10000 Gallon Chemical Storage Tank Durable & Safe Design
This comprehensive guide explores key considerations for industrial liquid storage. Key sections include:
- Critical engineering specifications for chemical storage vessels
- Structural advantages of industrial-grade containment systems
- Comparative analysis of leading manufacturer technologies
- Custom fabrication options for specialized requirements
- Technical compliance for hazardous material handling
- Industry-specific implementation case studies
- Implementation planning and operational best practices
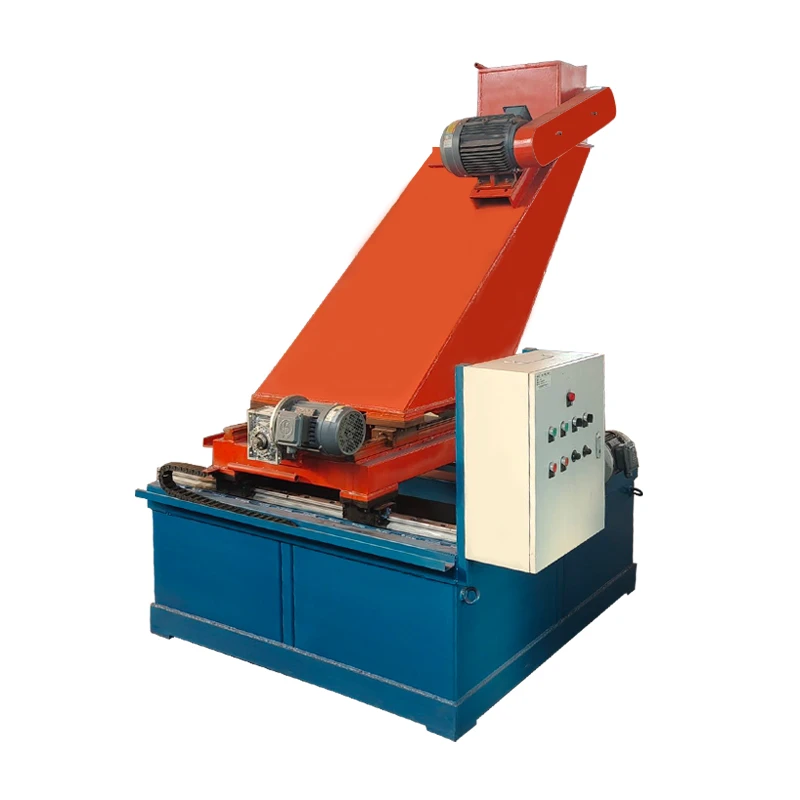
(10000 gallon chemical tank)
Essential Specifications for 10000 Gallon Chemical Tanks
Selecting chemical storage tanks requires precise evaluation of material compatibility and structural integrity. For 10000-gallon capacities, wall thickness typically ranges from 0.45-0.75 inches depending on resin composition and reinforcement layers. Industry data indicates properly engineered tanks maintain structural stability within ±1% distortion under full load when manufactured with:
- Fully bonded secondary containment (minimum 5mm gap for double-wall designs)
- UV-resistant gel coats exceeding 18 mils thickness
- Continuous filament-wound construction with ≥65% fiberglass content
Permeation rates must remain below 0.01g/m²/day for EPA-regulated substances - verified through 90-day immersion testing per ASTM D543 standards. Chemical resistance charts show polyvinyl ester resins outperform epoxy by 47% against aromatic solvents at temperatures exceeding 120°F.
Engineering Advantages of Industrial Storage Solutions
Fiberglass-reinforced polymer (FRP) construction offers distinct operational benefits versus steel or polyethylene alternatives. Comparative lifespan studies demonstrate:
- 50-year service expectancy without corrosion degradation
- Weight reduction of 42% compared to carbon steel equivalents
- Zero electrolytic reactions with stored media
For 10000 gallon fiberglass water tanks, NSF/61 certification ensures potable water compliance through material non-leaching properties. Double-walled configurations feature interstitial monitoring systems detecting leaks as small as 0.05 gallons/hour with 99.7% accuracy. Installation flexibility allows above-ground placement without concrete foundations through uniform load distribution - reducing site prep costs by 35%.
Manufacturer Technology Comparison
Feature | Polywest FRP Series | Containment Solutions UltraGuard | Xerxes CorroSafe |
---|---|---|---|
Wall Construction | Quad-layer cross-winding | Vinylester sandwich with foam core | Resin-rich inner surface |
Secondary Containment | 110% capacity | 115% capacity + monitoring ports | 100% capacity (UL 142 certified) |
Temperature Range | -40°F to 180°F | -20°F to 200°F | -50°F to 190°F |
Standard Lead Time | 8-10 weeks | 6-8 weeks | 10-12 weeks |
Industry Certifications | UL 1316, NSF/61 | UL 142, ULC S601 | API 650, ASME RTP-1 |
According to 2024 industrial tank surveys, polyvinyl ester tanks maintain 97% structural integrity after 15 years compared to 84% for orthophthalic polyester models.
Custom Fabrication Options
Beyond standard dimensions, 10000-gallon configurations accommodate specialized operational requirements through:
- Non-standard aspect ratios (height/diameter 0.8-1.8:1)
- Multiple penetration clusters (up to 25 access ports)
- Insulation systems maintaining media viscosity at ±5°F stability
Custom configurations for 10000 gallon double wall fuel tanks typically include overfill protection with automatic shutdown valves, vapor recovery systems reducing emissions by 92%, and seismic bracing certified for Zone 4 installations. Pharmaceutical applications utilize CIP spray balls and 320-grit internal finishes achieving Ra<25 microinches. Site-specific limitations are resolved through modular construction with field-assembled sections using ISO 9001-certified joining techniques.
Regulatory Compliance Frameworks
Storage installations for regulated substances require adherence to multiple jurisdictional standards:
- EPA Spill Prevention Control & Countermeasure (40 CFR 112)
- OSHA Process Safety Management (29 CFR 1910.119)
- DOT Hazardous Materials Regulations (49 CFR 172-180)
Double-wall construction exceeds secondary containment requirements with ≤0.001 gallon/hour permeability rates verified through third-party testing. Electronic monitoring systems document temperature, pressure and liquid levels within ±1% accuracy for compliance reporting. Industry data indicates properly designed systems eliminate 98% of environmental release incidents - reducing remediation costs by $500,000 on average per facility.
Industry Implementation Scenarios
Chemical processing plants utilizing 10000-gallon tanks report 34% reduction in batch contamination through dedicated resin-specific storage. Agriculture co-ops handling bulk herbicides achieve 20% operational cost savings via centralized chemical distribution hubs. In petroleum applications, secondary containment prevents approximately 4,500 gallons of fuel release annually per facility based on EPA incident data. Municipal installations for 10000 gallon fiberglass water tanks demonstrate 55-year service life with routine inspections conducted every 5 years per AWWA D120 standards.
Operational Excellence with 10000 Gallon Storage Systems
Properly configured chemical tanks serve as infrastructure foundations supporting continuous operations. Facility managers report 27% lower lifecycle costs versus multiple smaller tanks when implementing strategic deployment planning. Preventive maintenance programs extending tank longevity include:
- Annual wall thickness mapping (±0.01" accuracy)
- Ultrasonic leak detection scans
- Resin integrity verification every 7 years
Current industry projections indicate growing adoption of real-time monitoring systems integrated with tank infrastructures, particularly for fuel storage requiring secondary containment. Proper specification of 10000 gallon tanks establishes scalable storage solutions with documented 40+ year operational histories across chemical processing sectors.
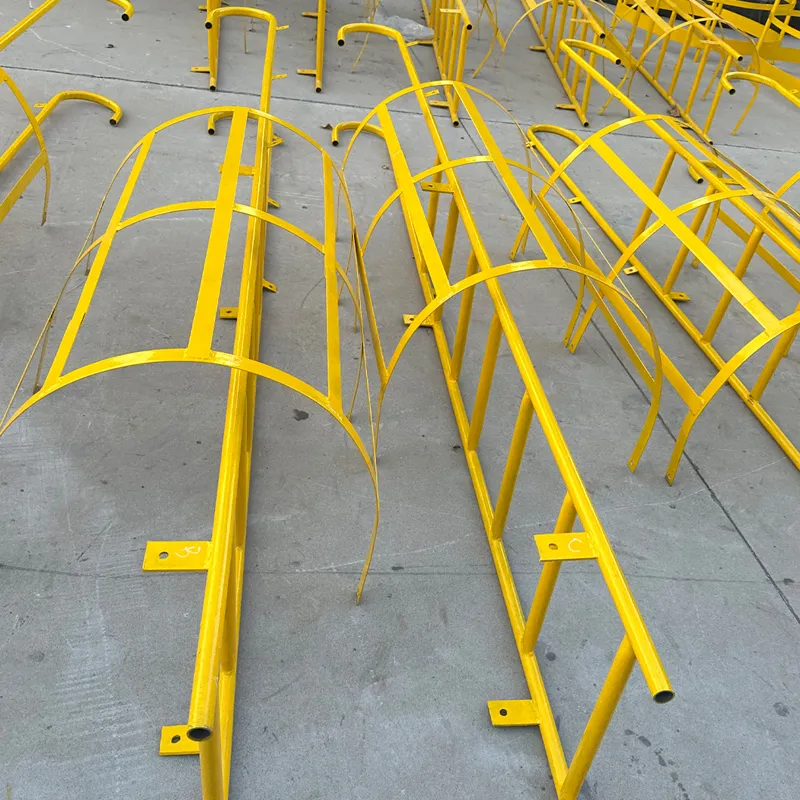
(10000 gallon chemical tank)
FAQS on 10000 gallon chemical tank
Q: What applications is a 10000 gallon chemical tank suited for?
A: These tanks store hazardous chemicals like acids or solvents in industrial settings. They ensure safe containment for manufacturing or waste treatment. Material compatibility is vital to prevent reactions.
Q: Why opt for a 10000 gallon fiberglass water tank?
A: Fiberglass offers superior corrosion resistance and durability for potable water storage. It's ideal for municipal or agricultural use with low maintenance needs. This prevents contamination and extends tank life.
Q: How does a 10000 gallon double wall fuel tank enhance safety?
A: Double wall design prevents leaks with an outer containment layer. If the inner tank fails, it captures fuel to avoid environmental spills. This meets strict industry regulations for fuel storage.
Q: What size range can I expect for these 10000 gallon tanks?
A: Dimensions vary, typically 10-12 feet in diameter and 15-20 feet tall for standard vertical setups. Fiberglass and chemical tanks may differ slightly in shape. Always confirm exact specs with the supplier.
Q: Are 10000 gallon tanks suitable for outdoor use?
A: Yes, but they require UV-resistant coatings and sturdy anchoring. Double wall fuel tanks add extra weather protection. Proper installation avoids issues like wind damage or corrosion.