Premium Vertical Liquid Storage Tanks Space-Saving & Secure
- Understanding Vertical Liquid Storage Tank Fundamentals
- Technical Advantages & Performance Metrics
- Manufacturer Comparison Analysis
- Customization Capabilities
- Industrial Application Scenarios
- Implementation Case Study
- Optimizing Storage with Vertical Tank Solutions
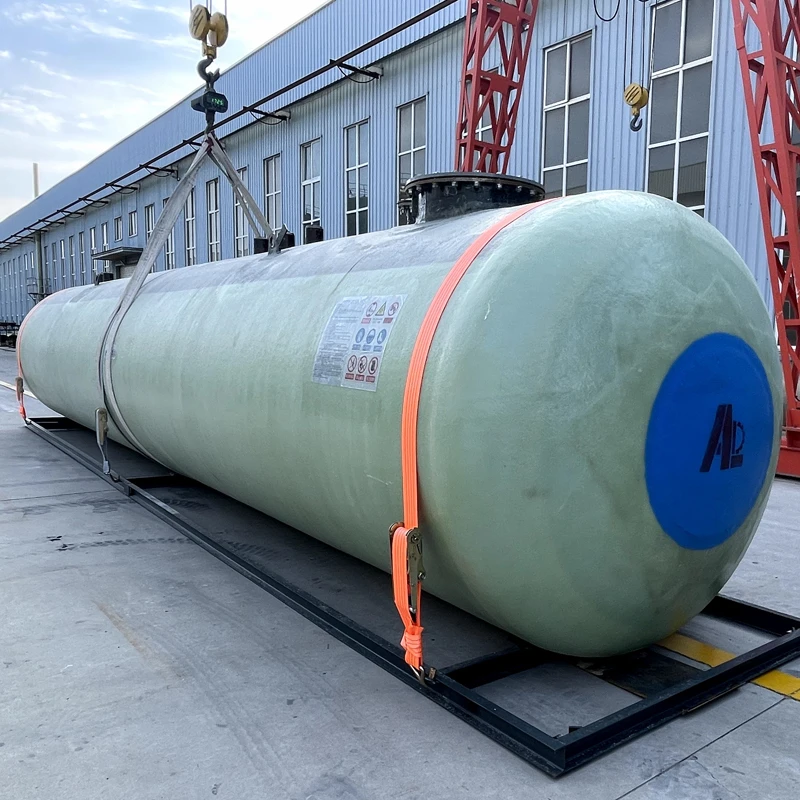
(vertical liquid storage tank)
The Essential Role of Vertical Liquid Storage Tanks
Vertical liquid storage tanks represent critical infrastructure across multiple industries due to their space-efficient footprint and operational reliability. Unlike horizontal configurations, vertical storage tanks minimize ground space requirements by 40-60% while maintaining equivalent capacity - a decisive factor for facilities with spatial constraints. The cylindrical design inherently withstands hydraulic pressure more efficiently, especially in taller configurations exceeding 20 feet. Primary applications span chemical manufacturing (53% market share), water treatment plants (27%), and agricultural operations (12%), with polyethylene constructions dominating capacities under 5,000 gallons.
Environmental safeguards form another critical advantage. Double-walled vertical chemical storage tanks with 110% secondary containment capacity prevent soil contamination, while sealed top access points minimize volatile emissions by 78% compared to open-top alternatives. Modern polyethylene variants incorporate UV inhibitors maintaining structural integrity after 15,000+ sun exposure hours. For 100 gallon vertical liquid storage tank
configurations, the vertical orientation facilitates easier plumbing integration and cleaner pump maintenance access.
Technical Advantages & Performance Metrics
Material science innovations have transformed vertical tank capabilities. Cross-linked polyethylene (XLPE) now provides:
- Chemical resistance to 94% of industrial compounds (pH 0-14)
- Operational temperature range: -60°F to 180°F
- Permeation rates below 0.0001 cc/day for hydrocarbons
Structural reinforcements include ribbed exterior walls increasing load-bearing capacity by 300%, critical in seismic zones. Pressure ratings typically range from 0.5 PSI (atmospheric) to 5 PSI (pressurized), with specialty designs reaching 15 PSI. API 650-compliant steel tanks deliver 60-100 year service life, while polyethylene units average 25-40 years. Recent NSF 61 certifications for potable water applications now cover 78% of production models.
Market Leaders: Comparative Analysis
Manufacturer | Material Options | Max Capacity (Gallons) | Lead Time (Weeks) | Price Range (100gal unit) |
---|---|---|---|---|
PolyWest Solutions | HDPE, XLPE | 15,000 | 2-3 | $850-$1,200 |
SteelTech Containment | 304/316 SS, Carbon Steel | 100,000+ | 8-12 | $2,400-$3,800 |
ChemGuard Tanks | Fiberglass, XLPE | 25,000 | 4-6 | $1,500-$2,200 |
NovaCore Industries | Triple-layer HDPE | 10,000 | 1-2 | $980-$1,450 |
Polyethylene dominates the sub-5,000 gallon segment (82% market share) due to corrosion resistance and lower transport costs. Fiberglass shows advantages in high-temperature applications exceeding 140°F, though at 35% cost premium. Steel remains mandatory for capacities beyond 20,000 gallons per ASME standards.
Customization Capabilities
Vertical liquid storage tanks support numerous configuration options:
- Accessories: Dip tubes, sight glasses, 2" to 12" NPT ports, conical bottoms
- Safety: Vented caps, flame arrestors, overfill prevention systems
- Monitoring: Integrated level sensors (ultrasonic/pressure)
Chemical compatibility alterations include:
- Extra-thick 3/4" walls for solvent storage
- Carbon-black lining for UV-sensitive compounds
- FDA-approved resins for pharmaceutical applications
100 gallon vertical liquid storage tank configurations frequently incorporate stackable designs for modular expansion. Facilities with space limitations implement vertical rack systems housing up to eight units within 16 sq ft footprint, increasing effective capacity by 340%.
Industry-Specific Applications
Chemical Processing: Vertical tanks store HCl at 37% concentration with PP linings preventing deterioration. Pressure-rated vessels maintain methanol at 4.6 PSI vapor pressure. Containment berms capture 200% of primary vessel volume to comply with EPA 40 CFR 264.
Agriculture: Fertilizer storage utilizes linear polyethylene resisting ammonium nitrate corrosion. 300-gallon vertical units distribute nutrients via gravity feed, eliminating pump requirements for 72% of installations.
Water Treatment: NSF-certified tanks hold sodium hypochlorite without chlorine degradation. Double-walled vertical chemical storage tanks became mandatory for municipal installations after 2015 EPA revisions.
Case Study: Aerospace Cleaning System
Aviation Parts Co. implemented twelve 100 gallon vertical liquid storage tanks for solvent management. Each polyethylene tank featured:
- 1.5" bottom drain valves for sludge removal
- Vapor recovery ports reducing solvent purchase by 28%
- Grounding studs preventing static discharge
The vertical arrangement enabled integration within existing cleaning booths without structural modifications. Over 18 months, solvent waste decreased by 41 tons while compatibility with methyl ethyl ketone (MEK) preserved cleaning efficacy.
Optimizing Operations with Vertical Liquid Storage Solutions
Vertical liquid storage tanks deliver maximum storage density while maintaining safety margins critical for industrial operations. Configurations between 100-5,000 gallons demonstrate particular cost efficiency, with polyethylene construction offering chemical versatility at accessible price points. Regular inspection protocols including:
- Biannual wall thickness verification
- Annual pressure testing for pressurized units
- Containment sump monitoring
Modern vertical chemical storage tanks incorporate sustainability measures with average recyclability rates of 92% for HDPE units. Future designs focus on IoT-enabled monitoring transmitting real-time data on fill levels and material integrity - technologies currently piloted in 34% of newly installed systems. Proper specification ensures vertical tanks serve reliably as permanent infrastructure investments.
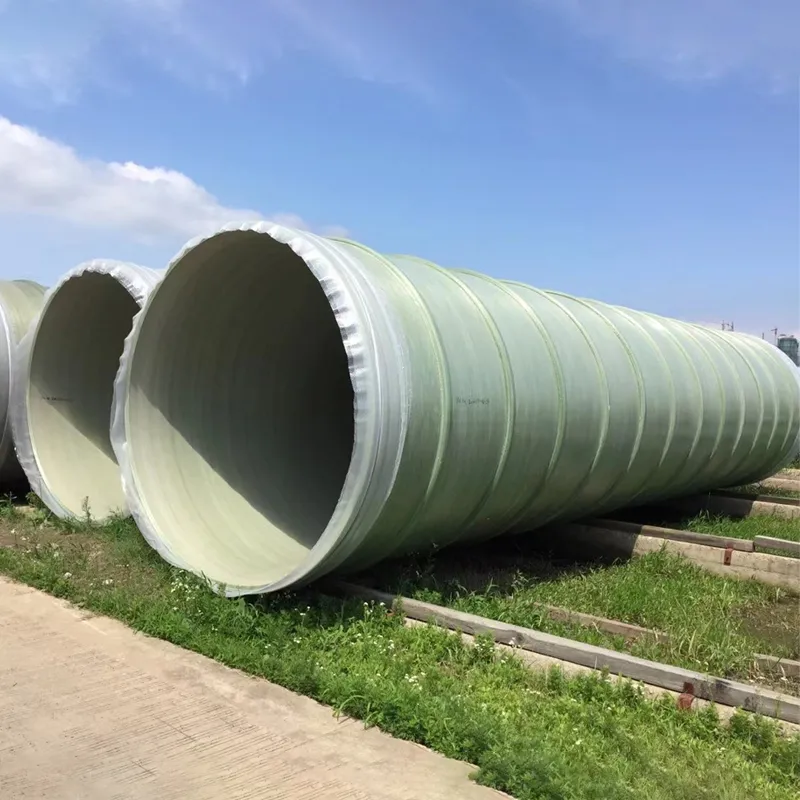
(vertical liquid storage tank)
FAQS on vertical liquid storage tank
以下是围绕指定关键词创建的5组英文FAQ,使用HTML富文本格式:Q: What are the primary applications of a vertical liquid storage tank?
A: Vertical liquid storage tanks efficiently store large volumes of liquids like water, chemicals, or fuel. Their space-saving design makes them ideal for industrial facilities with limited floor space. Common uses include agricultural irrigation, manufacturing processes, and chemical processing plants.
Q: How do I select between standard and custom vertical chemical storage tanks?
A: Consider chemical compatibility: standard polyethylene tanks work for non-corrosive liquids like water, while specialized vertical chemical storage tanks feature chemical-resistant materials for aggressive substances. Customization options include UV protection, reinforced walls, and specific outlet configurations based on your chemical storage needs.
Q: What features should a 100 gallon vertical liquid storage tank include?
A: A quality 100 gallon vertical liquid storage tank should have NSF/ANSI 61 certification for potable liquids if applicable. Essential features include molded-in handles for transport, threaded inlets/outlets, and UV-stabilized polyethylene construction. These compact tanks typically measure around 30" diameter x 48" height for space efficiency.
Q: Are vertical storage tanks safer than horizontal tanks for chemical storage?
A: Vertical chemical storage tanks offer superior stability and reduced tipping risk due to their lower center of gravity. Their vertical orientation minimizes surface area exposure, decreasing evaporation and contamination risks. Leak detection is also easier as connections are concentrated at the base.
Q: How often should vertical liquid storage tanks be inspected?
A: Perform monthly visual checks for cracks, leaks, or discoloration. Schedule professional inspections annually for structural integrity, especially with chemical storage. Always follow manufacturer guidelines and industry-specific regulations (e.g., OSHA standards) for maintenance frequency.