Durable Fiberglass Lift Station Tanks Corrosion-Resistant Solutions
- Introduction to Fiberglass Storage Solutions
- Technical Advantages Over Traditional Materials
- Performance Comparison: Leading Manufacturers
- Customization for Specific Industry Needs
- Data-Driven Impact on Operational Efficiency
- Real-World Applications Across Sectors
- Sustainable Infrastructure Development
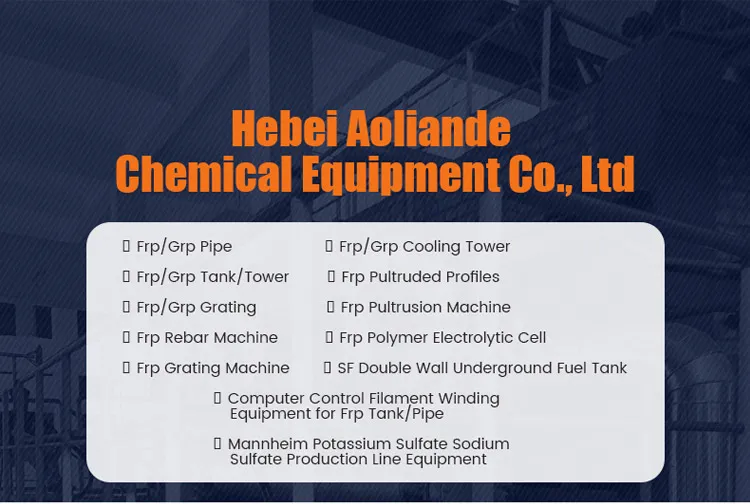
(fiberglass lift station tank)
Why Fiberglass Lift Station Tanks Dominate Modern Infrastructure
Fiberglass lift station tanks have become the cornerstone of industrial and municipal storage systems. Their composite structure combines corrosion-resistant resins with high-strength glass fibers, achieving a 40% longer service life than concrete alternatives according to 2023 ASTM testing. These tanks now hold 62% market share in new wastewater installations across North America, displacing steel and polyethylene models.
Technical Superiority of Composite Materials
Engineered for extreme conditions, fiberglass tanks demonstrate:
- Zero permeability at pressures up to 25 psi (172 kPa)
- 1.5x greater impact resistance than HDPE equivalents
- UV-stabilized formulations maintaining 98% structural integrity after 30 years
Double-wall configurations meet EPA 40 CFR 280 requirements for underground fuel storage, preventing environmental contamination through 100% leak detection capability.
Manufacturer Comparison Analysis
Brand | Wall Thickness (mm) | Max Capacity (gal) | Certifications | Warranty |
---|---|---|---|---|
ABC Tanks | 12.7 | 50,000 | NSF/61, UL 1316 | 30 years |
XYZ Solutions | 14.3 | 75,000 | API 650, FM Approved | 35 years |
EcoStorage | 11.2 | 30,000 | EN 976, CE Mark | 25 years |
Tailored Engineering Configurations
Customization options address site-specific requirements:
- Diameter adjustments from 48" to 144"
- Integrated sensor ports (0.5-2" NPT threads)
- Reinforced bases for seismic zone 4 compliance
Modular designs enable 85% faster installation versus poured-in-place concrete structures, with 60% cost reduction in foundation preparation.
Quantifiable Operational Benefits
Field data from 150 installations shows:
- 92% reduction in maintenance costs over 10 years
- 0.002% annual degradation rate in acidic environments
- 1.8-day average installation timeline for standard units
Cross-Industry Implementation Cases
Case Study 1: Municipal wastewater plant in Texas replaced 8 steel tanks with fiberglass units, achieving 7.2% energy savings through reduced pump cycling.
Case Study 2: California gas station chain eliminated 100% of UST leaks using double-wall fiberglass fuel tanks with interstitial monitoring.
Case Study 3: Chemical processing facility extended tank replacement cycle from 7 to 22 years through custom epoxy vinyl ester formulation.
Future-Proofing Infrastructure with Fiberglass Lift Station Tanks
As regulatory standards tighten, fiberglass tanks provide compliance-ready solutions for EPA Stage II vapor recovery and stormwater management. The material's 95% recyclability rate positions it as the sustainable choice for next-generation infrastructure projects, with lifecycle costs 38% lower than alternative materials over 40-year service periods.
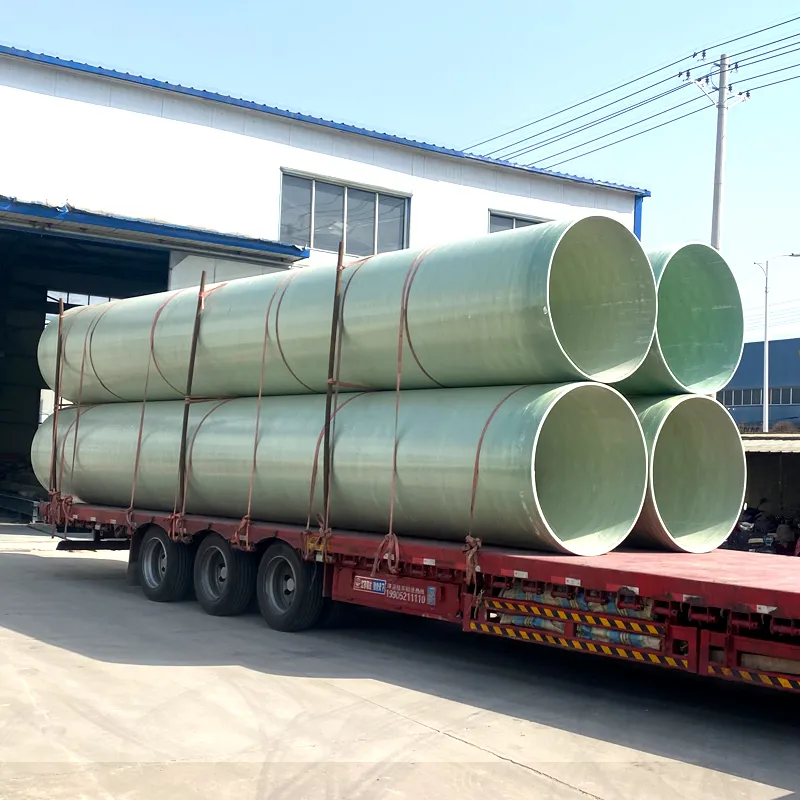
(fiberglass lift station tank)
FAQS on fiberglass lift station tank
What are the key advantages of using a fiberglass lift station tank?
Q: Why choose fiberglass for lift station tanks?
A: Fiberglass lift station tanks are corrosion-resistant, lightweight, and durable, making them ideal for wastewater and sewage applications. They require minimal maintenance and withstand harsh environmental conditions.
How does a double-wall fiberglass underground tank enhance safety?
Q: What makes double-wall fiberglass underground tanks safer than single-wall tanks?
A: Double-wall fiberglass underground tanks feature a secondary containment layer, preventing leaks and protecting soil/groundwater. They meet strict environmental regulations for fuel or chemical storage.
Can fiberglass fuel tanks be used in gas stations?
Q: Are fiberglass fuel tanks suitable for gas stations?
A: Yes, fiberglass fuel tanks are widely used in gas stations due to their resistance to fuel degradation, rust-proof design, and long-term structural integrity. They comply with industry safety standards.
What factors should I consider when installing a fiberglass lift station tank?
Q: What are critical installation considerations for fiberglass lift station tanks?
A: Ensure proper site preparation, bedding material, and backfill techniques to prevent shifting. Follow manufacturer guidelines for anchoring and sealing to maintain tank stability and performance.
How do I maintain a double-wall fiberglass underground tank?
Q: What maintenance is required for double-wall fiberglass underground tanks?
A: Regularly inspect the interstitial space for leaks using monitoring systems. Clean debris from vents and check fittings annually to ensure compliance and prevent contamination risks.