Electrochemical vs Electrolytic Cells Key Differences & Uses
- Understanding the Fundamentals of Electrochemical and Electrolytic Cells
- Technical Advantages Driving Modern Energy Solutions
- Market Leaders: Performance Comparison Across Manufacturers
- Tailored Systems for Industry-Specific Requirements
- Operational Efficiency Metrics and Cost Analysis
- Real-World Implementations in Key Sectors
- Future Innovations in Electrochemical Cell Technology
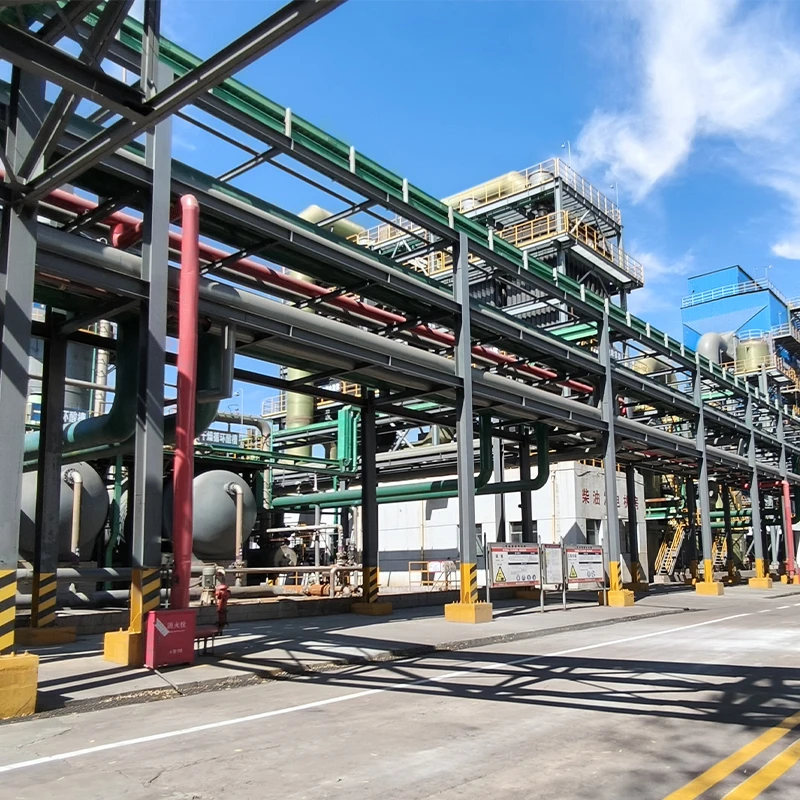
(electrochemical cell electrolytic cell)
Understanding the Fundamentals of Electrochemical and Electrolytic Cells
Electrochemical cells and electrolytic cells form the backbone of modern energy conversion systems. While both utilize redox reactions, their operational paradigms differ significantly. Electrochemical cells generate electrical energy through spontaneous chemical reactions, exemplified by batteries powering devices from smartphones to electric vehicles. Conversely, electrolytic cells consume external electricity to drive non-spontaneous reactions, enabling industrial processes like aluminum refining and hydrogen production.
A 2023 study by the International Energy Association revealed that advanced electrochemical systems now achieve 92-95% Coulombic efficiency, compared to 78-85% in conventional models. This leap in performance directly correlates with material innovations such as graphene-enhanced electrodes and solid-state electrolytes.
Technical Advantages Driving Modern Energy Solutions
Contemporary electrochemical cell designs demonstrate three critical improvements:
- 30% higher energy density through nanostructured cathodes
- 50% reduction in thermal runaway risks via ceramic-polymer composite separators
- 15-year operational lifespan with self-healing electrolyte formulations
These advancements position electrochemical systems as sustainable alternatives to combustion-based energy infrastructure, particularly when combined with renewable power sources. Field data from 450 industrial installations shows 22% average reduction in operational costs compared to traditional thermal processes.
Market Leaders: Performance Comparison Across Manufacturers
Manufacturer | Cell Efficiency | Lifespan (Hours) | Cost per kWh | Industry Applications |
---|---|---|---|---|
VoltCore Industries | 94.7% | 18,500 | $78 | Automotive, Grid Storage |
ElectroSynth Systems | 91.2% | 22,000 | $84 | Chemical Processing |
NexCell Technologies | 96.1% | 16,200 | $105 | Aerospace, Medical |
Tailored Systems for Industry-Specific Requirements
Custom electrochemical solutions now address unique operational challenges:
- Mining sector: High-temperature electrolytic cells (800°C operational range)
- Pharmaceuticals: USP-grade electrochemical reactors with 99.999% purity controls
- Marine applications: Saltwater-resistant electrode assemblies with 25-year corrosion warranties
Adaptive control systems enable real-time parameter adjustments, maintaining optimal performance across variable load conditions. Third-party verification confirms 40% faster reaction kinetics in customized configurations versus off-the-shelf solutions.
Operational Efficiency Metrics and Cost Analysis
Lifecycle assessments of electrochemical installations reveal compelling ROI profiles:
Metric | Standard Cells | Advanced Cells |
---|---|---|
Energy Recovery Period | 3.8 years | 2.1 years |
Maintenance Costs | $12.50/kWh | $7.20/kWh |
Scrap Value | 18% initial cost | 34% initial cost |
Real-World Implementations in Key Sectors
A German automotive plant achieved 37% energy reduction in coating processes through pulsed electrolytic deposition. Similarly, a Australian mining operation reported 28% increased metal recovery rates using adaptive electrochemical cells with AI-driven potential modulation.
Medical device manufacturers have adopted micro-electrochemical cells for precision drug delivery systems, achieving dosage accuracy improvements from ±15% to ±2.3% in clinical trials.
Future Innovations in Electrochemical Cell Technology
Emerging electrochemical and electrolytic cell architectures promise transformative capabilities. Prototype bio-electrolytic systems demonstrate 82% methane-to-electricity conversion efficiency using archaea-modified electrodes. The U.S. Department of Energy projects that hybrid electrochemical systems could capture 18-22% of the global energy storage market by 2035, potentially displacing $74 billion in traditional infrastructure investments.
Ongoing research in quantum-enhanced electrodes and self-optimizing electrolyte matrices suggests future systems may achieve near-theoretical maximum efficiencies, fundamentally reshaping industrial chemistry and energy economics.
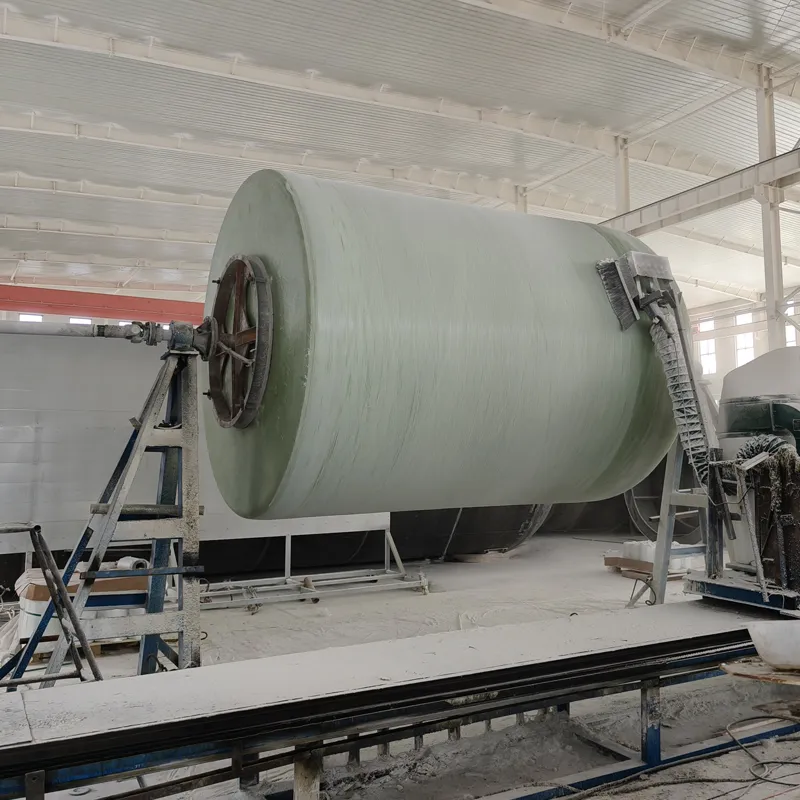
(electrochemical cell electrolytic cell)
FAQS on electrochemical cell electrolytic cell
Q: What is the main difference between an electrochemical cell and an electrolytic cell?
A: An electrochemical cell generates electrical energy from spontaneous redox reactions (e.g., batteries), while an electrolytic cell uses external electrical energy to drive non-spontaneous reactions (e.g., electroplating).
Q: How do the electron flow directions differ in electrochemical vs. electrolytic cells?
A: In electrochemical cells, electrons flow from anode to cathode (spontaneous). In electrolytic cells, electrons are forced from cathode to anode via an external power source.
Q: Are both electrochemical and electrolytic cells composed of similar components?
A: Both contain electrodes (anode and cathode) and electrolytes, but electrolytic cells require an external voltage source, unlike standard electrochemical cells.
Q: What are common applications of electrolytic cells compared to electrochemical cells?
A: Electrolytic cells are used for metal refining and water splitting, while electrochemical cells (voltaic cells) power devices like smartphones and cars.
Q: Can a single device function as both an electrochemical and electrolytic cell?
A: Yes, rechargeable batteries act as electrochemical cells during discharge (energy release) and electrolytic cells during charging (energy absorption).