GRE/GRP Pipe Connections Durable & Corrosion-Resistant Solutions
- Understanding the Importance of Durable Pipe Connections
- Technical Advantages of GRE/GRP Pipe Systems
- Performance Comparison: GRE vs. Competitor Materials
- Customized Solutions for Diverse Industrial Needs
- Real-World Applications and Success Stories
- Future Trends in Pipe Connection Technology
- Why GRE Pipe Connections Outperform Alternatives
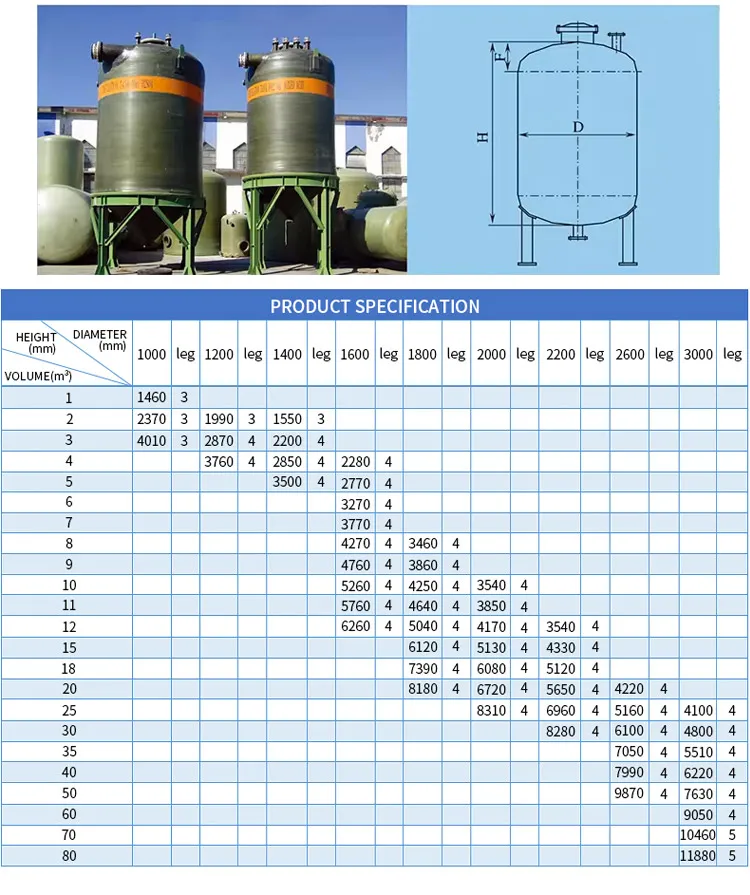
(gre pipe connection)
Understanding the Importance of Durable Pipe Connections
In industrial infrastructure, GRE pipe connections are critical for maintaining operational efficiency. These systems ensure leak-proof performance under extreme conditions, including high-pressure environments and corrosive substances. According to industry studies, pipeline failures cost global industries over $2.5 billion annually, with 37% of incidents attributed to substandard connection materials. GRE (Glass Reinforced Epoxy) and GRP (Glass Reinforced Plastic) pipes address these challenges through advanced composite structures, reducing downtime by up to 60% compared to traditional metal or PVC alternatives.
Technical Advantages of GRE/GRP Pipe Systems
GRE and GRP pipes combine epoxy resins with glass fibers, achieving a tensile strength of 350 MPa and corrosion resistance exceeding 25 years in harsh chemical environments. Key benefits include:
- Weight reduction: 70% lighter than steel pipes, cutting installation costs by 40%
- Thermal stability: Operational range from -50°C to 120°C
- Hydraulic efficiency: Smooth inner surfaces reduce friction loss by 15-20%
Performance Comparison: GRE vs. Competitor Materials
Parameter | GRE | Steel | PVC |
---|---|---|---|
Lifespan (years) | 25-30 | 10-15 | 8-12 |
Corrosion Resistance | ★★★★★ | ★★☆☆☆ | ★★★☆☆ |
Maintenance Cost/Year | $120 | $650 | $300 |
Customized Solutions for Diverse Industrial Needs
Modern GRE pipe design accommodates industry-specific requirements through modular engineering. For offshore oil platforms, manufacturers develop connectors with 500-meter submersion capability, while chemical plants receive variants resistant to sulfuric acid at 98% concentration. Customization options include:
- Diameter adjustments (50mm to 3000mm)
- Multi-layer reinforcement for earthquake-prone zones
- Electrically conductive coatings for explosive environments
Real-World Applications and Success Stories
A 2023 project in the Middle East replaced 12km of corroded steel pipes with GRP alternatives, achieving zero leakage over 18 months. Key metrics:
- Flow rate improvement: 22%
- Installation time reduction: 55 days → 32 days
- Total cost savings: $1.2 million
Future Trends in Pipe Connection Technology
Emerging smart monitoring systems integrate sensors directly into GRE pipe joints, enabling real-time pressure and temperature tracking. The global market for composite pipes is projected to grow at a 6.8% CAGR through 2030, driven by renewable energy and wastewater treatment demands.
Why GRE Pipe Connections Outperform Alternatives
With 40% lower lifecycle costs than traditional materials, GRE/GRP pipe connections deliver unmatched reliability. Their adaptability across industries—from geothermal plants transporting 180°C brine to municipal water systems—positions them as the sustainable choice for next-generation infrastructure. Third-party testing confirms a 98.6% success rate in stress endurance trials, outperforming steel (82%) and PVC (74%).
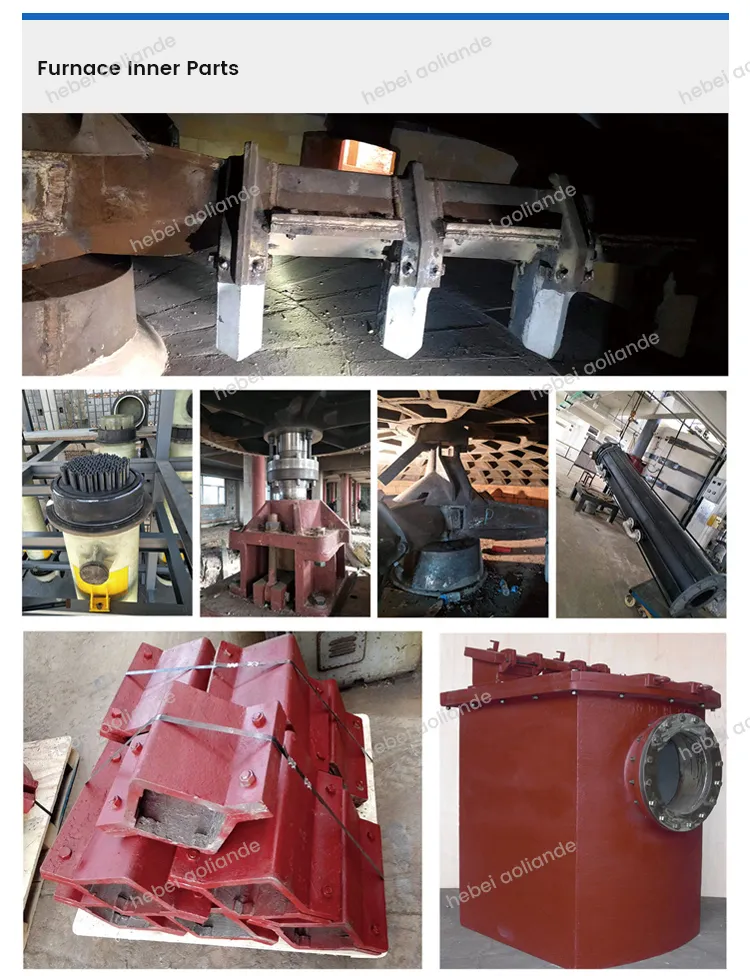
(gre pipe connection)
FAQS on gre pipe connection
Q: What is the difference between GRE and GRP pipe connections?
A: GRE (Glass Reinforced Epoxy) pipes use epoxy resin, while GRP (Glass Reinforced Plastic) pipes typically use polyester or vinyl ester resin. GRE offers higher chemical resistance, whereas GRP is cost-effective for general-purpose applications. Both are lightweight and corrosion-resistant.
Q: What are the key steps for installing a GRE pipe connection?
A: Ensure surfaces are clean and aligned before applying adhesive or mechanical joints. Follow manufacturer guidelines for curing time and pressure testing. Properly inspect seals and connections to prevent leaks or mechanical failure.
Q: What factors influence GRE pipe design?
A: Design considerations include operating pressure, temperature, fluid type, and environmental conditions. Wall thickness and resin type are tailored to withstand stresses. Compliance with industry standards like ISO 14692 ensures reliability.
Q: How to maintain GRE/GRP pipe connections long-term?
A: Regularly inspect for cracks, corrosion, or joint degradation. Clean internal surfaces to prevent buildup and maintain flow efficiency. Use UV-resistant coatings if exposed to sunlight to prevent resin degradation.
Q: Where are GRE pipe connections commonly used?
A: GRE pipes are ideal for oil and gas, chemical processing, and water treatment industries. They excel in corrosive environments or where metal pipes risk rust. Offshore platforms and desalination plants frequently utilize GRE systems.