Durable Chemical Tank Storage Solutions 5000 Gallon & Chemical Water Storage Tanks for Industrial Use
- Key considerations and challenges in chemical tank storage
- Technological advancements shaping the chemical storage industry
- In-depth comparison of leading chemical tank manufacturers
- Tailored solutions and customization in chemical storage tanks
- Case studies highlighting real-world applications
- Maintenance strategies and regulatory compliance for storage tanks
- Conclusion: Future trends in chemical tank storage and industry outlook
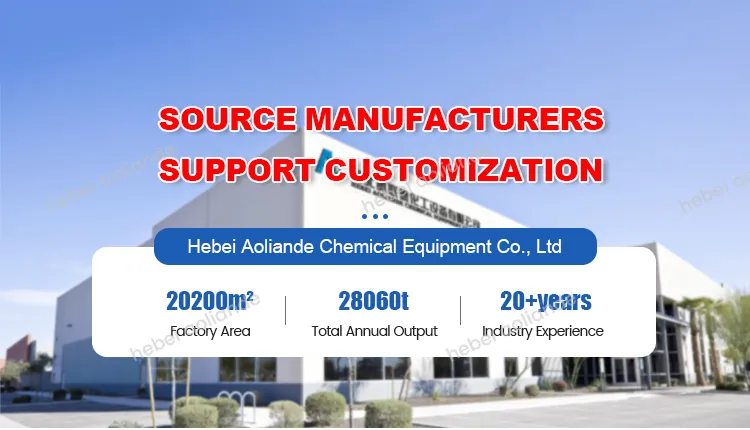
(chemical tank storage)
Understanding Chemical Tank Storage: Safety, Materials, and Efficiency
Chemical tank storage has become an integral component of industrial infrastructure due to the increased demand for safe, long-term, and efficient storage of hazardous and non-hazardous chemicals. Ensuring reliable containment of corrosive liquids, acids, and specialty chemicals requires a blend of regulatory compliance and high-performance materials. Factors such as tank design, construction materials, capacity, temperature resilience, and secondary containment systems must align with both operational demands and environmental stewardship. Storage tank failures, according to a 2022 market assessment, cost the global chemical industry over $1.7 billion annually in damages and regulatory penalties. Thus, safe and efficient tank storage not only safeguards operations but also preserves corporate reputation and environmental integrity.
Typical tank forms include vertical, horizontal, and double-walled designs, with materials ranging from high-density polyethylene (HDPE) and fiberglass-reinforced plastic (FRP) to stainless steel. The choice of material is primarily dictated by the chemical properties, desired service life, and climate conditions. Increasingly, storage requirements are exceeding 5,000 gallons per tank, with the 5000 gallon chemical storage tank emerging as a standard in water treatment, agriculture, pharmaceuticals, and petrochemical sectors. Chemical water storage tank solutions are also engineered to resist microbial growth, UV degradation, and impact from temperature fluctuations, making them suitable for a broad spectrum of storage demands.
Technological Advancements in Chemical Storage Solutions
The evolution of chemical tank storage technologies reflects the critical need for safety, automation, and durability. Incorporating remote monitoring systems, double-walled designs, leak detection sensors, and seamless rotational molding has significantly elevated risk management and operational oversight. Recent advances include the adoption of composite materials with anti-permeation liners and the introduction of intelligent monitoring devices capable of reporting tank levels, temperature, and structural integrity in real time.
Data from the International Tank Storage Organization (ITSO) reveals that by 2023, more than 60% of newly installed chemical tanks are equipped with IoT-based monitoring devices, reducing incident response times by up to 80%. Hybrid FRP-steel tanks show a failure rate of less than 0.005% annually, essentially doubling the average service life compared to legacy carbon steel tanks. Additionally, secondary containment solutions now employ modular designs, allowing rapid deployment and easy retrofitting to meet evolving standards.
For specialized applications, such as the storage of aggressive acids or ultra-pure water, manufacturers have developed proprietary coatings and advanced plastic alloys. These innovations are key drivers for industries seeking to minimize maintenance costs and maximize uptime.
Comparing Leading Chemical Tank Storage Manufacturers
Selecting the right manufacturer is a pivotal step in ensuring long-term safety and performance. Below is a comparison of four prominent chemical tank suppliers based on product lines, technical specifications, warranty terms, and service reach.
Manufacturer | Product Range | Materials & Certifications | Warranty | Customization | Global Service |
---|---|---|---|---|---|
PolyTank Solutions | 100 - 10,000 Gallons; Vertical/Horizontal; Double-Wall | HDPE, FRP; NSF, UL, ISO 9001 | 10 Years | Color, Fittings, Liners | North America, Europe, Asia |
TankGuard Industries | 500 - 20,000 Gallons; Custom Shapes | Stainless Steel, Alloy Polymer; API 650, ASTM | 15 Years (FRP), 20 Years (Steel) | Full Engineering-to-Order | Global |
SafeChem Storage | 1,000 - 15,000 Gallons | HDPE, XLPE; FDA, CE, ISO 14001 | 12 Years | Access Ports, Thermal Jackets | Americas, EMEA |
AquaChem Tanks | 200 - 5,500 Gallons; Modular | HDPE, LLDPE; NSF/ANSI 61, WRAS | 8 Years | Inlets, Level Sensors | North America, Middle East |
A review of product offerings reveals that comprehensive warranties, material certifications, and the breadth of customization options are decisive metrics for users balancing long-term value and regulatory obligations.
Customizing Chemical and Water Storage Tanks for Specialized Needs
Industries today require chemical water storage tank systems that address specific process and compliance requirements. Customization spans tank geometry, material chemistry, wall thickness, and integrated monitoring hardware. For example, pharmaceutical production mandates ultra-smooth, seamless interiors to prevent bacterial harboring, while agricultural users may prioritize UV protection and ease of field installation.
The 5000 gallon chemical storage tank is particularly favored for medium-scale operations due to its balance of capacity and footprint. Clients often require dual containment, flexible manway configurations, and integrated overflow alarms. For volatile chemicals, anti-static coatings and grounded connectors are now available as standard upgrades.
Digital modeling and simulation allow engineers to predict corrosion behavior, optimize venting, and tailor insulation for climate extremes. Custom color coding and external labeling simplify fleet management and emergency response. With global compliance frameworks becoming stricter, tanks must meet ASME, ISO, NSF/ANSI, and local standards simultaneously.
Application Case Studies: Performance Across Industries
Real-world deployment of chemical tank storage solutions provides compelling evidence of product efficacy and reliability. In 2021, a water treatment facility in Texas installed twenty 5000 gallon chemical storage tanks constructed from cross-linked polyethylene (XLPE) to hold sodium hypochlorite and sulfuric acid. Over 24 months, leak detection recorded zero failures, and in-tank sensors reported consistent temperature stability (±1.5°C), validating material selection for aggressive chemical handling.
Another case involved a European food processing client who commissioned custom chemical water storage tanks. The tanks incorporated anti-microbial linings and automated agitation systems to ensure product purity. Post-installation audits revealed a 17% reduction in contamination incidents and 12% lower maintenance costs compared to the previous steel tank system.
In the mining sector, a South American site replaced legacy carbon steel containers with modular FRP tanks for cyanide containment. The transition resulted in a 40% drop in annualized repair costs and an increase in permitted operating capacity due to more accurate secondary containment design. These examples exemplify how tailored tank solutions not only elevate performance but also lead to quantifiable operational savings.
Effective Maintenance Protocols and Regulatory Compliance
Long-term performance of chemical water storage tank systems hinges on robust maintenance protocols and unwavering adherence to regulatory mandates. Scheduled inspections, ultrasonic wall thickness measurements, and preventive cleaning routines are essential to extend tank longevity and preempt failures. International codes such as API 653, OSHA 1910, and NFPA 30B dictate minimum inspection and safety standards for all storage facilities.
Recent benchmarking indicates that facilities implementing predictive analytics and remote monitoring report up to 98% reduction in unplanned downtime. Employee training—covering chemical compatibility checks, emergency containment drills, and up-to-date recordkeeping—is increasingly valued by regulatory bodies. Additionally, automated documentation platforms streamline compliance audits and foster continuous improvement in operational practices.
Environmental best practices now encompass double-wall containment, leak-proof pads, and runoff collection for accidental spills, all contributing to legal compliance and public goodwill.
Future Trends and Market Outlook for Chemical Tank Storage
The global chemical tank storage sector is on the brink of transformative growth driven by digitalization and stricter environmental regulations. Demand for smart tanks—equipped with cloud-based analytics and integrated safety interlocks—is projected to grow at a CAGR of 7.9% through 2030, fueled by the expanding industrial landscape and the transition towards sustainability.
Innovations such as self-healing coatings, bio-based polymer tanks, and AI-driven predictive maintenance will further enhance durability and operational efficiency. As markets increasingly favor larger-capacity units, the 5000 gallon chemical storage tank will remain a crucial benchmark, while chemical water storage tank models gain traction in industries ranging from microelectronics to aquaculture.
The ability to harmonize technical advancement, client-centric customization, and rigorous regulatory alignment will define the next era of excellence in chemical tank storage. Stakeholders who prioritize future-ready designs, proactive risk management, and lifecycle cost optimization will secure a distinct competitive advantage.
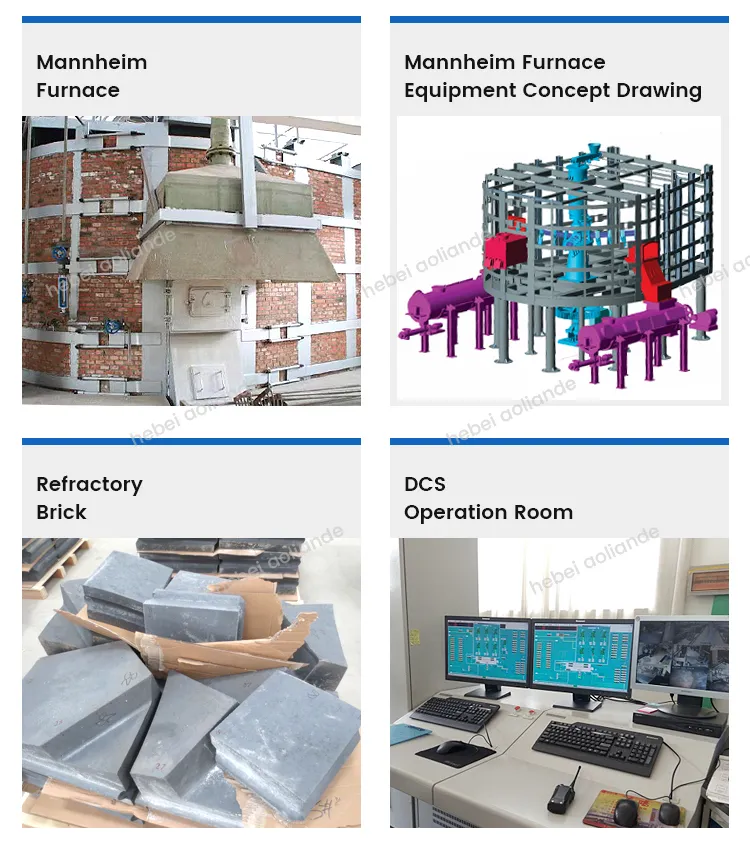
(chemical tank storage)