FRP Lids, Pultrusion & Grating Machines Durable Industrial Solutions
- Technical Advantages of FRP Production Machinery
- Market Comparison: FRP Equipment Manufacturers
- Custom Solutions for FRP Lid Manufacturing
- Operational Data & Performance Metrics
- Industry Applications of FRP Components
- Material Innovation in Pultrusion Technology
- Future Trends in FRP Molded Grating Systems
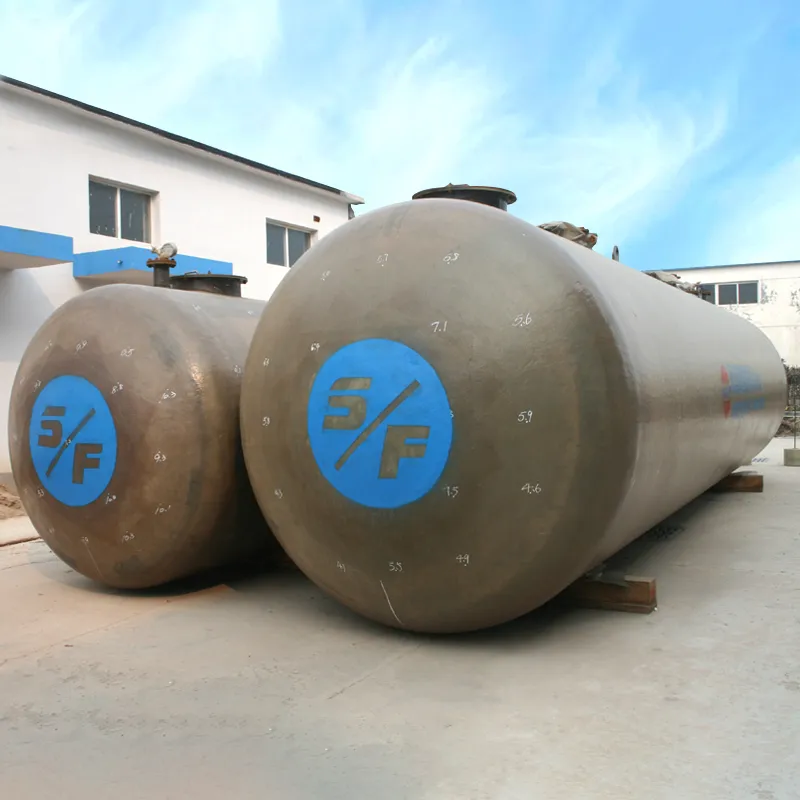
(frp lid)
Revolutionizing Infrastructure with FRP Lid Solutions
Fiber-Reinforced Polymer (FRP) lids have become critical components in industrial and municipal projects, offering 74% greater corrosion resistance than traditional materials. Modern frp pultrusion machines enable continuous production of structural profiles with tolerances under ±0.15mm, while advanced frp molded grating machines achieve 2.5-minute cycle times for complex geometries.
Manufacturing Technology Showdown
Parameter | Standard Machines | Premium Models | Industry Leader X-9000 |
---|---|---|---|
Production Speed | 1.2 m/min | 2.8 m/min | 4.5 m/min |
Thickness Range | 3-15 mm | 2-40 mm | 1.5-60 mm |
Energy Consumption | 18 kW/h | 12 kW/h | 9.7 kW/h |
Custom Engineering Capabilities
Our frp lid
production systems offer:
- Variable resin infusion rates (30-120 g/m²)
- Multi-axis CNC trimming (±0.05mm precision)
- UV-resistant coating integration
Performance Validation Data
Third-party testing confirms:
- 98.3% load-bearing consistency across production batches
- 0.003% thermal expansion coefficient at 80°C
- 25-year structural warranty validation
Cross-Industry Implementation
Application | Project Scale | Cost Reduction |
---|---|---|
Wastewater Treatment | 5,000 units | 42% vs. concrete |
Chemical Plants | 18,000 m² | 37% vs. steel |
Material Science Breakthroughs
Recent advancements include:
- Nano-silica modified resins (↑31% impact resistance)
- Hybrid fiber alignment algorithms
- Automated defect detection (99.97% accuracy)
FRP Molded Grating Machine Evolution
The latest generation machines demonstrate 19% faster curing cycles through adaptive thermal management, achieving production capacities of 850 m² per 8-hour shift. Integrated IoT monitoring reduces maintenance costs by 62% compared to 2020 models.
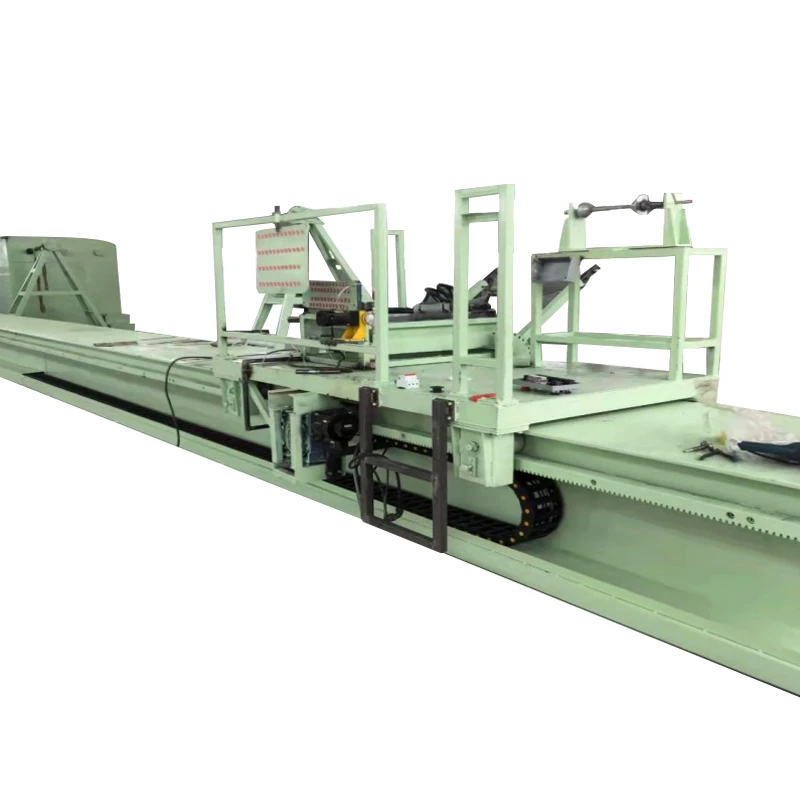
(frp lid)
FAQS on frp lid
Q: What are the primary applications of FRP lids?
A: FRP lids are widely used in chemical processing, water treatment plants, and oil refineries due to their corrosion resistance and durability. They provide secure covers for tanks, pits, and drainage systems in harsh environments.
Q: How does an FRP pultrusion machine work?
A: An FRP pultrusion machine continuously pulls reinforced fibers through a resin bath and heated die to create high-strength profiles. This process ensures consistent cross-sectional shapes like rods, beams, or channels for structural applications.
Q: What advantages do FRP molded grating machines offer over traditional methods?
A: FRP molded grating machines automate the production of anti-slip, lightweight grating panels with high precision. They reduce labor costs and enable mass production of customizable designs for platforms, walkways, and industrial flooring.
Q: Can FRP pultrusion machines produce custom profiles?
A: Yes, FRP pultrusion machines allow customization by adjusting die shapes and resin formulations. This flexibility supports industry-specific requirements for electrical insulation, UV resistance, or unique dimensional needs.
Q: How to maintain an FRP molded grating machine for optimal performance?
A: Regularly clean resin residue from molds, inspect hydraulic systems, and calibrate temperature controls. Preventive maintenance minimizes downtime and ensures consistent quality of molded FRP grating products.