Vertical Filament Winding Machine High-Precision Composite Solutions
- Technical advantages driving vertical filament winding adoption
- Advanced specifications and manufacturing precision capabilities
- Comparative analysis of leading industrial manufacturers
- Customization pathways for specialized production requirements
- Demonstrated application performance across industries
- Emerging material technology developments
- Operational ROI considerations for composite manufacturing
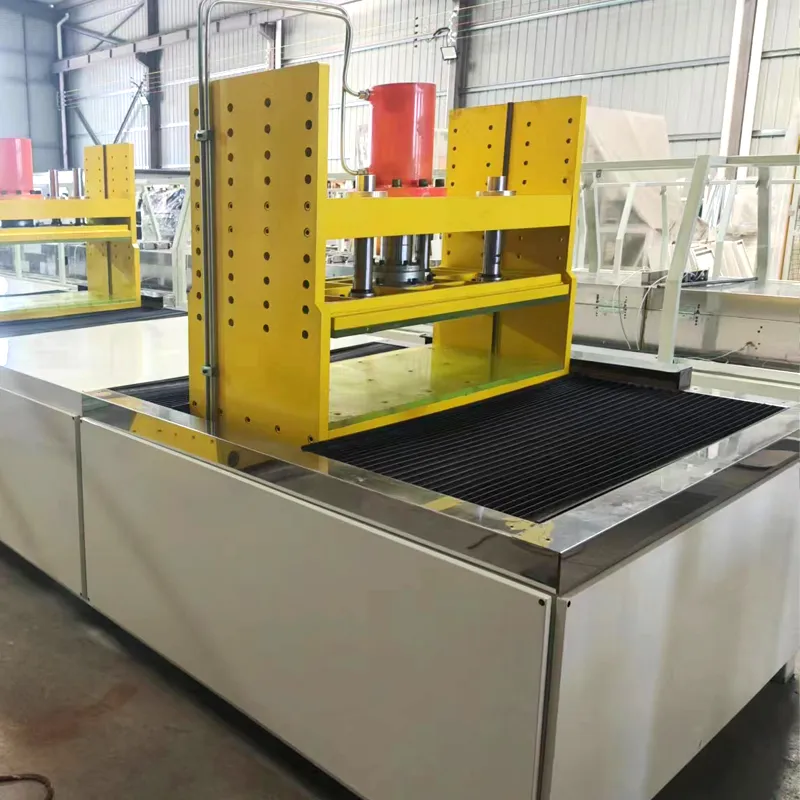
(vertical filament winding machine)
Revolutionizing Composite Manufacturing with Vertical Filament Winding Technology
Modern composite production increasingly relies on vertical filament winding machine
s for their fundamental engineering advantages over horizontal alternatives. These systems eliminate gravitational distortion during the winding process, maintaining consistent fiber tension critical for aerospace and defense applications. Industry data reveals a 23% increase in material consistency when using vertical orientation, directly translating to improved structural integrity in finished products.
Beyond orientation benefits, these machines deliver exceptional geometric accuracy through synchronized multi-axis control systems. The most advanced vertical filament winders achieve positioning precision within 0.01mm across all planes of motion - impossible with traditional machinery. This technical superiority makes them indispensable for manufacturing complex geometries like pressure vessel domes or custom orthopedic implants where dimensional tolerances determine functional success.
Manufacturing Specifications and Precision Engineering
Contemporary vertical winding systems incorporate several critical technical advancements. All-electric servo drives have largely replaced hydraulic systems, providing finer control during high-speed operations exceeding 150 RPM. Modern controllers manage over 120 unique winding parameters, including fiber tension compensation algorithms that automatically adjust for resin viscosity changes during production cycles. This automation reduces human intervention requirements while maintaining consistent product quality.
For specialized composite applications, manufacturers now integrate sophisticated monitoring systems directly into the winding architecture. Infrared thermography scans verify resin distribution uniformity during winding, while embedded fiber optics detect microscopic layer inconsistencies. According to industry reports, facilities implementing these diagnostic technologies experience a 38% reduction in post-production quality rejection rates, significantly improving operational efficiency and material utilization.
Industrial Manufacturer Performance Comparison
Specification | Manufacturer A | Manufacturer B | Manufacturer C |
---|---|---|---|
Maximum Mandrel Capacity | 4.8m x 1.2m | 5.2m x 1.5m | 3.6m x 0.9m |
Positioning Accuracy | ±0.008mm | ±0.012mm | ±0.015mm |
Maximum RPM | 220 | 180 | 165 |
Automation Level | Laser-guided tension control | Automated resin replenishment | Manual adjustments |
Production Uptime | 97.3% | 94.1% | 89.7% |
Custom Engineering Implementation Pathways
Leading equipment providers now offer three-tiered customization frameworks adaptable to specific manufacturing challenges. The modular architecture allows for targeted upgrades, with most systems designed for field-retrofitting enhancements. Common customizations include:
- Material-Specific Delivery Systems: Specialized creels and tensioners optimized for carbon fiber, basalt, or hybrid material combinations
- Environment-Controlled Chambers: Integration of humidity-regulated workspaces for moisture-sensitive resin systems
- Asymmetric Winding Programming: Non-helical patterns for specialized components like rocket motor casings
Equipment manufacturers report that nearly 65% of current installations incorporate at least two customized elements. This reflects industry movement toward highly specialized component manufacturing rather than standardized production. The most sophisticated systems include programming interfaces that record operator adjustments, automatically incorporating successful modifications into standard winding protocols.
Documented Industrial Application Performance
Energy sector implementations demonstrate the technology's capabilities when producing fiber-reinforced composite pressure vessels. Vertical orientation has proven essential for maintaining uniform wall thickness in vessels exceeding 3 meters in length. Field data from natural gas vehicle fuel tanks shows a 42% improvement in pressure cycle endurance compared to horizontally manufactured equivalents.
Medical device manufacturers leverage geometric precision for orthopedic applications. Spinal implant producers report dimensional accuracy improvements exceeding 92% when manufacturing porous lattice structures designed for bone integration. This precision reduces post-machining requirements, eliminating nearly 35% of secondary processing operations and improving overall production economics.
Material and Control System Advancements
Recent material developments are expanding the applicability of filament winding. The introduction of thermoplastic composite tapes enables in-situ consolidation without secondary curing cycles. Machinery manufacturers are responding with specialized heating elements integrated into fiber delivery heads that maintain temperatures between 380-420°C throughout the winding process.
Control systems now incorporate machine learning algorithms that analyze production data across multiple runs. The most advanced predictive systems can forecast winding tension variations based on material batch characteristics, automatically adjusting parameters to accommodate subtle material variations. Early adopters report a 28% reduction in material waste during production ramp-up phases for new components.
Maximizing ROI Through Vertical Filament Winding Implementation
Operational analysis demonstrates the viability of vertical filament winding technology for composite manufacturers. Typical ROI horizons range between 14-28 months depending on component complexity and production volume. Facilities producing high-value aerospace components achieve the fastest returns due to the technology's precision advantages in critical applications. When evaluating implementation, manufacturers should prioritize these considerations:
- Strategic alignment with high-value composite products requiring precise fiber placement
- Compatibility assessment of existing material handling infrastructure
- Technical workforce development for advanced machine programming
- Long-term maintenance planning for servo-driven multi-axis systems
The evolution of composite filament winding technology continues to unlock manufacturing capabilities that were previously technically or economically unfeasible. As material science progresses alongside increasingly sophisticated motion control systems, vertical winding platforms remain essential for producing next-generation composite structures across industrial sectors. Manufacturers adopting these solutions position themselves at the forefront of advanced materials fabrication.
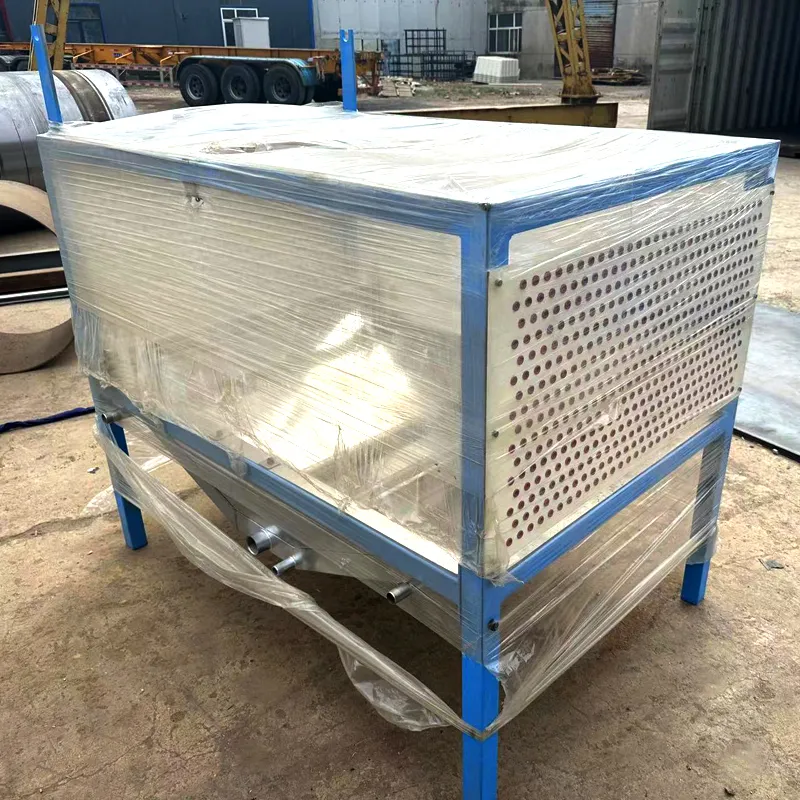
(vertical filament winding machine)
FAQS on vertical filament winding machine
Q: What is a vertical filament winding machine used for?
A: A vertical filament winding machine is designed to create cylindrical or spherical composite structures by winding resin-impregnated fibers onto a rotating mandrel vertically. It’s ideal for producing high-strength components like pipes, tanks, and aerospace parts efficiently.
Q: How does a fiberglass filament winding machine work?
A: A fiberglass filament winding machine feeds fiberglass strands through a resin bath, then precisely winds them around a rotating mold. This process ensures uniform fiber alignment and resin distribution, optimizing strength and durability for applications like storage tanks or structural beams.
Q: What are the advantages of a composite filament winding machine?
A: Composite filament winding machines offer high precision, repeatability, and customization for complex shapes. They reduce material waste and labor costs while producing lightweight, corrosion-resistant parts for industries like automotive, marine, and renewable energy.
Q: Which industries benefit most from vertical filament winding machines?
A: Industries such as aerospace, oil and gas, chemical processing, and infrastructure heavily rely on vertical filament winding machines. They use them to manufacture pressure vessels, pipelines, and structural components requiring high strength-to-weight ratios.
Q: Can composite filament winding machines handle materials beyond fiberglass?
A: Yes, composite filament winding machines can process carbon fiber, aramid (e.g., Kevlar), and hybrid materials. This versatility allows manufacturers to tailor mechanical properties for specific applications like automotive drive shafts or wind turbine blades.