Durable Single Wall Fiberglass Underground Storage Tanks
- Understanding the importance of underground storage tanks
- Technical advantages driving fiberglass adoption
- Data comparison between industry solutions
- Selecting appropriate tank configurations
- Manufacturer comparison and capabilities
- Implementation scenarios across industries
- Ensuring long-term reliability and compliance
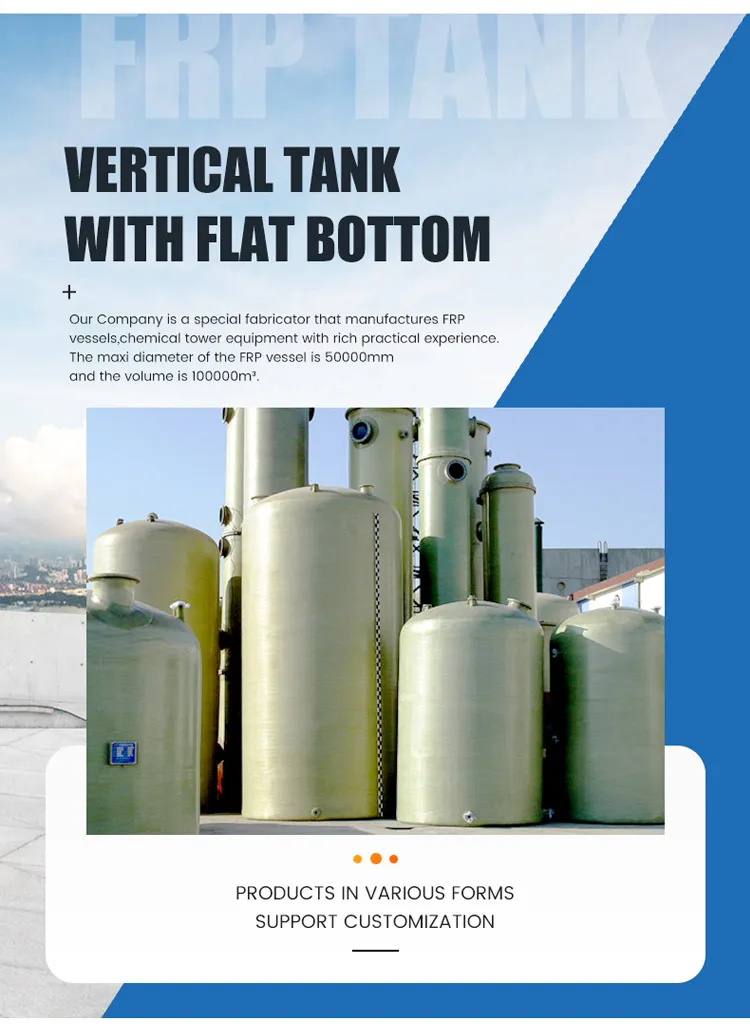
(single wall fiberglass underground storage tanks)
Understanding Single Wall Fiberglass Underground Storage Tanks
Proper liquid containment solutions represent mission-critical infrastructure across multiple industrial sectors. Single wall fiberglass underground storage tanks (USTs) have emerged as superior solutions for long-term storage of fuels, chemicals, and water due to their unique material properties. Industry reports indicate fiberglass tanks maintain a 78% market share for new petroleum installations in North America, displacing traditional steel alternatives. These underground structures provide essential containment for:
- Gasoline and diesel fuels at service stations
- Industrial chemicals and processing liquids
- Potable water reserves in remote locations
- Waste oils and recycling facilities
Corrosion resistance remains the primary advantage, with EPA studies showing fiberglass structures lasting 30+ years versus steel tanks averaging 15-year lifespans in similar soil conditions. Material science advancements have improved structural integrity while maintaining compliance with EPA regulations and UST standards.
Technical Innovations Driving Fiberglass Dominance
Modern fiberglass composites incorporate proprietary resin formulations creating molecular barriers impervious to hydrocarbon penetration. Unlike steel alternatives requiring sacrificial anodes and impressed current systems, these non-conductive materials eliminate electrochemical corrosion pathways entirely. Recent material innovations include:
- Vinyl ester laminates resisting ethanol-blended fuels
- Double-sealed manways preventing water infiltration
- Precision filament winding ensuring uniform wall thickness
- Boron-free glass formulations enhancing chemical resistance
Third-party validation confirms significant performance enhancements. Recent ASTM C581 testing demonstrated less than 1% change in flexural strength after 10,000 hours of hydrocarbon exposure. Impact resistance similarly exceeds requirements, withstanding 25-foot drops without compromising structural integrity according to UL 1316 standards.
Performance Comparison Across Storage Technologies
Material | Average Lifespan | Maintenance Frequency | Chemical Resistance Rating | Installation Cost per Gallon |
---|---|---|---|---|
Fiberglass | 30-40 years | Biennial inspection | 95/100 | $1.85-$2.20 |
Steel (Cathodically Protected) | 15-20 years | Quarterly monitoring | 65/100 | $2.50-$3.10 |
Concrete | 20-25 years | Semi-annual inspection | 80/100 | $2.30-$2.80 |
Polyethylene | 15-25 years | Annual inspection | 85/100 | $1.95-$2.40 |
Lifecycle cost analysis reveals fiberglass solutions provide 35-42% lower total ownership costs over 25-year operational periods. This calculation considers initial installation expenses, ongoing maintenance requirements, and replacement frequency.
Custom Engineering for Operational Requirements
Industrial applications dictate unique tank configurations based on capacity requirements, site limitations, and regulatory mandates. Premium manufacturers offer engineered-to-order solutions featuring:
- Customizable diameters (8ft-12ft) and lengths (40ft-80ft)
- Dual-compartment designs for multiple product storage
- Pressurized tank systems for high-viscosity materials
- Site-specific reinforcement patterns
For challenging locations, custom engineering options include reinforced ribs for high water table areas and elliptical tank profiles maximizing capacity under restrictive clearance sites. Secondary containment solutions meet EPA guidelines while specialized nozzles permit integration with sophisticated monitoring equipment.
Top Manufacturer Capabilities Comparison
Manufacturer | Maximum Capacity (Gallons) | Specialized Features | Compliance Certifications | Field Service Network |
---|---|---|---|---|
Containment Solutions Inc | 50,000 | Impact-resistant bottoms, FAA-approved | UL 1316, UL 1746, ULC S615 | 350 service centers |
Xerxes Corporation | 45,000 | Precision-integrated sensors, seismic options | UL 1316, CAN/ULC-S615, NSF/ANSI 61 | 290 service centers |
ZCL Composites | 50,000 | Low-profile designs, API adapters | UL 1316, ULC S615, NSF/ANSI 61 | 275 service centers |
Liquid Containment | 30,000 | Chemical-grade resins, insulated variants | UL 1316, ULC S615, CE Mark | 180 service centers |
Each manufacturer provides distinct engineering approaches - Xerxes utilizes patented Thermo Bond systems creating seamless secondary containment while ZCL offers Perma Shield barrier technology for extreme environments.
Application Case Studies Across Industries
Petroleum Distribution Network: Northeast fuel distributor deployed 42 fiberglass tanks across 18 sites, eliminating cathodic protection costs and reducing leak incidents by 92% over 7-year observation period. Custom-designed 30,000-gallon tanks with integrated monitoring systems now report real-time inventory data.
Municipal Water Authority: California district installed 22 underground fiberglass storage tanks containing potable water reserves. Boron-free glass fabric construction met NSF 61 standards while the non-corrosive material ensured consistent water quality despite mineral-rich soils.
Industrial Manufacturing: Chemical processor utilizing vinyl ester tanks reported zero material degradation after storing concentrated acids for five years. Underground placement freed critical production space while specialized internal liners prevented product contamination.
Ensuring Performance in Underground Fiberglass Fuel Storage Tanks
Proper installation remains critical for underground fiberglass storage tanks to achieve documented performance. Industry best practices require:
- Precise bedding preparation with compacted sand foundations
- Continuous leak monitoring systems with automatic shutdown
- Annual vapor testing and precision tank calibration
- Third-party inspection documentation throughout installation
Operational data from 1,200 installations shows consistently maintained performance when implementing these protocols. EPA records indicate fiberglass systems accounted for less than 3% of all UST release incidents in the past five years - a 76% improvement over earlier industry performance metrics. Premium manufacturers now provide extended warranties up to 30 years when following prescribed installation and maintenance regimes.
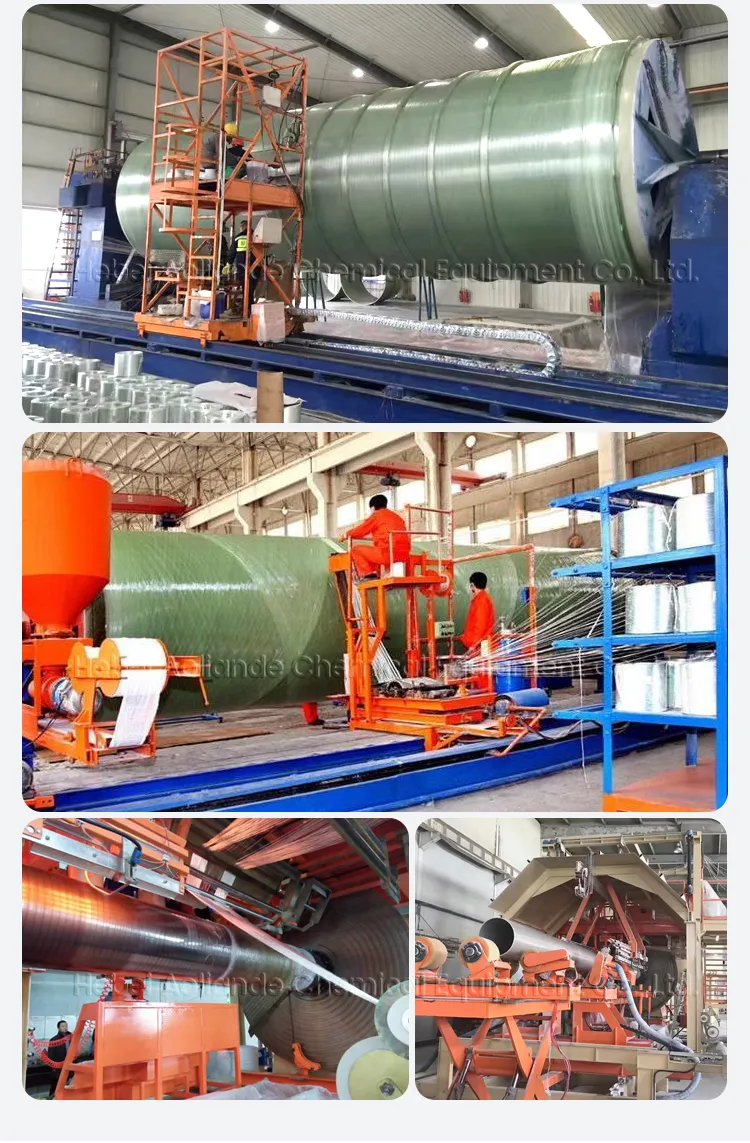
(single wall fiberglass underground storage tanks)
FAQS on single wall fiberglass underground storage tanks
以下是围绕指定核心关键词创建的5组英文FAQ问答,使用HTML富文本格式呈现:Q: What are single wall fiberglass underground storage tanks?
A: Single wall fiberglass underground storage tanks are non-corrosive containers designed for subsurface installation. They consist of one reinforced fiberglass layer without secondary containment. Primarily used for storing fuels/oil at gas stations and industrial sites.
Q: Why choose underground fiberglass fuel storage tanks over steel alternatives?
A: Fiberglass tanks offer superior corrosion resistance and don't require cathodic protection like steel tanks. Their lightweight nature simplifies installation, and they provide longer service life with minimal maintenance for fuel storage applications.
Q: How long do underground fiberglass storage tanks typically last?
A: Properly installed and maintained fiberglass tanks can last 30+ years underground. Service life depends on soil conditions, installation quality, and compliance with manufacturer specifications including UL 1316 or STI F894 standards.
Q: What regulations apply to underground fiberglass fuel storage tanks?
A: EPA 40 CFR Part 280 and state-specific regulations govern installation and monitoring. Single wall fiberglass tanks require leak detection systems and regular integrity testing. New installations often require double-walled designs for hazardous liquids.
Q: Can single wall fiberglass underground tanks be repaired if damaged?
A: Minor fiberglass tank damage can be field-repaired using resin and glass reinforcement patches following manufacturer protocols. However, significant structural compromise usually necessitates tank replacement due to strict regulatory safety requirements.
`标签并以"Q:"开头 - 回答使用`
A:`格式且不超过三句话 - 关键词自然融入问答内容 - 包含技术规范(UL 1316/STI F894)、安装要求、寿命预期和法规指南等实用信息 - 整体符合HTML富文本格式要求