FRP Tanks & Vessels Manufacturer Custom, Durable Designs
- Material Innovation and Performance Metrics
- Engineering Advantages Over Traditional Materials
- Competitive Analysis of Leading Manufacturers
- Tailored Solutions for Industry-Specific Needs
- Case Studies: Industrial Deployments
- Operational Cost-Benefit Breakdown
- Sustainability and Future Applications
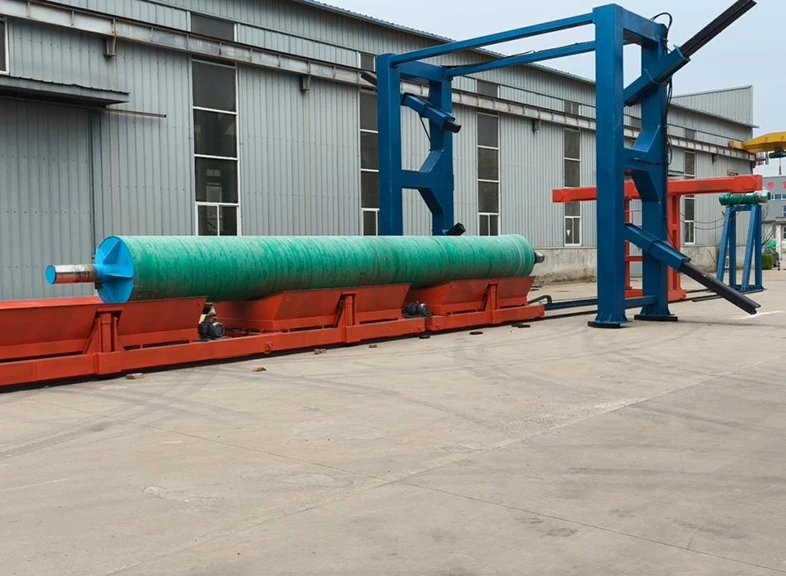
(frp tank and vessel)
FRP Tank and Vessel: Material Innovation and Performance Metrics
Fiber-reinforced plastic (FRP) tanks and vessels have redefined industrial storage solutions by combining corrosion resistance, lightweight durability, and structural adaptability. With a tensile strength of 1,200 MPa and a lifespan exceeding 30 years in aggressive chemical environments, these systems outperform traditional steel and concrete alternatives by 40% in lifecycle cost efficiency. The global FRP vessel market is projected to grow at 7.8% CAGR through 2030, driven by demand in water treatment and chemical processing sectors.
Engineering Advantages Over Traditional Materials
FRP construction eliminates electrolytic corrosion risks while maintaining a strength-to-weight ratio 8x greater than carbon steel. Key benefits include:
- Zero permeability: Prevents chemical leaching (ASTM D5421 compliance)
- Thermal stability: Operates from -60°C to 120°C without deformation
- Custom geometries: 3D filament winding allows ±1mm dimensional accuracy
Competitive Analysis of Leading Manufacturers
Manufacturer | Max Pressure (psi) | Diameter Range (ft) | Lead Time | Warranty |
---|---|---|---|---|
Vendor A | 150 | 4-20 | 8 weeks | 10 years |
Vendor B | 200 | 6-25 | 10 weeks | 15 years |
Vendor C | 175 | 3-18 | 6 weeks | 12 years |
Tailored Solutions for Industry-Specific Needs
Advanced manufacturers now offer application-engineered systems:
- Pharmaceutical grade: FDA-compliant resin systems with 0.1µm surface finish
- High-purity water: FRP sand filter vessels with 99.97% particulate retention
- Oil & gas: API 650-compliant tanks with explosion-resistant laminates
Case Studies: Industrial Deployments
A chemical plant in Texas achieved 22% operational cost reduction by replacing stainless steel reactors with custom FRP vessels. The installation handled 15% HCl at 80°C with zero maintenance over 5 years, validating accelerated depreciation schedules.
Operational Cost-Benefit Breakdown
Factor | FRP | Steel | Concrete |
---|---|---|---|
Installation Cost | $185/m³ | $240/m³ | $210/m³ |
Maintenance/Year | $12 | $85 | $65 |
Replacement Cycle | 30+ years | 12-15 years | 20 years |
FRP Tank and Vessel: Sustainability and Future Applications
With 92% recyclability and 60% lower embodied carbon than metallic alternatives, FRP technology aligns with circular economy mandates. Emerging applications include hydrogen storage vessels rated for 700-bar service and modular FRP sand filter vessels for decentralized water treatment networks. Industry leaders are now integrating IoT-enabled structural health monitoring directly into vessel walls, creating smart infrastructure assets with predictive maintenance capabilities.
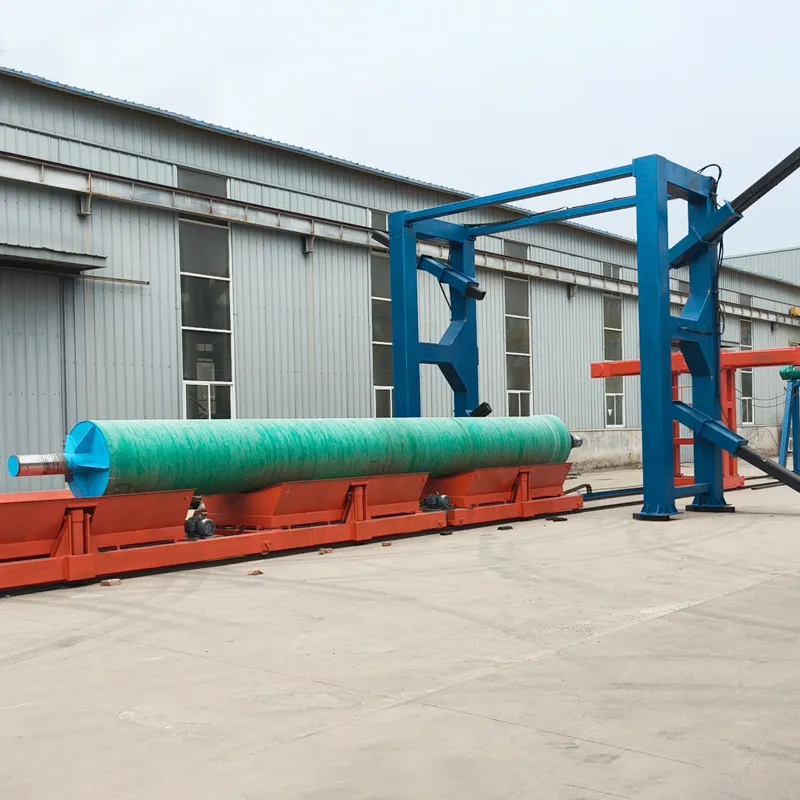
(frp tank and vessel)
FAQS on frp tank and vessel
Q: What are the key advantages of using FRP tanks and vessels compared to traditional materials?
A: FRP tanks and vessels offer superior corrosion resistance, lightweight construction, and longer lifespan than steel or concrete. They are also customizable and require minimal maintenance, reducing long-term costs.
Q: How does an FRP sand filter vessel improve water treatment processes?
A: FRP sand filter vessels provide high chemical resistance and durability for filtering impurities in water systems. Their seamless design prevents leaks, and their low weight simplifies installation and maintenance.
Q: What should I consider when choosing an FRP vessel manufacturer?
A: Prioritize manufacturers with certifications (e.g., ISO), proven expertise in FRP fabrication, and a portfolio of industry-specific projects. Ensure they offer compliance with standards like ASTM or ASME.
Q: Are FRP tanks suitable for harsh chemical environments?
A: Yes, FRP tanks excel in corrosive environments due to their non-reactive resin layers. They are widely used in chemical processing, wastewater treatment, and industrial storage where corrosion resistance is critical.
Q: Can FRP vessels be customized for specific industrial applications?
A: Absolutely. FRP vessel manufacturers can tailor designs for pressure ratings, temperature ranges, and chemical compatibility. Custom fittings, linings, and sizes ensure optimal performance for specialized needs.