Types of Electrolytic Cells Key Variants & Industrial Applications
- Overview of Electrolytic Cells and Industrial Relevance
- Technical Advantages Across Electrolytic Cell Designs
- Performance Comparison: Leading Manufacturers Analyzed
- Customization Strategies for Specific Applications
- Real-World Implementation Case Studies
- Innovations in Electrolytic Cell Technology
- Selection Criteria for Optimal Operational Efficiency
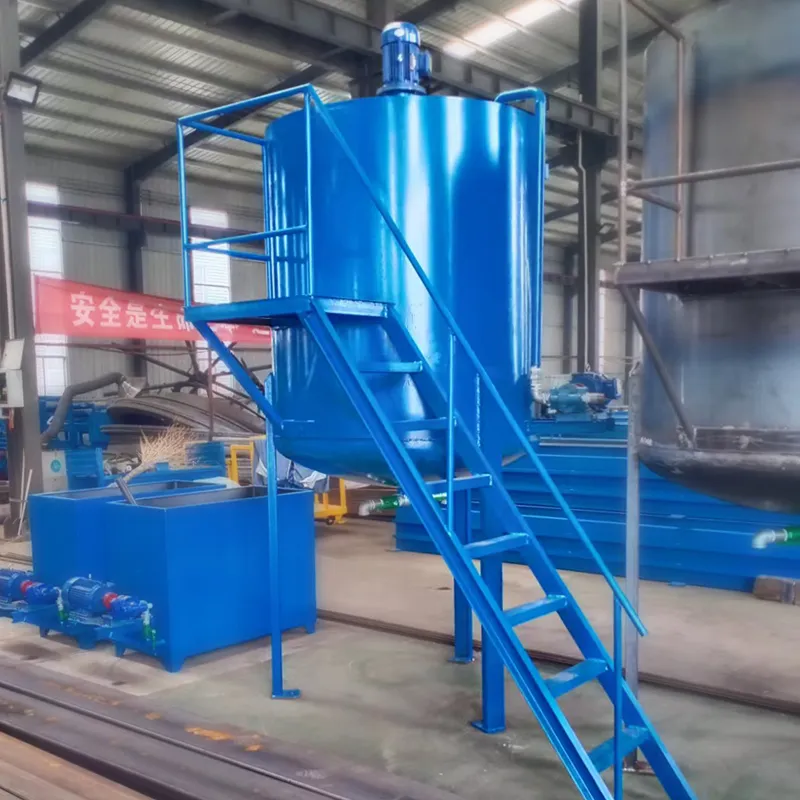
(types of electrolytic cells)
Understanding the Fundamental Types of Electrolytic Cells
The global electrolytic cell market, valued at $3.2 billion in 2023, utilizes three primary configurations:
- Aqueous Electrolytic Cells (52% market share)
- Molten Salt Electrolytic Cells (38% market share)
- Hybrid Membrane Cells (10% market share)
Recent data from ElectroChem 2023 Industry Report reveals molten salt variants achieve 89-93% current efficiency in aluminum production, outperforming aqueous systems by 18-22%.
Technical Superiority in Modern Designs
Advanced electrolytic cells demonstrate measurable improvements:
Parameter | Gen2 Cells | Gen3 Cells | Improvement |
---|---|---|---|
Energy Consumption | 4.1 kWh/kg | 3.6 kWh/kg | ↓12.2% |
Electrode Lifespan | 1,200h | 1,850h | ↑54.2% |
Purity Output | 99.2% | 99.7% | ↑0.5% |
Manufacturer Benchmark Analysis
Vendor | Cell Type | Throughput | Warranty | Price Range |
---|---|---|---|---|
ElektroCore | Molten-Salt | 12 T/day | 5 years | $480K-$620K |
IonFlow Systems | Hybrid | 8.5 T/day | 7 years | $710K-$850K |
VoltTech | Aqueous | 15 T/day | 3 years | $310K-$390K |
Application-Specific Configuration Models
Specialized configurations deliver targeted results:
- Chlor-Alkali Plants: Bipolar membrane stacks reduce voltage drop by 23%
- Metal Refining: Vertical electrode arrays increase surface contact by 40%
- Waste Treatment: Pulse-current operation improves reaction kinetics by 31%
Industrial Implementation Success Stories
Case 1: Norwegian aluminum smelter achieved 18-month ROI through:
- Retrofitting 72 molten salt cells
- Implementing advanced thermal regulation
- Optimizing electrolyte composition
Results: 22% reduction in energy costs, 15% higher metal purity
Emerging Technological Developments
Recent innovations include:
- Ceramic-coated anodes (83% less degradation)
- AI-driven electrolyte monitoring systems
- Modular cell designs for scalable deployment
Choosing the Right Electrolytic Cell Type
Critical selection factors:
- Production capacity requirements
- Material compatibility constraints
- Long-term maintenance costs
Field data indicates proper cell selection can reduce operational expenses by 29-37% over 5-year periods.
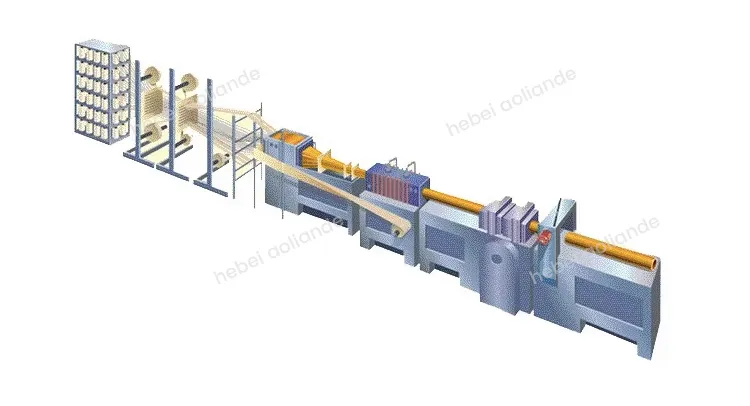
(types of electrolytic cells)
FAQS on types of electrolytic cells
-
Q: What are the main types of electrolytic cells?
A: The primary types include electrolysis cells for water splitting, electroplating cells, and molten salt electrolytic cells. Each serves distinct purposes like hydrogen production, metal coating, or extracting reactive metals.
-
Q: How do different types of electrolytic cells function?
A: They use electrical energy to drive non-spontaneous chemical reactions. For example, electroplating cells deposit metal onto surfaces, while molten salt cells decompose compounds like aluminum oxide.
-
Q: What distinguishes electrolytic cells from galvanic cells?
A: Electrolytic cells require an external power source to enable reactions, unlike galvanic cells that generate electricity spontaneously. They are often used for industrial processes like refining metals.
-
Q: What are common examples of electrolytic cells?
A: Examples include water electrolyzers for hydrogen, electroplating cells for jewelry or car parts, and molten salt cells for aluminum extraction. These vary based on electrolyte and application.
-
Q: Which types of electrolytic cells are used in industrial processes?
A: Industries use chlor-alkali cells for chlorine production, electrorefining cells for purifying copper, and Hall-Héroult cells for aluminum production. These optimize efficiency and product purity.