Electrolytic Cell and Electrolysis Explained Efficient Electrochemical Solutions for Industry
- Introduction to Electrolytic Cell and Electrolysis
- Technical Advantages of Modern Electrolytic Cells
- Electrolytic Cell vs. Galvanic Cell: Fundamental Differences
- Electrochemical Cell and Electrolytic Cell in Industrial Applications
- Leading Electrolytic Cell Manufacturers: A Comparative Analysis
- Custom Electrolytic Solutions: Tailored for Your Needs
- Electrolytic Cell and Electrolysis: Real-World Success Stories
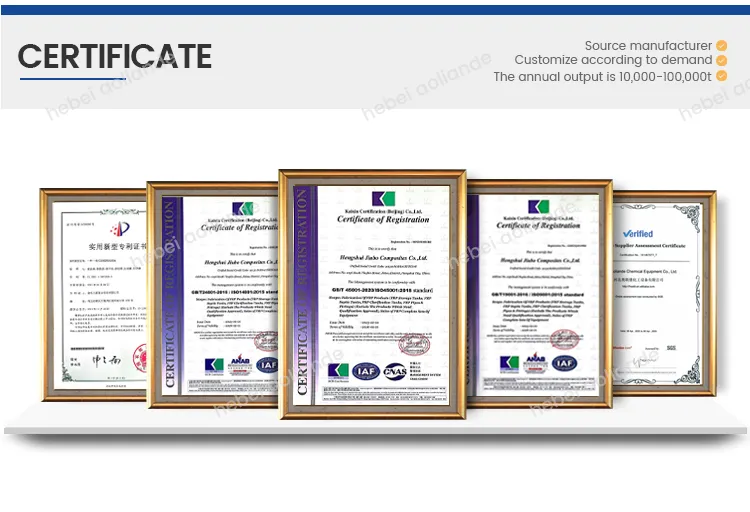
(electrolytic cell and electrolysis)
Introduction to Electrolytic Cell and Electrolysis
Electrolytic cell and electrolysis are foundational technologies in the field of industrial chemistry and materials science. Electrolysis is a non-spontaneous chemical process driven by electrical energy, usually conducted in specialized devices known as electrolytic cells. The global demand for chemical compounds produced through electrolytic methods—such as aluminum, chlorine, and hydrogen—has soared, with the market for hydrogen produced using electrolysis projected to reach USD 16.6 billion by 2031. Electrolytic cells play a crucial role in processes involving the breakdown of ionic substances and the deposition or purification of metals. Advances in cell design, electrode materials, and electrolytes have propelled the efficiency and scalability of electrolysis, allowing industries to achieve higher purity, lower costs, and improved sustainability. In the following sections, we delve into the technical breakthroughs, industry comparisons, and real-world impact of electrolytic technologies.
Technical Advantages of Modern Electrolytic Cells
Modern electrolytic cells incorporate a variety of technical advancements that differentiate them from their older counterparts. Innovations such as advanced membrane separation technologies, high-surface-area electrodes, and automated electronic controls have substantially improved operational efficiency. Where traditional cells often achieved current efficiencies below 80%, current state-of-the-art systems regularly exceed 95%, minimizing energy waste and operational costs. New catalysts, including platinum-group metals and conductive ceramics, increase the rate of electrolysis and markedly reduce overpotentials. For example, the adoption of ion-exchange membranes in chlor-alkali electrolysis has reduced environmental impact and eliminated chlorine gas leakage hazards. More precisely controlled voltage and temperature regimes, made possible by IoT-based automation, have allowed for precise modulation of electrochemical reactions. As energy costs have a significant bearing on production budgets—energy requirements for water electrolysis range from 4.5 to 5.5 kWh per cubic meter of hydrogen—these improvements not only increase output but also enable a rapid response to fluctuating energy prices and supply.
Electrolytic Cell vs. Galvanic Cell: Fundamental Differences
Despite both being types of electrochemical cells, the distinction between electrolytic cell and galvanic cell is essential for understanding their industrial and laboratory applications. Galvanic cells—exemplified by batteries—generate electrical energy through spontaneous redox reactions, whereas electrolytic cells consume electrical energy to drive chemical changes that would not otherwise occur. This difference in energy directionality underpins their roles in energy storage and material synthesis. Galvanic cells typically function with positive cell potentials and produce energy; electrolytic cells require an external power source and operate with negative cell potentials. The following table summarizes the core differences and typical uses:
Parameter | Electrolytic Cell | Galvanic Cell |
---|---|---|
Process Direction | Non-spontaneous (requires energy input) | Spontaneous (generates energy) |
Main Purpose | Chemical synthesis, metal refining | Energy storage, power supply (batteries) |
Cell Potential | Negative | Positive |
Electrode Behavior | Anode (+) oxidation, Cathode (–) reduction | Anode (–) oxidation, Cathode (+) reduction |
Example | Water electrolysis cell | Lithium-ion battery |
Electrochemical Cell and Electrolytic Cell in Industrial Applications
Present-day industrial landscapes rely heavily on both electrochemical cell and electrolytic cell technologies. In aluminum smelting, the Hall-Héroult electrolytic process dominates, requiring high-current, low-voltage cells that operate continuously to produce over 60 million metric tons of aluminum annually worldwide. Chlor-alkali electrolysis powers the production of 74 million tons of chlorine each year, utilizing membrane or diaphragm cells to separate and purify the end products. Hydrogen production through water electrolysis is becoming increasingly central to renewable energy strategies—especially with proton exchange membrane (PEM) electrolyzers allowing rapid ramp-up for grid-balancing and green hydrogen initiatives. These cells are engineered for minimal maintenance, long electrode life (over 20,000 operating hours), and safety through integrated monitoring systems. As industries push to decarbonize and electrify, demand for high-throughput and energy-efficient electrolytic cells continues to accelerate.
Leading Electrolytic Cell Manufacturers: A Comparative Analysis
The electrolytic cell and electrolysis
market features several key manufacturers whose products differ in efficiency, scale, and customization options. The table below provides a comparison of leading providers based on technical features, production capacity, and global reach:
Manufacturer | Current Efficiency (%) | Max Production Capacity | Electrode Material | Customization Options | Primary Markets |
---|---|---|---|---|---|
NEL Hydrogen | 96 | 3,000 Nm³/h (H₂) | Nickel, Platinum | High | Europe, North America, Asia-Pacific |
Thyssenkrupp Uhde Chlorine Engineers | 95 | 800,000 t/a (Chlorine) | Titanium, Ruthenium Oxide | Medium | Global |
Cummins Inc. | 94 | 2,000 Nm³/h (H₂) | Nickel, Iridium | Medium | Americas, Europe |
McPhy Energy | 93 | 1,600 Nm³/h (H₂) | Stainless Steel, Nickel | High | Europe, Asia |
These companies invest heavily in R&D to enhance both electrolytic cell durability and process automation. Clients choose suppliers based on lifetime cost efficiency, after-sales service, and the ability to tailor systems to unique process requirements.
Custom Electrolytic Solutions: Tailored for Your Needs
With the diversity of electrochemical applications, standard products rarely meet every industry-specific requirement. Custom electrolytic cell solutions are increasingly in demand for sectors such as pharmaceuticals, semiconductor manufacturing, and renewable energy. These tailored systems support various electrolytes, operate at specific voltages, and integrate with industrial digital controls (SCADA/PLC). For instance, in specialty electroplating, custom-shaped electrodes and variable-current regimes improve coating uniformity and reduce material wastage by 18% compared to off-the-shelf solutions. Modular cell designs allow seamless expansion as production needs evolve, supporting throughputs from small-batch laboratory scale up to multi-ton processing facilities. Partnering with manufacturers offering flexible engineering and fast prototyping capabilities ensures that customers receive solutions optimized for efficiency, regulatory compliance, and long-term operational reliability.
Electrolytic Cell and Electrolysis: Real-World Success Stories
Electrolytic cell and electrolysis technologies have catalyzed progress across multiple industries. In the energy sector, PEM electrolyzers deployed in Germany's “Hydrogen Valley” initiative enable production of 10,000 metric tons of green hydrogen annually, directly powering public transportation and decarbonizing industry. In the mining sector, a leading copper refinery in Chile deployed advanced electrolytic cells, boosting copper cathode purity to 99.998% and slashing energy costs by 12% over ten years. In the field of water treatment, municipal authorities in Singapore utilize customized electrochemical cells for on-site chlorine generation, reducing chemical transport emissions by over 8,000 metric tons of CO₂ annually. These case studies underscore the impact of innovative electrolytic cell and electrolysis technology on quality, efficiency, and sustainability. As global demand for clean energy, advanced materials, and sustainable manufacturing accelerates, electrolytic cell expertise will remain at the forefront of industrial progress.
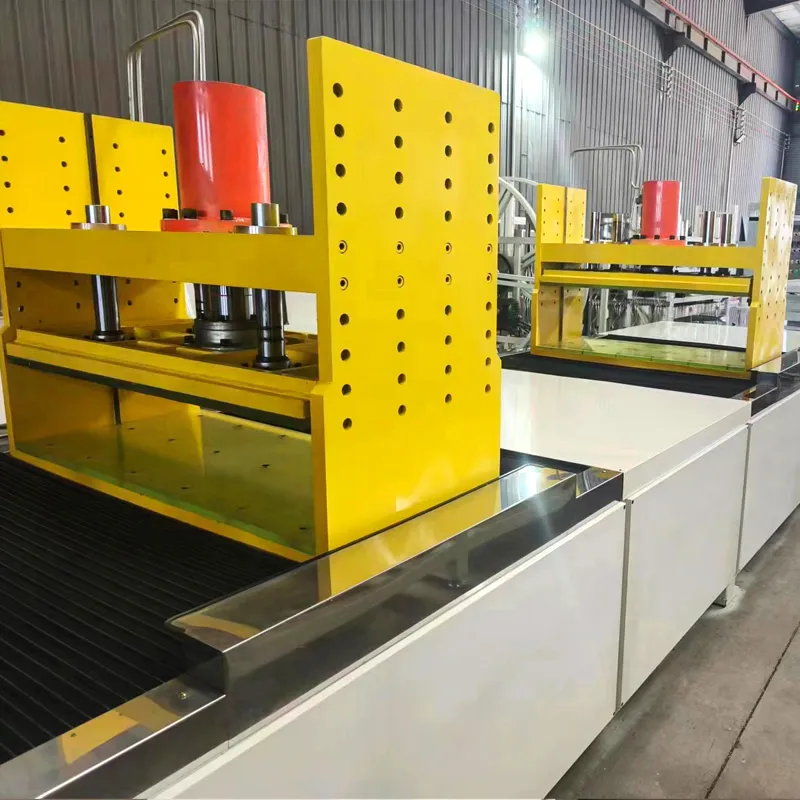
(electrolytic cell and electrolysis)