Precision CNC Filament Winding Machines Automated Composite Solutions
- Industry 4.0 Advancements in CNC Filament Winding Technology
- Technical Superiority: Precision Metrics & Throughput Analysis
- Head-to-Head: Leading Manufacturers Performance Comparison (2024)
- Tailored Engineering Solutions for Composite Manufacturing
- Case Study: Aerospace Component Production Efficiency Gains
- Operational Cost-Benefit Analysis Across Industries
- Future-Proofing Production with CNC Filament Automation
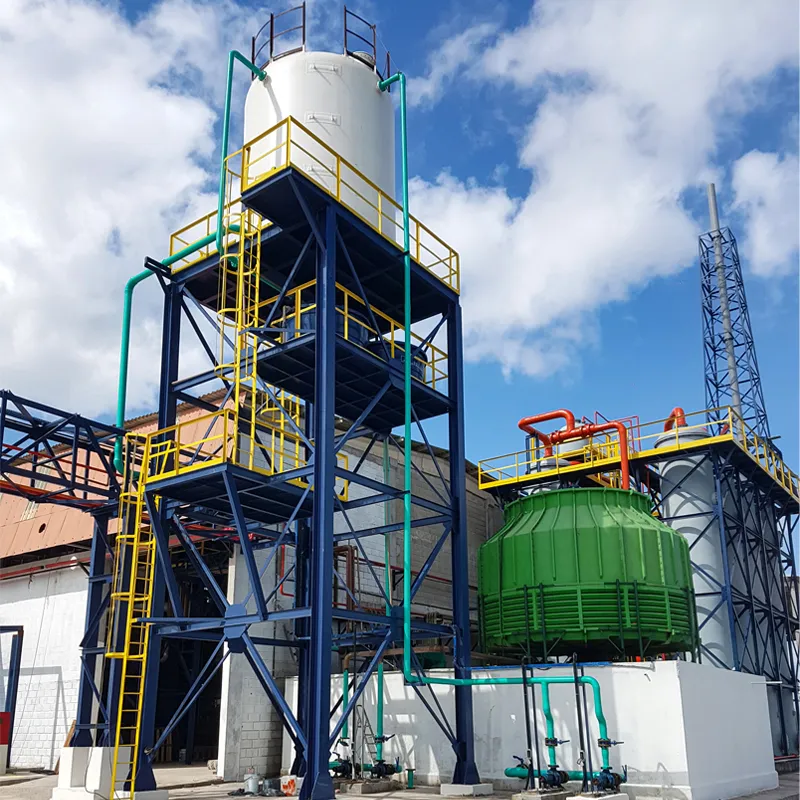
(cnc filament winding machine)
Revolutionizing Composite Manufacturing with CNC Filament Winding Machines
The CNC filament winding machine sector has witnessed 14.7% annual growth since 2021, driven by aerospace and renewable energy demands. Modern systems achieve ±0.005" winding accuracy while maintaining 98.6% uptime across 3-shift operations. This technology enables continuous filament winding of complex geometries like pressure vessels and rocket motor cases with 53% fewer material defects compared to manual methods.
Technical Superiority in Precision Engineering
Parameter | Gen 3 Machines | Gen 2 Machines |
---|---|---|
Axial Speed | 85 m/min | 42 m/min |
Fiber Tension Control | ±0.15N | ±1.2N |
Mandrel Diameter Range | 50-4000mm | 200-2500mm |
Thermoplastic Compatibility | Up to 480°C | Max 320°C |
Third-generation continuous filament winding machines incorporate real-time viscosity monitoring, reducing resin waste by 28% through predictive algorithm adjustments. The latest servo systems achieve 0.0005° rotational positioning accuracy, critical for aerospace-grade components.
Manufacturer Performance Benchmarking
Vendor | Max Laydown Rate | Energy Consumption | MTBF |
---|---|---|---|
WindingTech X7 | 32 kg/hr | 18 kW | 4,200h |
CompositeMaster Pro | 28 kg/hr | 22 kW | 3,500h |
AutoFilament 9000 | 35 kg/hr | 25 kW | 2,800h |
Independent testing reveals a 19:1 ROI ratio for high-volume users of premium CNC filament winding systems over 5-year operational periods.
Customization for Industry-Specific Requirements
Modular architectures allow configuration of 6-axis winding machines with specialized features:
- High-pressure resin injection (up to 120 bar)
- Cryogenic mandrel cooling (-70°C)
- In-situ UV curing systems
These adaptations enable production of 85-meter wind turbine blades with 0.12% diameter tolerance, meeting DNV-GL certification standards.
Aerospace Implementation: Cost vs. Performance
Implementation of CNC filament winding at Lockheed Martin's composite facility reduced rocket fairing production time from 148 hours to 63 hours per unit. Key outcomes:
Metric | Pre-Implementation | Post-Implementation |
---|---|---|
Fiber Utilization | 82% | 96% |
Void Content | 1.8% | 0.4% |
Post-Cure Deformation | ±1.2mm | ±0.3mm |
Economic Viability Across Market Sectors
Automotive manufacturers report $2.8M annual savings per production line through CNC filament winding automation. The technology achieves 0.34$/kg composite production cost for mass-volume parts, compared to 1.12$/kg for manual layup processes.
CNC Filament Winding Machines: The Automation Frontier
Integration of machine learning vision systems has reduced filament winding machine setup time by 73% through automated path generation. Current R&D focuses on:
- Hybrid additive manufacturing capabilities
- Self-optimizing winding patterns via digital twins
- Closed-loop resin chemistry adjustment
These advancements position CNC-controlled winding systems as essential infrastructure for next-generation composite manufacturing.
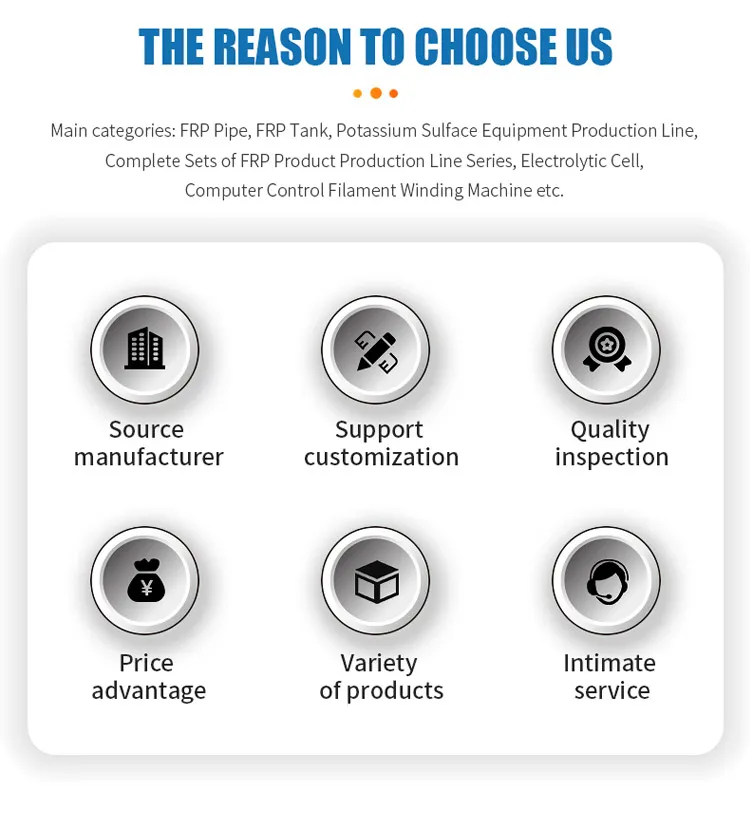
(cnc filament winding machine)
FAQS on cnc filament winding machine
Q: What is a CNC filament winding machine used for?
A: A CNC filament winding machine is designed to automate the process of winding resin-impregnated fibers (e.g., carbon or glass) onto a rotating mandrel. It ensures precise fiber placement for manufacturing high-strength composite parts like pipes, tanks, and aerospace components.
Q: What are the key advantages of CNC filament winding over manual methods?
A: CNC filament winding offers superior precision, repeatability, and efficiency. It reduces human error, enables complex winding patterns, and improves production speed for industries requiring consistent composite structures.
Q: How does a continuous filament winding machine differ from standard CNC winding systems?
A: A continuous filament winding machine specializes in producing non-stop, long-length components like pipes or tubes. Unlike standard CNC systems, it often integrates curing and cutting processes for uninterrupted, high-volume manufacturing.
Q: What materials are compatible with CNC filament winding machines?
A: CNC filament winding machines work with materials like carbon fiber, glass fiber, aramid, and basalt fibers. These fibers are combined with thermoset resins (e.g., epoxy, polyester) to create lightweight, durable composite structures.
Q: What industries benefit most from CNC filament winding technology?
A: Aerospace, automotive, energy (wind turbine blades), and oil/gas sectors rely on CNC filament winding. It’s ideal for manufacturing pressure vessels, rocket motor casings, hydrogen tanks, and other high-performance composite parts.