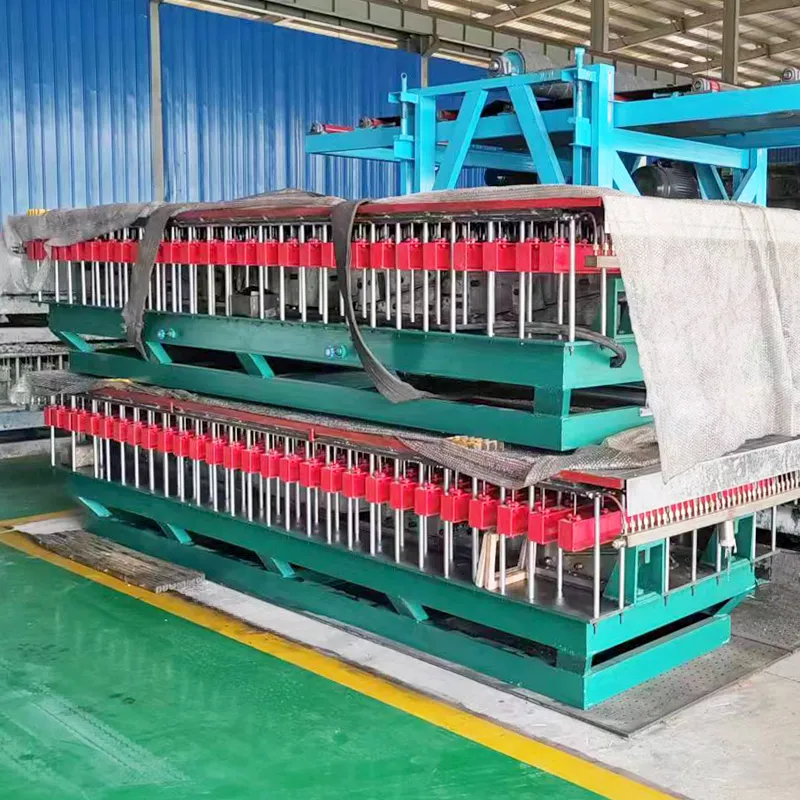
(fiberglass reinforced plastic tanks)