FRP Grating Machine Manufacturer High-Efficiency Molded Grating Production
- Overview of FRP Grating Machines in Modern Manufacturing
- Technical Advantages: Durability and Efficiency
- Performance Comparison: Leading Manufacturers Analyzed
- Custom Solutions for Industry-Specific Needs
- Real-World Applications and Case Studies
- Cost-Benefit Analysis and ROI Metrics
- Future Trends in FRP Grating Machine Innovation
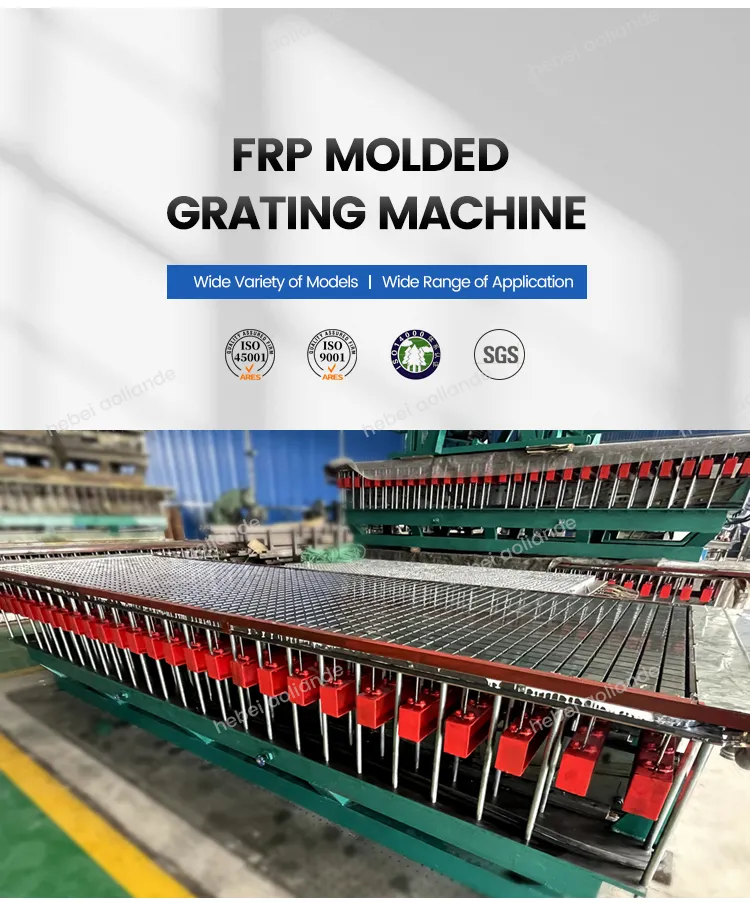
(frp grating machine)
Why FRP Grating Machines Are Transforming Industrial Production
FRP (Fiber Reinforced Plastic) grating machines have become indispensable in sectors demanding corrosion-resistant, lightweight, and high-strength materials. The global market for FRP molded grating machines is projected to grow at a CAGR of 8.3% through 2030, driven by infrastructure upgrades and stricter safety regulations. These machines enable the production of gratings that withstand harsh environments, including chemical plants, offshore platforms, and wastewater treatment facilities, with a service life exceeding 15 years.
Technical Advantages: Durability and Efficiency
Modern molded grating machines leverage advanced pultrusion and molding techniques to achieve superior mechanical properties. Key benefits include:
- 30% faster production cycles compared to traditional metal grating systems.
- Resistance to UV radiation, acids, and alkalis, reducing maintenance costs by up to 45%.
- Customizable mesh designs with load capacities ranging from 1,500 to 10,000 lbs/sq ft.
Performance Comparison: Leading Manufacturers Analyzed
Manufacturer | Production Speed (sq ft/hr) | Max Load Capacity (lbs/sq ft) | Energy Efficiency | Price Range ($) |
---|---|---|---|---|
TechGrate Systems | 220 | 8,500 | High | 85,000–120,000 |
FiberPult Inc. | 180 | 7,200 | Medium | 65,000–95,000 |
PolyMold Engineering | 250 | 10,000 | High | 110,000–150,000 |
Custom Solutions for Industry-Specific Needs
Leading suppliers offer tailored configurations for specialized applications. For example, anti-slip surface patterns are integrated for oil and gas platforms, while fire-retardant resins are used in aerospace facilities. Modular designs allow clients to adjust grating thickness (15–50 mm), panel sizes (up to 12 ft x 4 ft), and resin-to-glass ratios (1:1 to 3:1) based on operational requirements.
Real-World Applications and Case Studies
A chemical processing plant in Texas reported a 40% reduction in grating replacement costs after switching to FRP units produced by TechGrate Systems. Similarly, a desalination project in Dubai achieved 99% corrosion resistance over a decade using PolyMold’s machines. Additional applications include:
- Bridge decking in coastal regions
- Anti-static flooring for electronics manufacturing
- Safety walkways in nuclear power facilities
Cost-Benefit Analysis and ROI Metrics
While initial investments for FRP grating machines are 20–30% higher than steel alternatives, lifetime savings average 60% due to lower installation and upkeep expenses. For a mid-sized factory processing 5,000 sq ft/month, ROI is typically achieved within 2.3 years, with annual maintenance costs below $3,000.
Future Trends in FRP Grating Machine Innovation
Emerging technologies like AI-driven quality control and carbon-fiber hybrid composites are reshaping the FRP molded grating machine landscape. Manufacturers are also adopting IoT-enabled predictive maintenance systems, cutting downtime by up to 25%. As sustainability mandates tighten, machines capable of recycling 90% of production waste will dominate the next decade.
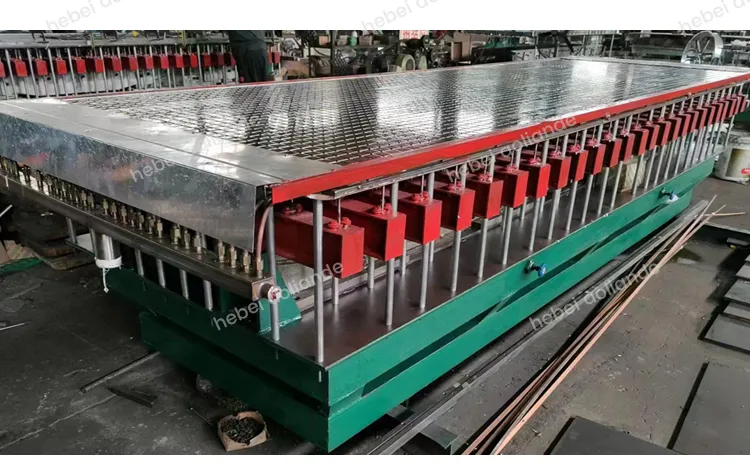
(frp grating machine)
FAQS on frp grating machine
Q: What is an FRP grating machine used for?
A: An FRP grating machine is designed to manufacture fiber-reinforced plastic (FRP) gratings, which are lightweight, corrosion-resistant panels used in industrial flooring, platforms, and walkways.
Q: How does an FRP molded grating machine differ from traditional metal grating machines?
A: Unlike metal grating machines, FRP molded grating machines use composite materials and molding techniques to produce gratings with superior resistance to rust, chemicals, and harsh environments.
Q: What are the key features of a molded grating machine?
A: Molded grating machines offer high precision, customizable mold designs, and automated processes to create uniform FRP gratings with consistent strength and dimensional accuracy.
Q: Can an FRP grating machine handle large-scale production?
A: Yes, modern FRP grating machines are built for high-volume production, enabling rapid manufacturing of gratings while maintaining quality and structural integrity.
Q: What industries benefit most from FRP molded grating machines?
A: Industries like oil and gas, wastewater treatment, marine, and chemical processing rely on FRP molded gratings for their durability, safety, and low maintenance requirements.