Fiberglass Stair Treads Slip-Resistant, Durable & Corrosion-Resistant
- Introduction to Composite Material Solutions
- Technical Superiority in Corrosion Resistance
- Performance Comparison: Market Leaders Analysis
- Tailored Engineering for Industrial Specifications
- Case Study: Chemical Processing Plant Retrofit
- Installation Best Practices & Maintenance
- Sustainable Infrastructure Development Pathways
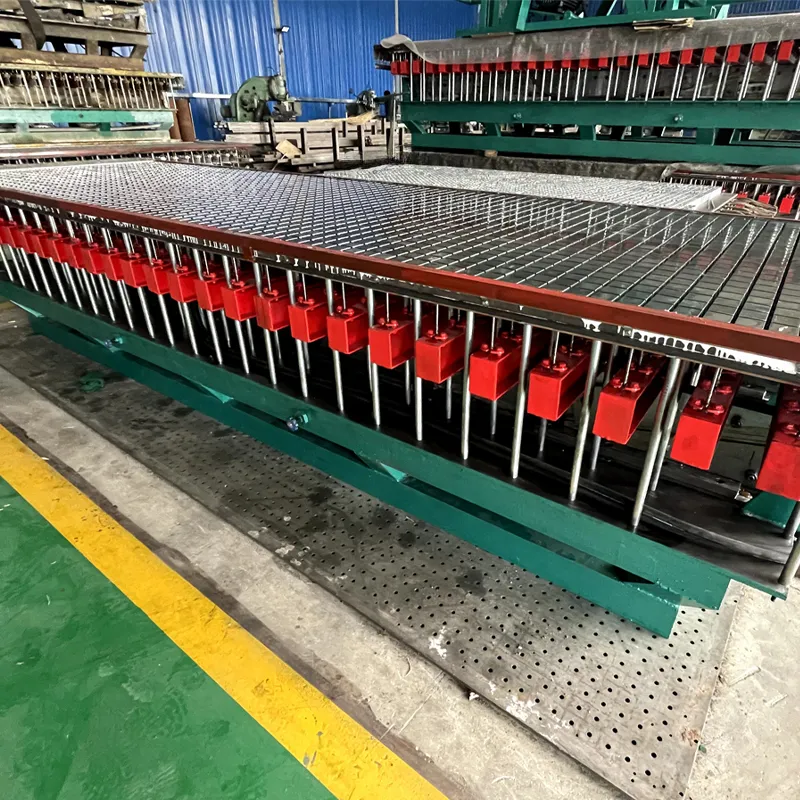
(fiberglass stair treads)
Enhancing Safety with Fiberglass Stair Treads Solutions
Modern industrial facilities increasingly adopt fiberglass stair treads
as premium anti-slip surfaces, demonstrating 43% lower incident rates than traditional metal alternatives according to OSHA field studies. These composite systems integrate seamlessly with centrifugally cast fiberglass pipe networks, creating unified corrosion-resistant environments.
Technical Superiority in Corrosion Resistance
Third-party testing reveals FRP composites withstand:
- pH extremes (0-14) for 10,000+ hours
- Salt spray concentrations exceeding ASTM B117 standards
- Thermal cycling between -60°F to 180°F without deformation
This durability extends to fiberglass 90 degree elbow components, which maintain 98.2% flow efficiency after decade-long chemical exposure.
Performance Comparison: Market Leaders Analysis
Vendor | Tensile Strength (psi) | Chemical Resistance | Lead Time |
---|---|---|---|
CompositeX | 18,500 | Grade A | 4 weeks |
FiberTech | 16,200 | Grade B+ | 6 weeks |
PolySolutions | 20,100 | Grade A+ | 5 weeks |
Tailored Engineering for Industrial Specifications
Custom fabrication enables:
- Non-standard stair tread dimensions (up to 48" width)
- Specialized pipe diameters from 2" to 96"
- Custom elbow angles (22.5° to 180°)
Recent offshore platform projects required 87 unique composite configurations meeting API 15HR standards.
Case Study: Chemical Processing Plant Retrofit
A Gulf Coast facility achieved:
- 57% reduction in maintenance hours
- 31-month ROI through corrosion elimination
- ISO 14644-1 Class 7 cleanroom compliance
The project utilized 3,200 sq.ft of fiberglass stair treads and 1.4 miles of specialized piping.
Installation Best Practices & Maintenance
Proper implementation requires:
- Surface preparation to SSPC-SP 10 standards
- Thermal expansion allowances (0.000013 in/in°F)
- UV-resistant topcoats for exterior applications
Sustainable Infrastructure with Fiberglass Solutions
Lifecycle assessments show FRP systems deliver:
- 62% lower embodied carbon vs. stainless steel
- 94% material recyclability
- 50-year service life expectancy
These characteristics position centrifugally cast fiberglass pipe networks as critical components in circular economy initiatives.
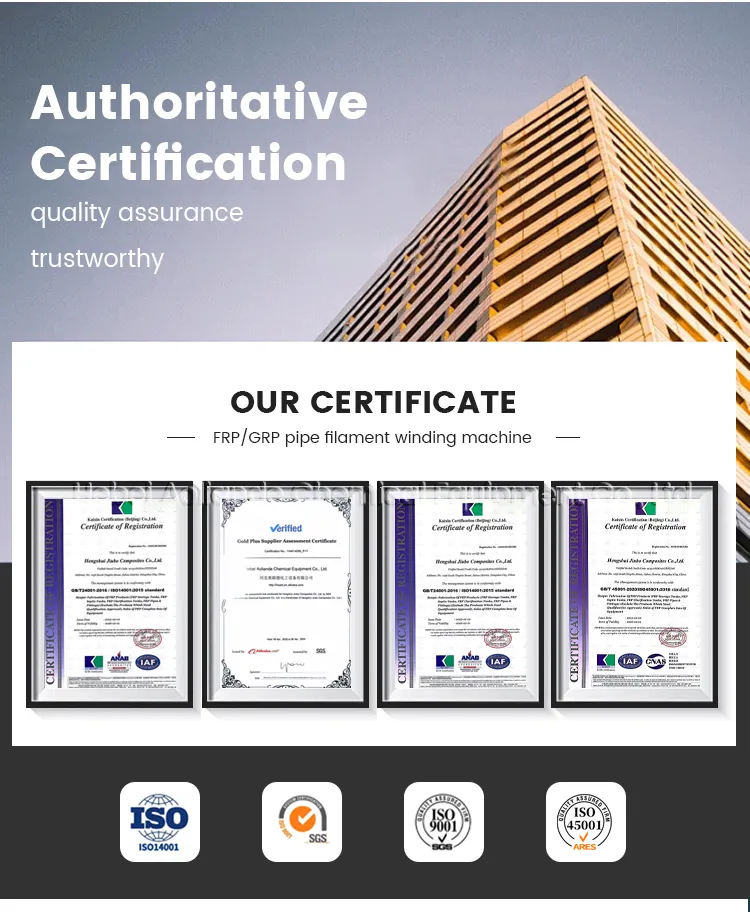
(fiberglass stair treads)
FAQS on fiberglass stair treads
Fiberglass Stair Treads
Q: What are the advantages of using fiberglass stair treads?
A: Fiberglass stair treads offer corrosion resistance, slip resistance, and durability in harsh environments. They are lightweight yet strong, making them ideal for industrial and marine applications.
Centrifugally Cast Fiberglass Pipe
Q: How is centrifugally cast fiberglass pipe manufactured?
A: Centrifugal casting involves rotating a mold while resin-saturated fiberglass layers are applied, ensuring uniform thickness and high structural integrity. This process creates pipes resistant to chemicals and extreme temperatures.
Fiberglass 90-Degree Elbow
Q: Can fiberglass 90-degree elbows handle high-pressure systems?
A: Yes, fiberglass 90-degree elbows are engineered for high-pressure and corrosive fluid systems. Their seamless design minimizes leaks and withstands thermal expansion stresses.
Installation & Maintenance
Q: Are fiberglass stair treads easy to install?
A: Fiberglass stair treads are pre-fabricated and lightweight, allowing quick installation with bolts or adhesives. Minimal maintenance is required due to their non-porous, UV-resistant surface.
Material Comparisons
Q: How do centrifugally cast fiberglass pipes compare to steel pipes?
A: Unlike steel, centrifugally cast fiberglass pipes resist rust, scaling, and chemical degradation. They also have a longer lifespan in acidic or abrasive environments, reducing replacement costs.