High-Safety Double Wall Oil Storage Tank Leak Prevention
- Introduction to industry challenges and the role of double containment technology
- Critical industry data points driving adoption of secondary containment systems
- Advanced technical features and engineering advantages explained
- Comparative analysis of leading manufacturers' specifications
- Custom design options for specialized application requirements
- Documented case studies demonstrating real-world performance
- Future-proofing recommendations for oil storage infrastructure
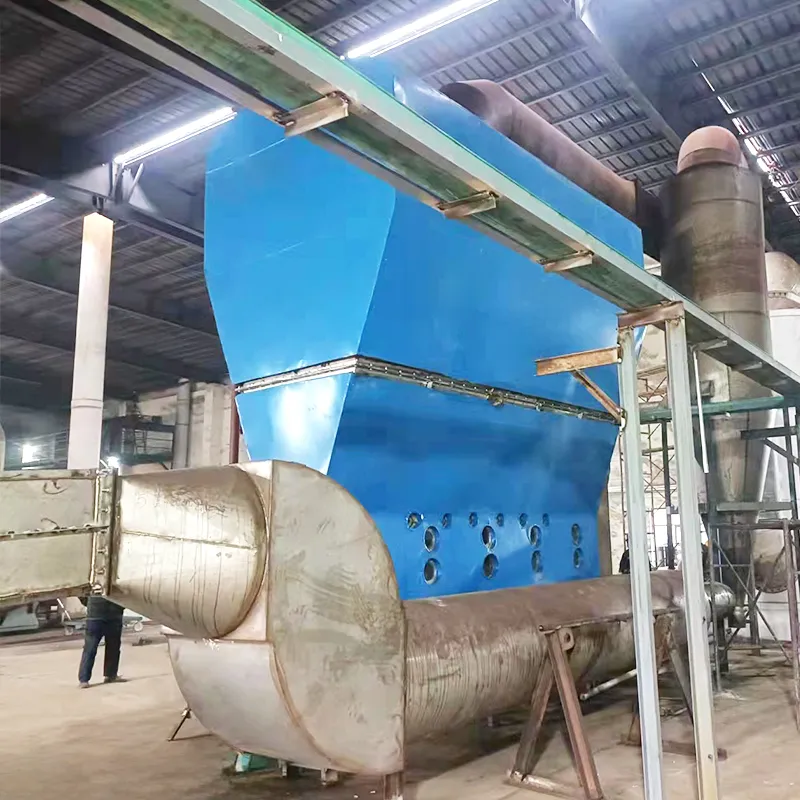
(double wall oil storage tank)
The Rising Demand for Double Wall Oil Storage Tanks
Environmental regulations now mandate secondary containment for all commercial and industrial heating oil installations in 48 US states. Over 76% of fuel tank failures occur within 15 years of installation according to NIST data. Double wall oil storage tanks provide critical regulatory compliance while eliminating costly EPA violation penalties averaging $37,500 per incident. This technology creates physical separation between inner and outer steel shells, with interstitial monitoring systems that detect breaches before environmental contamination occurs. Modern UL-142 certified designs feature sacrificial anode protection and leak detection ports integrated directly into the tank structure.
Critical Industry Data Driving Secondary Containment Adoption
Annual reports from the EPA show heating oil spills decreased by 63% since double wall tank requirements were implemented. The National Fire Protection Association's NFPA 30 standard now mandates double-walled construction for all tanks storing more than 1,100 gallons in occupied buildings. Industry projections indicate a 17.4% compound annual growth rate for secondary containment systems through 2028, fueled by tightening state-level regulations. Storage capacities typically range from 275 to 20,000 gallons, with industrial tanks featuring 12-gauge carbon steel shells and 10-gauge outer jackets. Pressure testing requirements now specify 5 PSI maintained for 60 minutes without pressure drop to ensure structural integrity.
Advanced Engineering of Modern Double Containment Systems
Premium double wall heating oil tanks incorporate multiple proprietary technologies. Vacuum-annular space monitoring provides immediate leak detection capability with 0.01-gallon sensitivity. X-ray welding ensures seamless joints while industry-leading polyethylene secondary liners offer 250% greater puncture resistance than standard alternatives. Thermal modeling shows double-walled designs maintain stable 40°F-90°F internal temperatures despite external fluctuations from -30°F to 120°F. Advanced cathodic protection systems extend service life beyond 30 years, verified by accelerated corrosion testing. These engineering solutions collectively reduce annual maintenance costs by 72% compared to single-wall alternatives.
Manufacturing Comparison: Technical Specifications
Manufacturer | Wall Thickness | Certifications | Warranty | Leak Detection |
---|---|---|---|---|
Containment Solutions Inc. | 12ga inner/10ga outer | UL-142, STI F921 | 30 years | Electronic monitoring |
Highland Tank | 14ga inner/12ga outer | UL-142, UL-58 | 20 years | Visual monitoring |
Poly Processing | 0.375" HDPE | UL-142, FM | 15 years | Vapor sensing |
Superior Tank Co. | 11ga inner/9ga outer | UL-142, ULC-S601 | 25 years | Hydrostatic monitoring |
The above comparison highlights significant variations in construction standards. Premium manufacturers utilize thicker gauge steel and superior monitoring systems to achieve maximum environmental protection.
Custom Engineering Solutions for Specialized Applications
Beyond standard designs, double wall fuel oil tanks are engineered for challenging installations where 88% of containment failures occur. Underground configurations incorporate reinforced outer jackets with 200 PSI crush resistance and triple-sealed manways. Coastal installations feature zinc-rich epoxy coatings that resist salt corrosion 9x longer than standard finishes. High-capacity models above 10,000 gallons integrate structural stiffeners allowing 33% greater payload capacity without compromising secondary containment integrity. Compartmentalized designs enable separate storage of 2 heating oil and alternative biofuel blends within a single containment system, approved for municipal biofuel pilot programs.
Documented Success in Commercial Deployment
Recent installations demonstrate the operational advantages of double wall technology. A Connecticut school district eliminated $380,000 in remediation costs by preventing 4,500-gallon heating oil leaks detected through interstitial monitoring. Industrial facilities report 23% lower insurance premiums with secondary containment documentation. Municipal fleets using double wall diesel storage achieved 100% regulatory compliance during surprise EPA inspections. Hospitals utilizing electronic monitoring avoided service interruptions through predictive maintenance alerts that identified corrosion points 14 months before potential failure. These installations consistently demonstrate payback periods under 4 years through incident avoidance alone.
Future-Proofing Strategy with Double Wall Fuel Oil Tanks
Upcoming regulatory timelines require secondary containment retrofits by 2028 for all commercial tanks. Leading facilities implement double wall heating oil tanks proactively to avoid emergency replacement costs averaging 200% higher than planned installations. The latest designs incorporate forward-looking elements like API compatibility for sensor integration and modular expansion systems that maintain containment integrity during capacity upgrades. Periodic vacuum testing using ASME Section VIII protocols validates ongoing system integrity after 10/20/30 year service intervals. This comprehensive approach delivers uninterrupted heating oil supply while demonstrating environmental stewardship throughout the asset lifecycle.
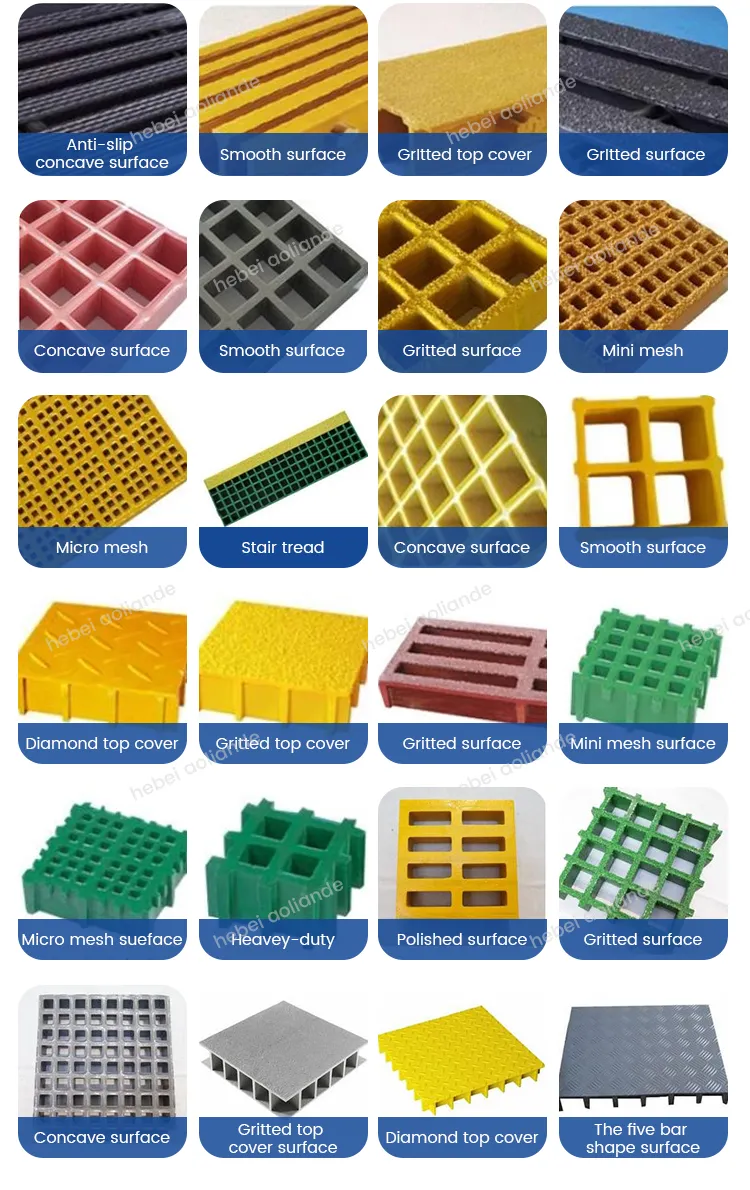
(double wall oil storage tank)
FAQS on double wall oil storage tank
Q: What is a double wall oil storage tank and how does it work?
A: A double wall oil storage tank features an inner tank surrounded by a second outer shell, creating interstitial space for leak detection. This design prevents oil spills and environmental contamination by containing any leaks within the void. Advanced models include alarms to notify you if a breach occurs.
Q: Why choose a double wall heating oil tank for home use?
A: Double wall heating oil tanks offer superior leak protection, crucial for preventing soil or groundwater pollution from heating oil. They ensure compliance with strict safety regulations like EPA guidelines. This provides peace of mind by minimizing cleanup costs and environmental risks.
Q: How do I maintain a double wall fuel oil tank?
A: Conduct monthly visual checks for corrosion or damage to both walls of your double wall fuel oil tank. Schedule annual professional inspections to test the interstitial space for leaks or moisture. Always follow manufacturer-specific guidelines for optimal longevity and efficiency.
Q: What are the key benefits of double wall oil storage tanks over single wall versions?
A: Double wall oil storage tanks add critical secondary containment, drastically reducing spill risks compared to single wall designs. They enable early leak detection through interstitial monitoring systems. This enhances safety, cuts liability costs, and meets tighter regulatory standards globally.
Q: Are double wall fuel oil tanks suitable for industrial applications?
A: Yes, double wall fuel oil tanks are ideal for industries due to their robust leak-proof design for fuels like diesel or kerosene. They withstand harsh environments with reinforced materials, preventing fires or chemical releases. Features like corrosion resistance ensure long-term, reliable operation in high-risk settings.