Types of Electrolytic Cells Overview, Key Types & Applications
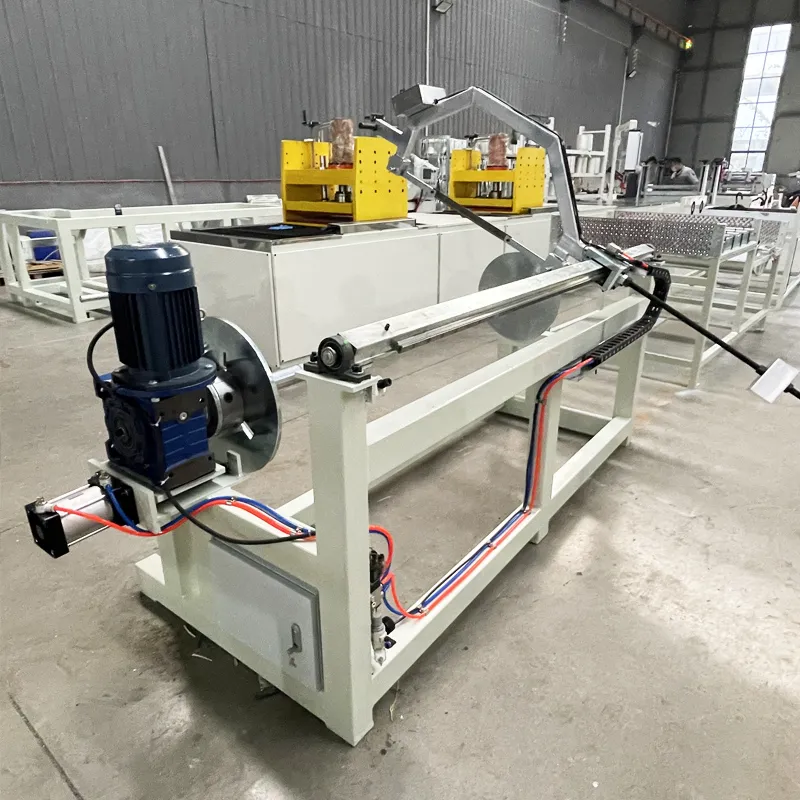
(types of electrolytic cells)
Understanding Types of Electrolytic Cells and Their Industrial Significance
This comprehensive analysis explores the diverse landscape of industrial electrolytic systems through these key aspects:
- Fundamental principles and operational mechanics of electrolytic cells
- Technical advantages and economic impact metrics across industries
- Comparative analysis of leading manufacturers and their technologies
- Custom engineering approaches for specialized applications
- Industry-specific implementation case studies with quantifiable results
- Emerging technological advancements in cell design
- Strategic selection criteria for different operational environments
Electrochemical Fundamentals and Operational Principles
Modern industrial processes leverage distinct categories of electrolytic cells based on their electrochemical architectures. Membrane cells utilize selective ion-exchange barriers to separate anode and cathode compartments, achieving 92-95% current efficiency in chlorine production. In contrast, diaphragm cells employ porous separators requiring periodic replacement every 12-18 months, while mercury cells have largely been phased out due to environmental regulations. Each configuration demonstrates specific electrolysis mechanisms:
- Aqueous Electrolyzers: Utilize liquid electrolyte solutions with ionic conduction, representing 68% of industrial installations
- Molten Salt Cells: Operate at 700-900°C for reactive metal extraction, consuming 12-18kWh per kilogram of aluminum produced
- Polymer Electrolyte Membrane (PEM): Solid polymer electrolytes enable rapid startups and dynamic operation, preferred for hydrogen generation
These systems fundamentally transform electrical energy into chemical energy through redox reactions, with efficiency determined by electrode overpotential, electrolyte conductivity, and thermodynamic limitations.
Technical Advantages and Operational Economics
Advanced electrolytic cell designs deliver substantial operational benefits. Modern membrane chlor-alkali cells achieve energy consumption as low as 2,150 kWh per ton of chlorine, representing a 40% reduction compared to legacy systems. Metallurgical applications using molten salt electrolysis maintain production costs below $1,800 per tonne for primary aluminum when energy prices remain under $0.04/kWh. Three critical performance vectors distinguish contemporary systems:
- Efficiency Metrics: Cutting-edge alkaline water electrolysers now reach 74-78% efficiency at current densities of 0.4 A/cm²
- Lifespan Considerations: PEM electrolyzer stacks demonstrate 65,000+ hours operational durability with proper maintenance protocols
- Footprint Optimization: Containerized electrolysis units deliver 500 Nm³/h hydrogen production in just 12m² footprint
The global electrolyzer market has experienced 12.4% compound annual growth since 2018, projected to reach $10.7 billion by 2027 as industries accelerate decarbonization initiatives.
Manufacturer Comparison and Technology Offerings
Manufacturer | Primary Technology | Max Capacity | Power Density | Efficiency (%) | Key Innovations |
---|---|---|---|---|---|
Thyssenkrupp Nucera | Alkaline Water Electrolysis | 700 MW Modular | 0.45 A/cm² | 78-82% | Scaffolded Electrodes |
Cummins (Hydrogenics) | PEM | 25 MW Single Unit | 3.0 A/cm² | 67-72% | HyStat® Thermal Integration |
Nel Hydrogen | Atmospheric Alkaline | 300 Nm³/h | 0.3 A/cm² | 70-75% | Zero-Gap Cell Geometry |
Bloom Energy | Solid Oxide Electrolysis | 100+ MW | - | 85-90% | High-T Steam Electrolysis |
Recent performance data indicates alkaline systems maintain cost advantages at scale ($900/kW), while PEM technologies demonstrate superior dynamic response characteristics essential for renewable power integration.
Customized Solutions for Industry-Specific Applications
Specialized configurations address unique process requirements across sectors. For precious metal recovery, pulsating current electrolysis achieves 99.97% purity through optimized waveform control. Chlor-alkali facilities now implement advanced membrane technologies reducing power consumption to 2,200 kWh per tonne while eliminating mercury contamination risks. Hybridized systems are increasingly prevalent:
- Metallurgical Processing: Multi-polar reduction cells for zinc electrowinning generate 99.995% pure metal at 3,100 kWh/tonne
- Water Treatment: Electrocoagulation units combine electrolytic oxidation with flocculation for >95% contaminant removal
- Chemical Synthesis: Gas diffusion electrode cells enable direct peroxide production, reducing energy intensity by 37% versus traditional routes
Such application-specific optimizations demonstrate tangible improvements: semiconductor facilities using custom electrolytic purification report 14-month ROI through reduced ultrapure water costs.
Industrial Implementation Case Studies
Quantifiable outcomes validate electrolytic cell selection criteria across sectors. A European chemical plant retrofitted membrane chlor-alkali cells achieving:
- 23% reduction in specific energy consumption (from 2,950 to 2,270 kWh/tonne NaOH)
- Caustic concentration increase from 32% to 33% with no additional evaporation energy
- $1.8 million annual savings despite $3.2 million capital investment
For hydrogen production, an offshore wind installation integrated pressurized PEM electrolyzers demonstrating:
- 84% capacity utilization leveraging variable renewable power profiles
- Production cost stabilization at $4.20/kg despite intermittent operation
- Seawater feedstock consumption reduced by 43% through closed-loop coolant systems
Aluminum smelters implementing next-generation inert anodes project 15-20% energy reduction equivalent to 3.5 TWh annual savings per 300,000 tonne facility.
Future Trajectories and System Evolution
Electrolytic cell innovation focuses predominantly on electrode architectures and separator technologies. Novel catalytic coatings incorporating iridium-ruthenium oxides have demonstrated 0.05 V overpotential reduction at 2 A/cm², potentially lowering PEM stack costs by 19%. Three key developmental vectors are emerging:
- Anion exchange membranes approaching 2.0 S/cm conductivity at reduced catalyst loading requirements
- Advanced computational fluid dynamics optimizing flow field designs, reducing pumping energy by 27%
- Machine learning implementations predicting electrode degradation with 95% accuracy
R&D pipeline analysis indicates emerging technologies will reach 85% system efficiency thresholds by 2030 while halving current capital expenditure requirements per installed capacity.
Selecting Appropriate Types of Electrolytic Cells for Operational Needs
Optimal electrolytic cell selection requires multidimensional analysis across four primary parameters:
- Economic Factors: PEM systems offer superior dynamic response but incur 2.5× higher stack replacement costs than alkaline
- Operational Environment: Molten salt cells remain unmatched for reactive metal production despite 18% efficiency limitations
- Scalability Requirements: Containerized alkaline systems deliver faster deployment while central SOEC installations achieve superior efficiency at scale
- Sustainability Mandates: Membrane chlor-alkali technologies have reduced mercury pollution by 97% since 1990
Industry benchmarking reveals properly maintained electrolytic installations operate profitably for 15+ years, with electrochemical processes now representing 36% of industrial hydrogen production and 100% of global primary aluminum manufacturing.
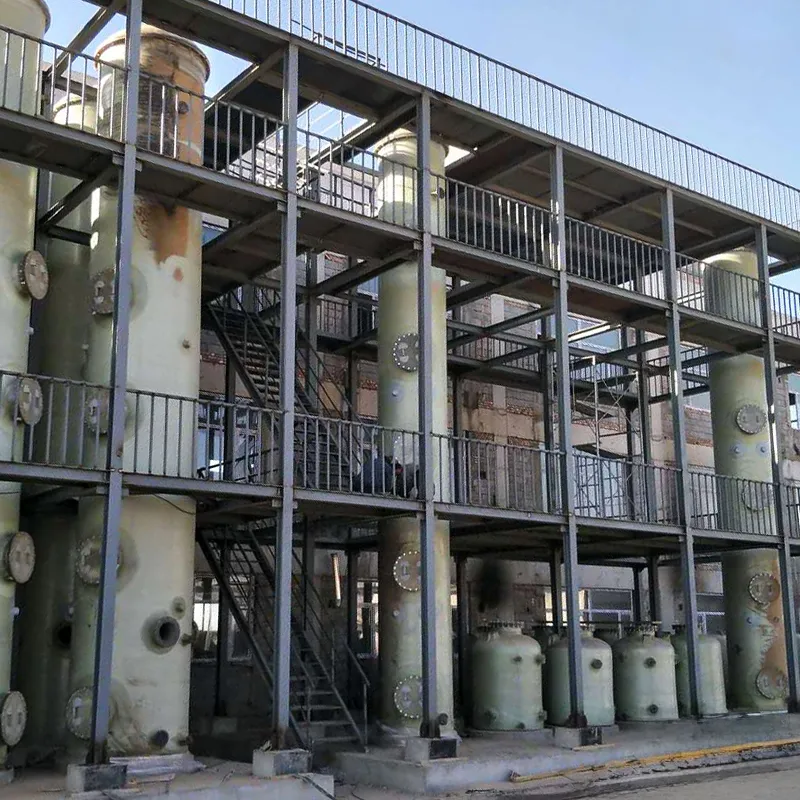
(types of electrolytic cells)
FAQS on types of electrolytic cells
FAQ: Types of Electrolytic CellsQ: What are the different types of electrolytic cells?
A: The main types include aqueous electrolytic cells, molten (fused) salt electrolytic cells, and diaphragm-based cells. Aqueous cells use water-based electrolytes for processes like metal refining, while molten salt cells operate with high-temperature salts to extract reactive metals like aluminum. Diaphragm cells separate electrodes to manage chemical reactions, such as in chlor-alkali production.
Q: How do the different types of electrolytic cells function?
A: Each type works by passing electric current through electrolytes to drive non-spontaneous redox reactions. For instance, molten salt cells decompose compounds like alumina into pure metals, while diaphragm cells use permeable barriers to isolate products like chlorine gas and sodium hydroxide. The electrolyte state (aqueous, molten, or separated) dictates the specific reaction pathway.
Q: What industries rely on various types of electrolytic cells?
A: Molten salt cells are vital in aluminum smelting, aqueous cells enable electroplating and refining of copper or zinc, and diaphragm cells produce industrial chemicals like chlorine. Clean energy sectors also use specialized electrolytic cells for hydrogen generation via water splitting.
Q: What distinguishes a diaphragm electrolytic cell from other types?
A: Diaphragm cells feature a physical barrier (e.g., asbestos or polymer membranes) separating anode and cathode compartments to prevent product mixing, unlike aqueous or molten salt cells that rely purely on electrolyte composition. This design is crucial for processes like sodium hydroxide synthesis, where chlorine gas must not contact the cathode products.
Q: Why are multiple types of electrolytic cells necessary?
A: Different electrolytic cells optimize conditions for target reactions—molten salts handle high-temperature metal extraction, aqueous solutions suit ion reduction in electroplating, and diaphragm setups ensure safe product separation. No single cell type can efficiently perform all electrolytic processes.