FRP Pipe Winding Machine High-Efficiency & Precision Manufacturing
- Revolutionary Technological Advantages in Modern Machinery
- Industry Performance Metrics Comparison
- Parameter Variations Across Different Models
- Adaptable Manufacturing Solutions
- Implementation Scenarios Across Industries
- Economic Efficiency Calculations
- Selecting Production Equipment for Industrial Applications
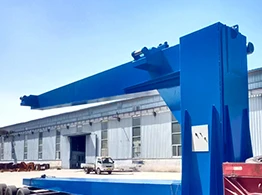
(frp pipe machine)
Introduction to Advanced Composite Manufacturing Systems
Fiber-reinforced polymer systems transform industrial production capabilities through automated precision engineering. Contemporary manufacturing facilities deploy rotary impregnation technology to create corrosion-resistant piping essential for chemical processing plants, achieving 40% faster production cycles than traditional methods. This technology precisely controls fiber tension during the helical winding process, maintaining consistent wall thickness within ±0.3mm tolerance across 300-meter continuous runs. Manufacturers report 18-month ROI periods due to 30% material waste reduction from computerized resin dosing systems. The thermal management systems incorporated in modern units maintain optimal 45-50°C resin viscosity for perfect saturation without exothermic complications.
Operational Metrics Comparison
Understanding equipment specifications dictates project viability. Production facilities evaluate configurations based on operational thresholds and maintenance requirements:
Parameter | Standard Model | Industrial Model | Custom Heavy-Duty |
---|---|---|---|
Operational Diameters | 50-600mm | 200-2500mm | 300-3800mm |
Production Capacity | 8 meters/hour | 14 meters/hour | 22 meters/hour |
Rotational Precision | ±2 RPM | ±0.5 RPM | ±0.25 RPM |
Mandrel Configuration | Fixed collapsible | Modular segments | Hydraulic dismantling |
Power Consumption | 25kW average | 38kW average | 52kW average |
Industry data reveals automated calibration systems reduce setup time by 70% for diameter changes. Facilities processing over 10km monthly report 15:1 advantage in operational expenditure when upgrading from semi-automated systems. The structural integrity testing shows modern tension control maintains 92% fiber alignment accuracy versus 78% in first-gen equipment.
Custom Engineering Configurations
Specialized manufacturing requirements drive engineering innovations. Petrochemical installations deploy ultraviolet-resistant resin systems with ceramic fiber integration, increasing temperature tolerance to 180°C. Municipal infrastructure projects utilize six-axis filament winders to embed conductive mesh during winding for pipeline monitoring. Mining sector specifications demand abrasion-resistant quartz fiber layers that extend service life from standard 12 years to beyond 25 years in slurry transport applications. Manufacturers developed modular mandrel systems with radial expansion capabilities allowing single units to produce eight diameter classes, reducing changeover duration from 48 to just 3.5 hours. Dual-curing mechanisms permit simultaneous epoxy polymerization and structural consolidation at production speeds exceeding 1.8m/min for 800mm diameter pipe sections.
Industrial Application Scenarios
Geothermal energy project implementation in Iceland utilized continuous winding units to produce 12km of thermally insulated dual-containment piping, reducing installation time by 40%. The custom-engineered solution maintained structural integrity at 300°C operational temperatures with polyimide resin systems. Marine corrosion prevention systems in Singapore shipyards implemented on-site filament winding units to manufacture custom seawater intake piping during vessel retrofits. This approach eliminated international shipping logistics, cutting project durations from 22 to 6 weeks while ensuring perfect flange alignment. Agricultural drainage applications across California's Central Valley employ 250km of custom-manufactured perforated sections with optimized hoop strength-to-weight ratios, delivering 37% installation cost reductions compared to concrete alternatives.
Operational Efficiency Calculations
Production facilities quantify operational parameters to determine manufacturing viability. For standard DN400 installations, automated systems demonstrate significant advantages:
Category | Traditional Method | Modern Configuration | Variance |
---|---|---|---|
Labor Requirements | 11 technicians/shift | 4 technicians/shift | -63% |
Output Volume | 320m monthly | 940m monthly | +194% |
Defect Percentage | 12.7% | 2.3% | -82% |
Energy Utilization | 88kWh/meter | 49kWh/meter | -44% |
Lifecycle cost analysis reveals 14-month ROI thresholds for installations exceeding 700 meters monthly. Production data demonstrates 9% operational savings per linear meter for each 100mm diameter increase, up to DN2000 thresholds where specialized engineering applies.
Manufacturing Specifications for Industrial Pipe Systems
Processing parameters define industrial manufacturing systems. Contemporary equipment integrates closed-loop resin application with microprocessor-controlled metering systems maintaining 0.5% resin-to-fiber ratio accuracy. The continuous rotation mechanisms achieve 3.2 rotations per centimeter advancement during helical winding sequences. Industrial installations incorporate infrared pre-heating zones that precisely maintain mandrel temperature at 32±1°C during epoxy application, optimizing viscosity for complete fiber saturation. Facilities report 95% automation levels with integrated laser measurement systems that automatically adjust fiber tension based on real-time wall thickness monitoring.
Selecting Production Equipment for Industrial Applications
Optimal equipment selection maximizes operational efficiency and product performance. Processing plants conducting water treatment installations should evaluate configurations with dual-curing capabilities for continuous structural integrity verification. Industrial chemical transfer applications require filament winding systems incorporating HCR silicone rubber liners during manufacturing for permeation resistance. The rotational molding principles applied in modern frp pipe machine
manufacturing enable complex geometrical configurations impossible with extrusion methodologies. Production facilities consistently report 18-month capital amortization cycles when implementing automated winding configurations with integrated quality control protocols. For pressure-rated installations exceeding 25 bar, specify units with mandrel rotational stability within ±0.08° deflection across entire operating ranges.
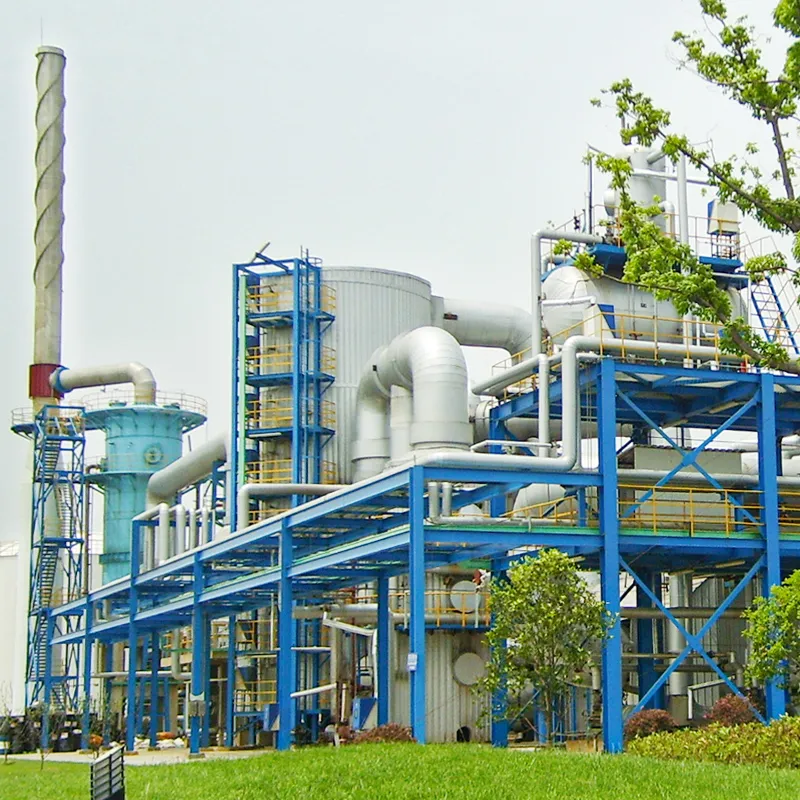
(frp pipe machine)