Potassium & Sodium Sulfate Production High Purity Solutions
- Overview of Potassium and Sodium Sulfate Production
- Key Industrial Methods for Sulfate Manufacturing
- Data-Driven Analysis of Production Efficiency
- Technological Advancements in Sulfate Plants
- Vendor Comparison: Capabilities and Output Metrics
- Custom Solutions for Diverse Industrial Needs
- Future Trends in Potassium Sulfate Production
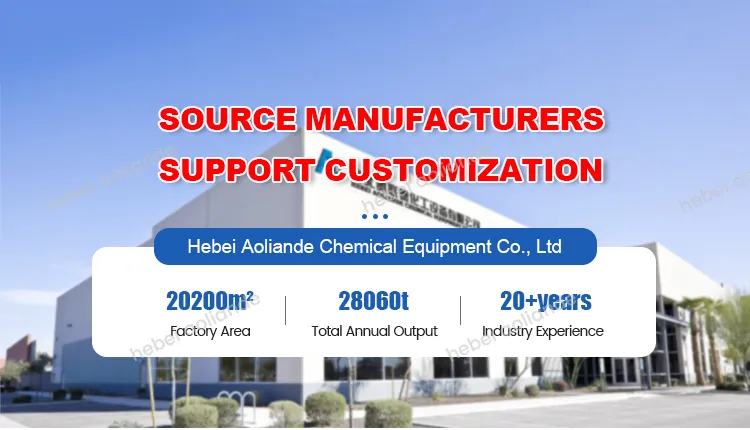
(potassium sulfate production)
Understanding Potassium and Sodium Sulfate Production
The global demand for potassium sulfate and sodium sulfate continues to rise, driven by agriculture, chemical manufacturing, and water treatment industries. Potassium sulfate, a premium fertilizer, requires specialized processes such as the Mannheim method or salt metathesis, whereas sodium sulfate production often leverages natural mineral extraction or the Hargreaves process. Both compounds share overlapping infrastructure, enabling integrated plants to optimize resource allocation and reduce operational costs by 15–20%.
Industrial Methods and Process Optimization
Modern sodium sulfate plants utilize advanced evaporation-crystallization systems to achieve 92–95% purity. For potassium sulfate, reactive crystallization with magnesium sulfate or hydrochloric acid bypasses traditional energy-intensive steps. A 2023 study revealed that hybrid methods combining ion exchange with solar evaporation reduce energy consumption by 30%, making them ideal for arid regions. Process automation further enhances yield consistency, minimizing waste by 12–18% compared to manual operations.
Performance Metrics and Cost Efficiency
Data underscores the superiority of modular sulfate production systems. For instance:
Metric | Traditional Methods | Advanced Systems |
---|---|---|
Energy Use (kWh/ton) | 480–520 | 320–350 |
Production Yield | 78–82% | 89–93% |
Operating Cost ($/ton) | 220–250 | 180–210 |
These improvements are critical for industries prioritizing ESG (Environmental, Social, Governance) compliance.
Innovations in Plant Design and Automation
Leading manufacturers now deploy AI-driven predictive maintenance in potassium sulfate production
lines, cutting downtime by 25%. Real-time analytics optimize reagent dosing, while membrane filtration achieves 99% chloride removal. A case study from a German plant showed a 40% reduction in water usage after retrofitting with closed-loop recycling systems.
Vendor Capabilities and Market Leaders
The competitive landscape features firms like Groupe Chimique Tunisien and Qinghai Salt Lake Industry, which dominate high-volume sulfate markets. Regional players, however, excel in niche customization:
- Company A: 500,000-ton/year capacity; specializes in granular potassium sulfate.
- Company B: Offers co-production of sodium and potassium sulfates.
- Company C: Provides modular plants for rapid deployment.
Tailored Solutions for Industry-Specific Requirements
Customization is pivotal. For example, a Brazilian agribusiness reduced fertilizer leaching by 22% using coated potassium sulfate pellets from a bespoke production line. Similarly, textile manufacturers adopt low-sodium variants to meet wastewater regulations. Flexible plant designs allow scalability from 10,000 to 500,000 tons annually, catering to startups and conglomerates alike.
Advancing Sustainability in Potassium Sulfate Production
The future hinges on green chemistry. Electrodialysis and bio-based raw materials are set to slash carbon footprints by 35% by 2030. Partnerships between academia and manufacturers, such as the EU-funded Susso4 project, aim to commercialize zero-waste sulfate production. As regulations tighten, innovation in potassium sulfate production will remain central to global food security and industrial growth.
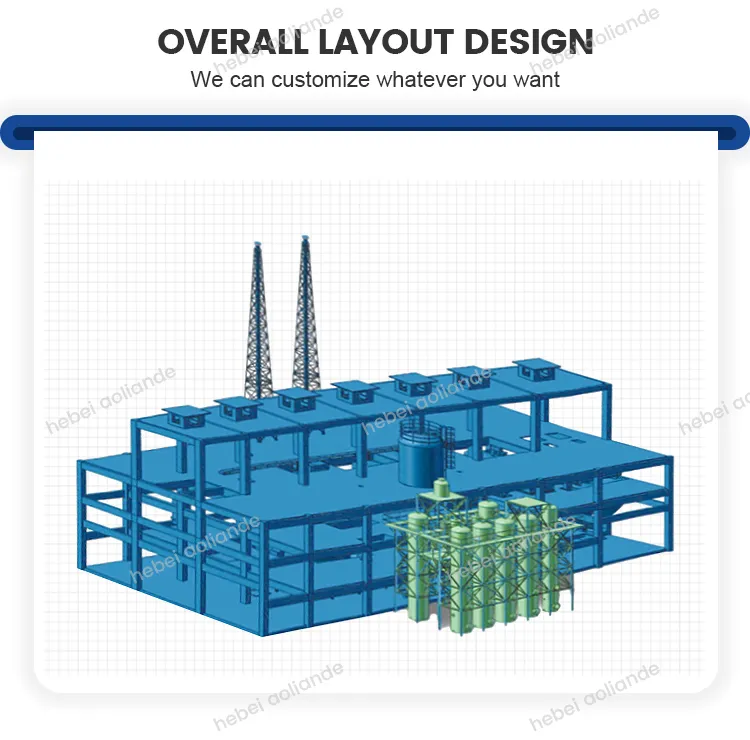
(potassium sulfate production)
FAQS on potassium sulfate production
Q: What are the primary methods for potassium sulfate production?
A: The main methods include the Mannheim process (reacting KCl and sulfuric acid) and the potassium-magnesium sulfate conversion. Other methods involve brine evaporation or reacting sodium sulfate with potassium chloride.
Q: How does sodium sulfate production relate to potassium sulfate manufacturing?
A: Sodium sulfate can be a byproduct in some potassium sulfate processes, such as the Hargreaves method. It may also serve as a raw material in alternative production routes when reacted with potassium salts.
Q: Can a sodium sulfate plant be adapted for potassium sulfate production?
A: Partial adaptation is possible if infrastructure supports sulfate-based reactions, but dedicated equipment for potassium chloride handling and purification would typically be required.
Q: What are key differences between potassium and sodium sulfate production processes?
A: Potassium sulfate often requires potassium chloride as a feedstock, while sodium sulfate uses salt or byproduct streams. Energy inputs and reaction temperatures also differ significantly between the two processes.
Q: Are byproducts from sodium sulfate plants used in other industries?
A: Yes, sodium sulfate byproducts may be used in detergents, glass manufacturing, or as feedstock for potassium sulfate production via metathesis reactions with potassium chloride.